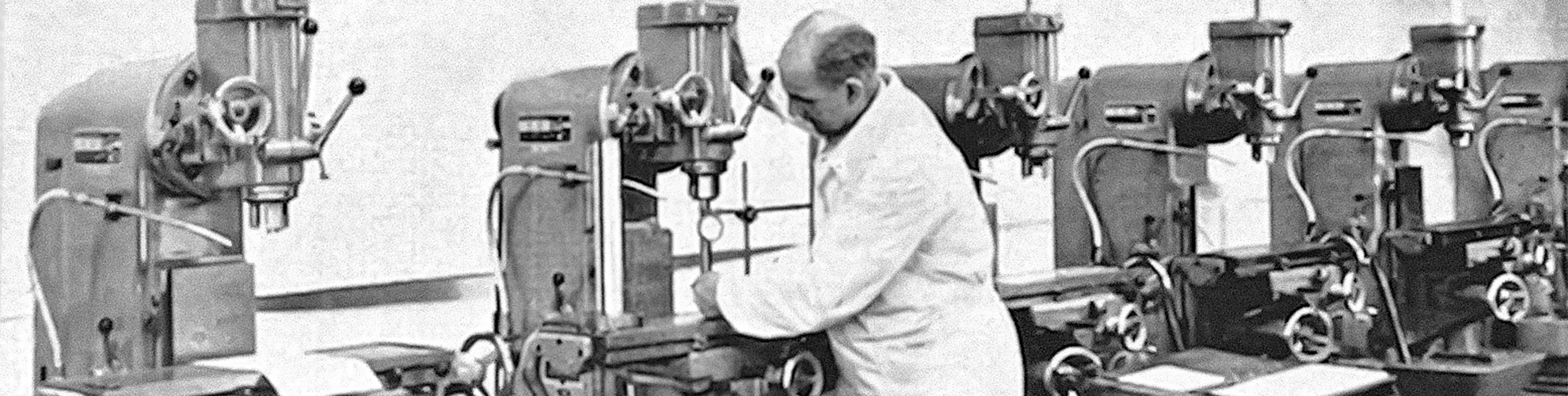
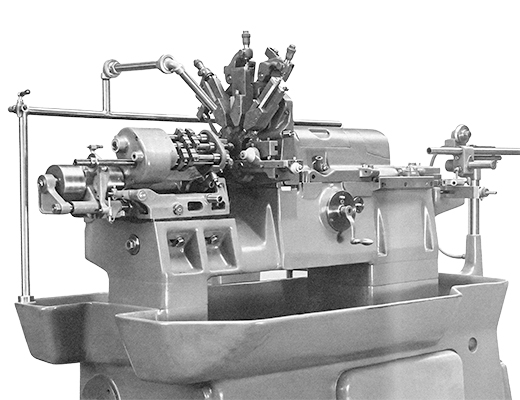
De los patines de hielo a la máquina de producción
La fábrica propiamente dicha arranca con una máquina que fabrica las anillas de sujeción de los muelles tensores de los relojes. Se trata de un gran paso para esta pequeña y joven empresa, dado que la nueva máquina permite fabricar piezas con una enorme demanda en la industria relojera: cada muelle de reloj necesita una de estas anillas. Hasta ese momento las anillas se fabricaban a mano en el marco de un proceso muy laborioso que no permitía producir grandes cantidades. Pero la máquina de Steinel lo cambia todo. Puede producir día y noche sin parar.
Esto le viene muy bien a la industria relojera de Schwenningen, dado que necesita las piezas en grandes cantidades para satisfacer una demanda que no deja de crecer. La fabricación de relojes empezó siendo una industria artesanal a mediados del siglo XIX, se convirtió en la principal industria de la ciudad y en la actualidad es el motor económico principal de la región. La innovación técnica que trae consigo la industrialización se incorpora al arte de fabricar relojes, y Schwenningen se convierte en un centro neurálgico de la mecánica y la ingeniería de precisión, que a su vez favorece el desarrollo de máquinas y utillajes en otros sectores. El propio Bernhard Steinel ha trabajado varios años en la industria relojera antes de crear su propia empresa. Friedrich Mauthe, Thomas Haller, Schlenker y Kienzle son grandes fabricantes de relojes y las principales empresas del sector.
Leer másLa primera taladradora multihusillo del mundo
Poco a poco el panorama empresarial va mejorando y Steinel vuelve a centrarse en la ingeniería mecánica. El joven empresario contrata a su primer técnico en 1927. Sus conocimientos les permiten acelerar cada vez más el ritmo de innovación. Precisamente en 1927, la empresa alcanza uno de su grandes hitos con el desarrollo y la fabricación de la primera taladradora multihusillo del mundo. Este producto dará origen a un catálogo completo de maquinaria para la industria mecánica. El viento sopla a favor. A la primera taladradora multihusillo le siguen las taladradoras de cuatro husillos y las roscadoras. Más tarde, el pequeño equipo produce también remachadoras de martillo, bruñidoras de rodillos y fresadoras de curvas. La demanda es tal, que el espacio se les vuelve a quedar pequeño para la gran cantidad de máquinas que necesitan producir.
Pero la nueva expansión se topa con otra crisis económica. Esta vez se trata de la Gran Depresión de 1929/30, que afecta a toda la economía mundial. La gente no tiene dinero para comprar productos y la demanda se desploma. De un día para otro las calles de Schwenningen y de toda Alemania se llenan de miles de hombres y mujeres que se han quedado sin trabajo. Muchas empresas de la industria relojera tienen que reducir las jornadas de sus empleados para sobrevivir. No es el caso de Bernhard Steinel. "Yo nunca dejé de trabajar", recordará décadas después. Estaba convencido de que después de una depresión viene un boom, y no se equivocó. Así, a Steinel le llueven los pedidos. Hace negocios incluso con los rusos, a los que les vende bruñidoras de martillo y taladradoras. La demanda de estas máquinas es alta. Tan alta, que la fábrica no tiene suficiente capacidad para atender todos los pedidos. La solución: introducir un segundo turno y contratar a más operarios para que las máquinas trabajen a pleno rendimiento durante más tiempo. Dado el alto nivel de desempleo existente, resulta muy fácil encontrar buenos profesionales. Tras la crisis, Steinel cuenta con una plantilla formada por quince mecánicos y tres aprendices perfectamente preparada para hacer frente a la elevada demanda. En 1930 la fábrica se vuelve a quedar pequeña. Steinel compra la finca de al lado, conocida como Frick-Fabrik, y empieza a construir remachadoras. Cada año fabrica y vende entre 800 y 900 máquinas.
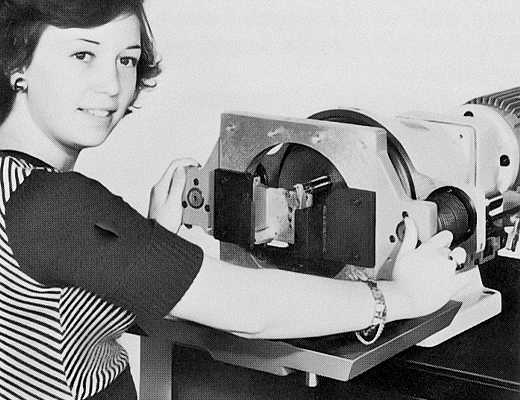

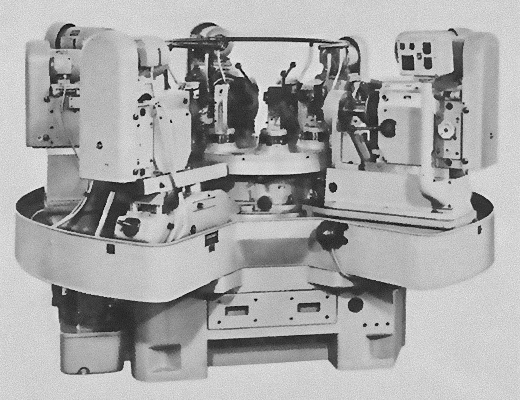
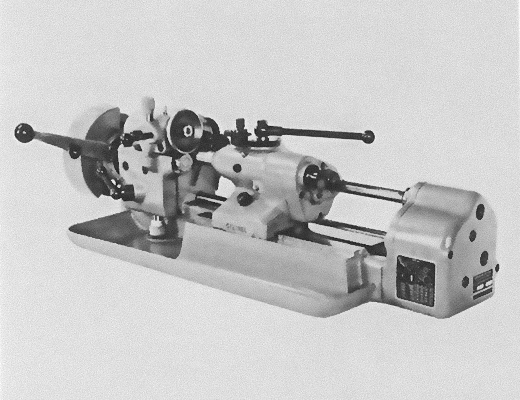
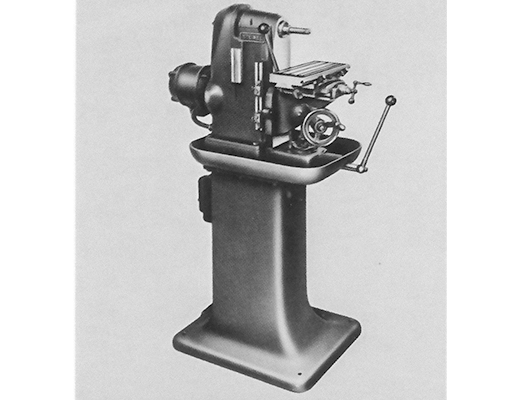
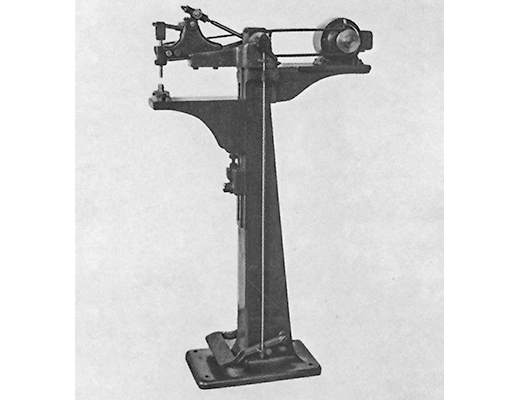
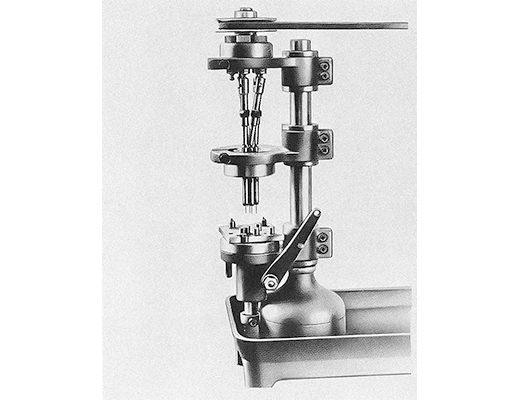

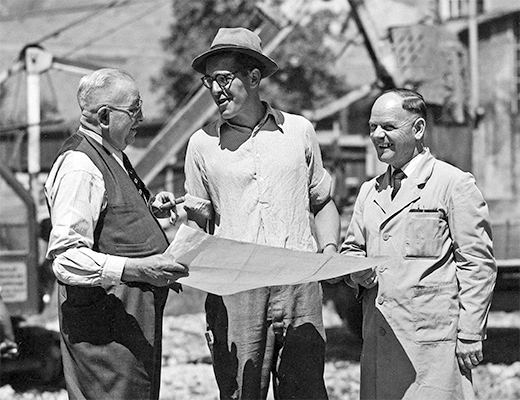
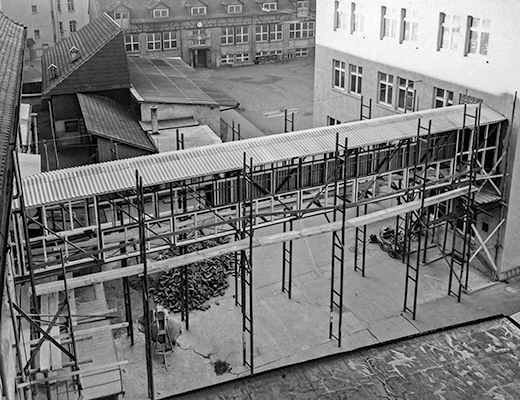
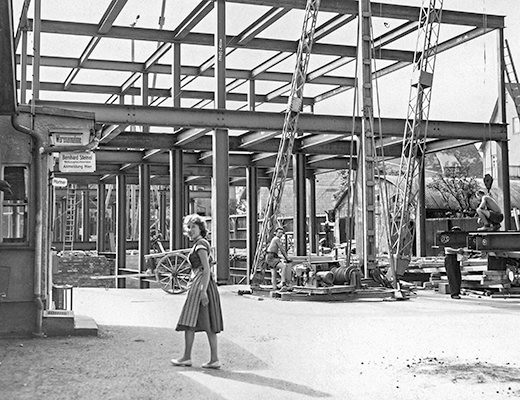
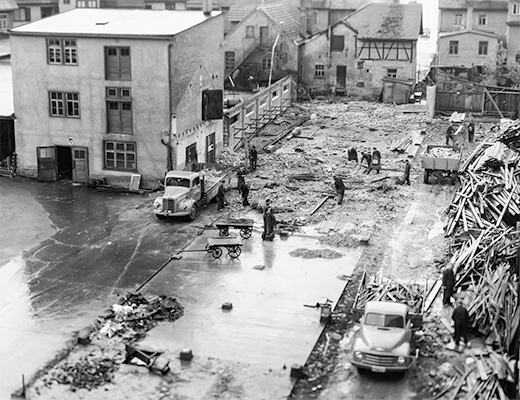
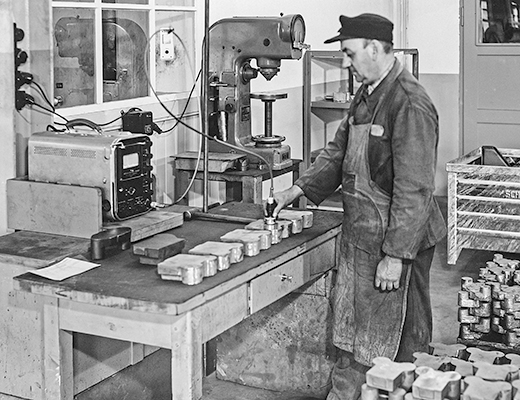
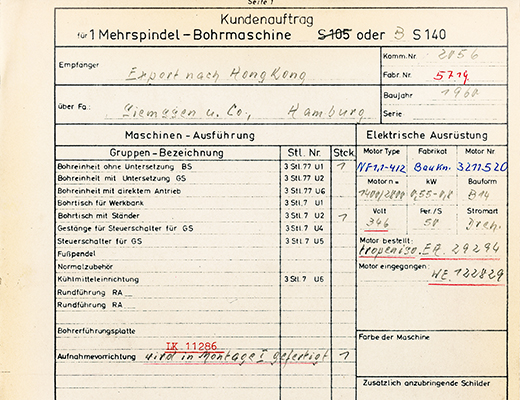
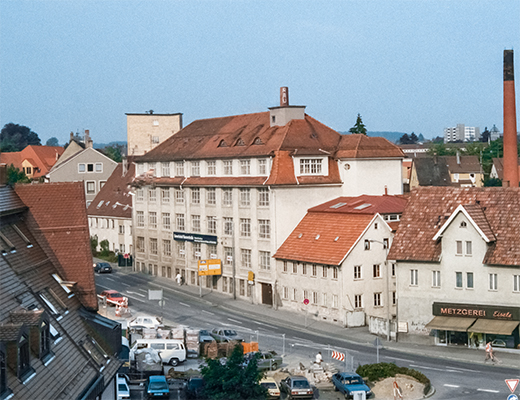
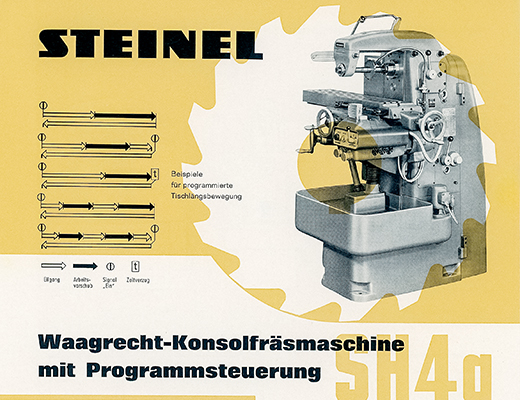
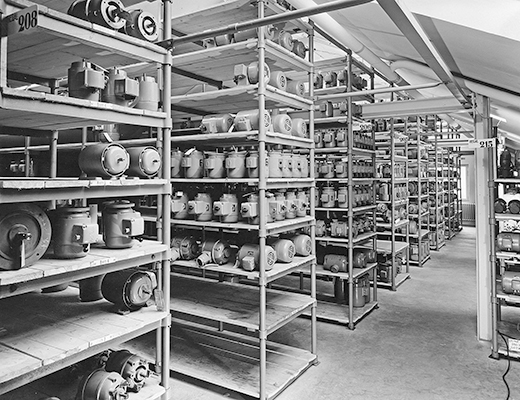
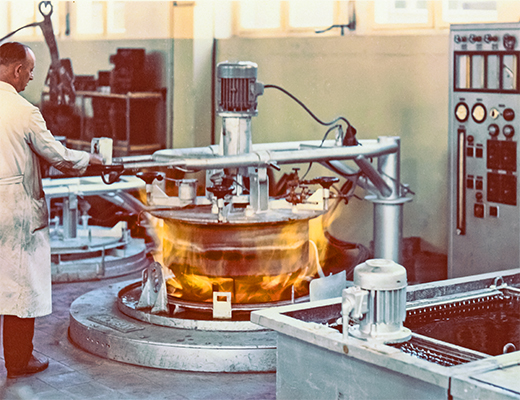
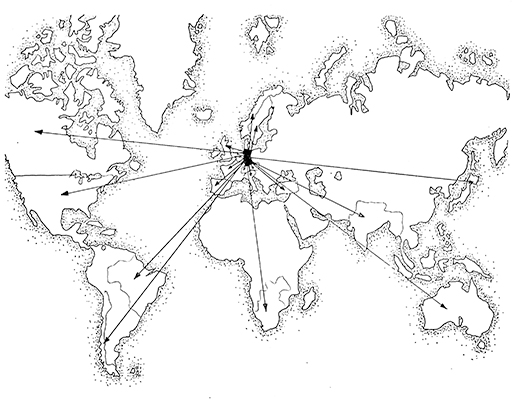
La innovación tecnológica impulsa el crecimiento
Aunque la confiscación de los equipos de producción ha generado un grave perjuicio, Steinel sigue trabajando y retoma el catálogo de antes de la guerra. En un inicio salen del centro de producción en pequeñas cantidades máquinas de fresado, máquinas multihusillo, taladradoras compactas, pulidoras de pivotes y de piñones y remachadoras. Pero eso no es todo: la empresa retoma y mejora la gama de componentes modulares desarrollada durante la guerra. En poco tiempo está en condiciones de suministrar once normalizados con un total de 130 productos. Un apunte: décadas después siete grupos de productos con 465 normalizados cubrirán un total de 25.000 productos. Steinel ofrece una amplísima gama de productos que va desde el casquillo guía más pequeño hasta bastidores de columnas de gran tamaño.
Leer másEl primer ordenador IBM
"Los maestros de producción reciben cada lunes un plan de trabajo semanal impreso", reza el periódico local de diciembre de 1970. Y es que ahora, el ordenador planifica cada semana la secuencia temporal de entre 3000 y 4000 fases de trabajo en la producción. De este modo se determina la secuencia en la que los 260 grupos de máquinas deben procesar las piezas. Steinel se vuelve a colocar en la vanguardia con la incorporación del primer ordenador IBM. La fábrica de máquinas herramienta es la primera empresa de toda la región de Schwarzwald-Baar-Heuberg que cuenta con un flujo de procesos calculado casi al completo por ordenador. "Para nosotros no es posible avanzar sin el uso de un sistema informático de este tipo", afirma el jefe de la empresa, Bernhard Steinel hijo, durante la presentación del ordenador en la sucursal de IBM de Villingen. Con esto el empresario está diciendo que el sistema garantiza una producción más rentable porque se hace un aprovechamiento óptimo de las máquinas. También, que se acortan los plazos de entrega y se cumplen rigurosamente. Steinel invierte grandes sumas en esta mejora de la eficiencia: la empresa paga a IBM 30.000 marcos al mes por el alquiler del ordenador. Es un coste alto teniendo en cuenta que en esa época un trabajador medio gana unos 1.000 marcos al mes. No obstante, con el aumento de la productividad esta gran inversión queda sobradamente amortizada. El ordenador tiene otra gran ventaja: nunca se cansa. Además, trabaja básicamente cuando el personal ya está disfrutando de su fin de semana. A partir del viernes por la tarde, funciona a toda velocidad y distribuye las tareas para las máquinas de la semana siguiente.
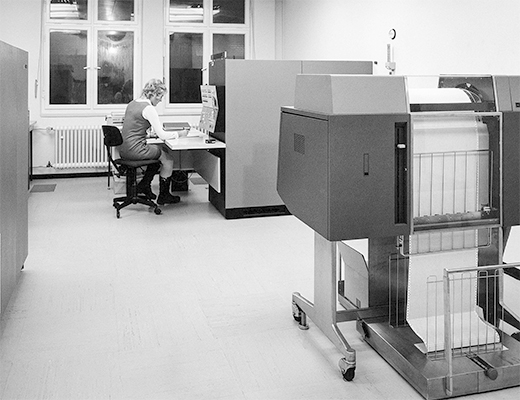
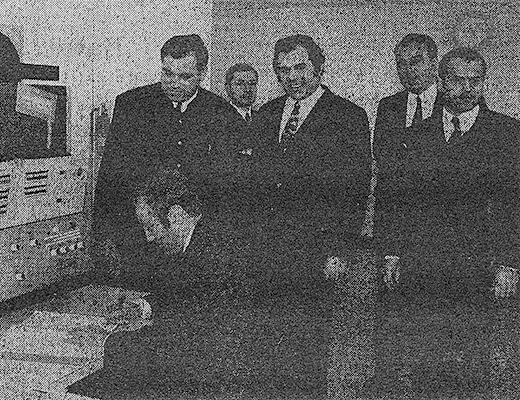
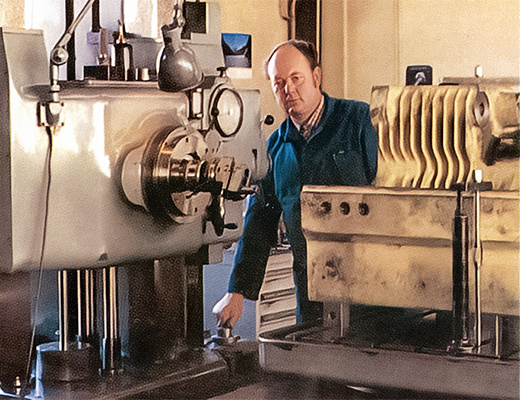
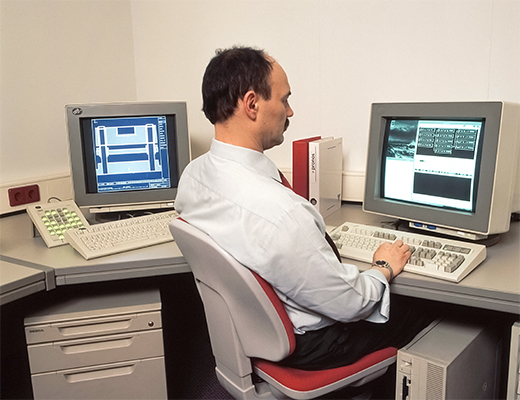
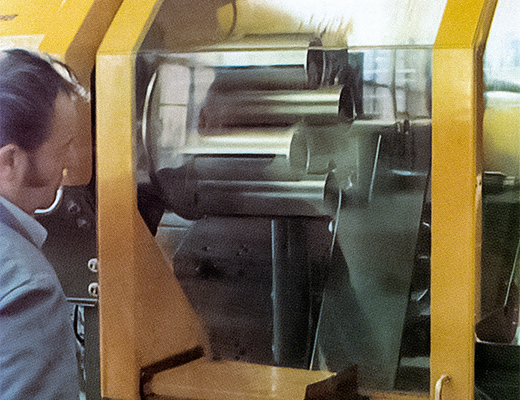
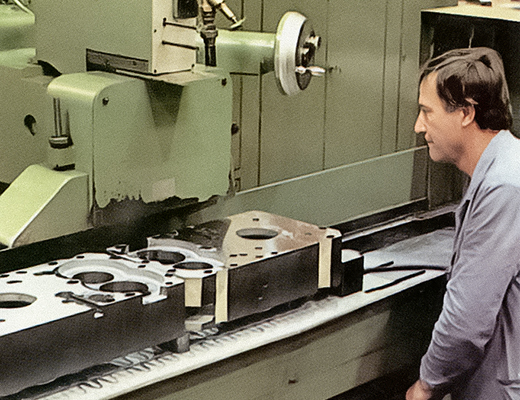

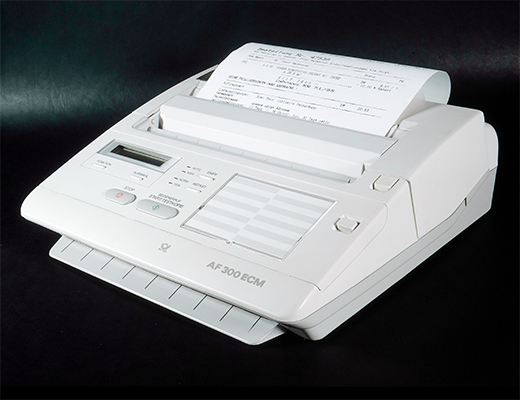
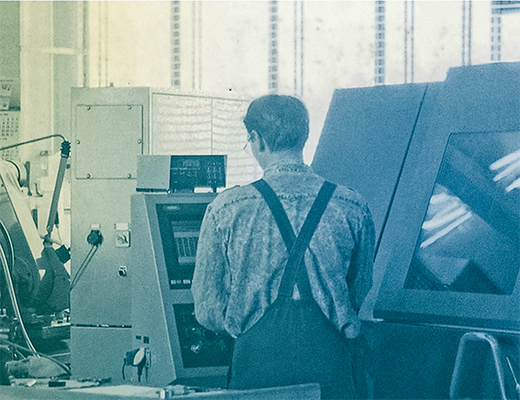
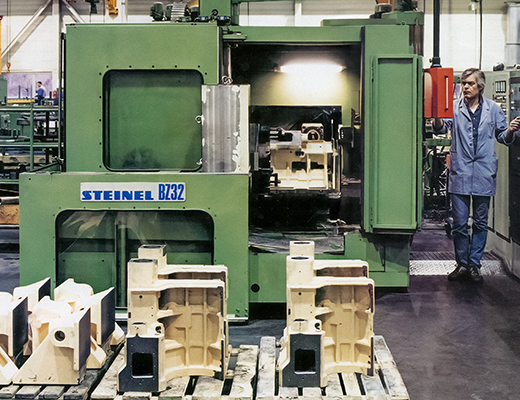
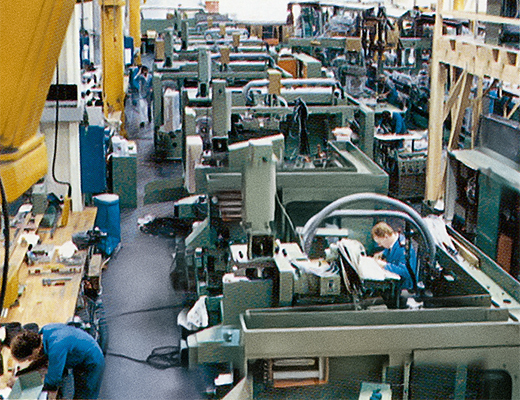
Mayor nivel de precisión gracias a las máquinas CNC
Las máquinas CNC se empiezan a popularizar y cada vez se utilizan más. Son máquinas herramienta controladas por ordenador que permiten procesar el material con una gran exactitud. Los componentes pueden fabricarse con un alto grado de precisión y repetibilidad. La gran ventaja que ofrecen frente a las máquinas manuales es que funcionan de forma autónoma y realizan muchas tareas sin intervención humana una vez que el programa está en marcha. Gracias al control por ordenador, las máquinas son extremadamente precisas y pueden realizar trabajos complicados y delicados sin errores, incluso con repeticiones masivas.
Por otro lado, los primeros ordenadores personales aún tardarán mucho en llegar. El primer PC se instala en el departamento de ventas en abril de 1990. Los distintos departamentos tienen asignados horarios fijos en los que pueden utilizar el ordenador. Para facilitar la comunicación se utiliza un fax con papel térmico que se entrega al destinatario mediante un sistema interno de tubos neumáticos. En el año 2001 este sistema se sustituye por el correo electrónico, que ha tardado en implantarse por razones de seguridad.
Steinel entra en el sector de la construcción de instalaciones industriales
Gracias a la amplia y sólida experiencia de sus ingenieros de diseño y de sus empleados, Steinel se considera preparada para pasar al siguiente nivel y adentrarse en el sector de la construcción de instalaciones industriales. Es un paso de gigante hacia el futuro que permite a la empresa ofrecer a sus clientes industriales instalaciones llave en mano. Steinel se ocupa de todo el proceso, desde el abastecimiento de las materias primas hasta la producción, pasando por los ensayos y el montaje físico de la instalación. Para materializar estos complejos proyectos, los ingenieros de Steinel utilizan tanto sus propios equipos como máquinas de otros fabricantes. La empresa cuenta con una amplia experiencia sobre todo en la planificación de sistemas para la producción de tubos, manguitos, brocas y barrenas para la extracción de petróleo y gas. La demanda de este tipo de soluciones es alta en todo el mundo. Con sus tornos CNC y sus taladradoras de agujeros profundos, centros de mecanizado especiales, máquinas de montaje y una amplia gama de sistemas de ensayo y medición, Steinel suministra e instala sus sistemas en Austria, Japón, Estados Unidos e incluso en la Unión Soviética.
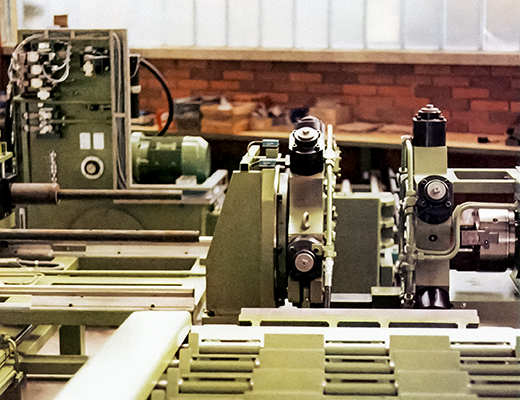

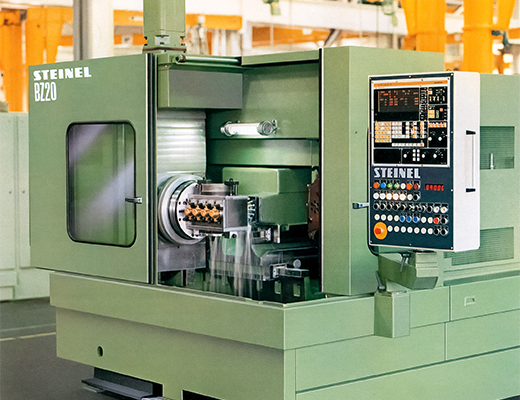
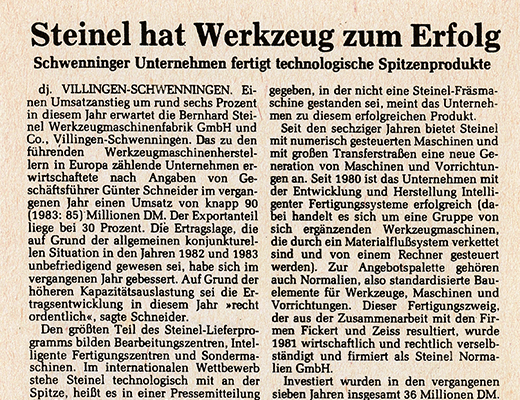
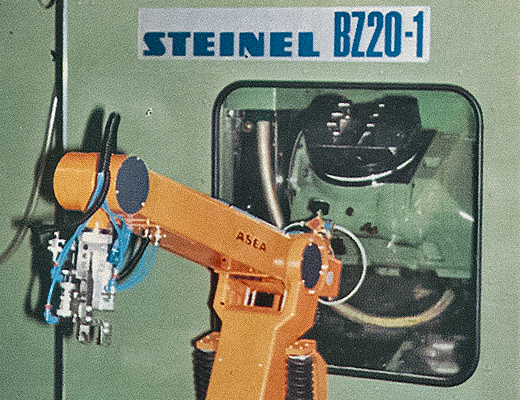
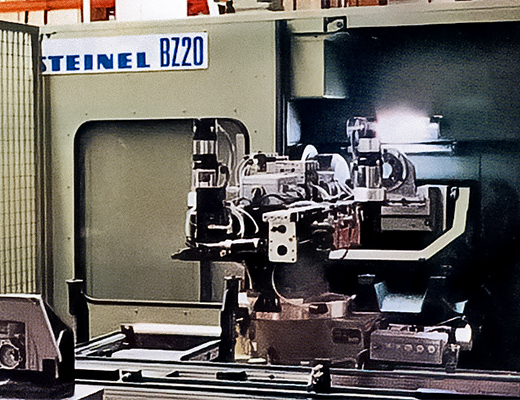
Máquinas controladas por ordenador
La casa Zeiss solicita a Steinel su participación en un proyecto pionero como fabricante de sistemas de producción inteligentes. Así, desarrolla un sistema piloto de fabricación flexible que puede procesar 150 piezas distintas. Y lo hace gracias a una instalación controlada por ordenador con cuatro centros de mecanizado BZ 20 combinados con un dispositivo de cambio de palets, un almacén de palets con 30 alojamientos, un punto de carga y descarga, un carro de transporte controlado por CN y una máquina de medición.
Este innovador sistema despierta un gran interés cuando se presenta al público especializado. En ese mismo año y también en 1984 Steinel desarrolla un sistema de fabricación flexible para Bosch. Consta de cuatro centros de mecanizado BZ 20 y otros cuatro BZ 25 con 80 cabezales de doble husillo conectados entre sí mediante un sistema modular de transporte de palets que se cargan y descargan con dispositivos de manipulación. Pero la cosa no acaba aquí, dado que a estos grandes clientes se suman otros muchos que encargan sus propios sistemas de fabricación flexible con un diseño similar. Y en todos los proyectos Steinel responde con solvencia gracias a su dilatada experiencia en la construcción de máquinas especiales y tecnología NC, dos disciplinas que Steinel combina a la perfección para satisfacer los requisitos más exigentes y fabricar centros de mecanizado cada vez más productivos. Para ello, utiliza cabezales de taladrado multihusillo y avance automático de piezas, además de integrar unidades NC y el cambio automático de herramientas para aportar una mayor flexibilidad a las máquinas especiales.
La primera página web de un proveedor alemán de normalizados
En 1997, internet era todavía un territorio inexplorado y lleno de misterios para muchas empresas alemanas. Las páginas web eran una rareza y la idea de que las empresas pudieran presentar sus productos y servicios en línea se antojaba bastante extravagante. Pero mientras unos dudaban, Steinel decidía adentrarse en la era digital y convertirse en el primer proveedor de normalizados en dar el salto a la red.
El dominio .de se introdujo en 1986, pero apenas se utilizó hasta principios de los noventa. No fue hasta 1995 cuando empezaron a establecerse sitios web comerciales, y en 1996 se lanzaron portales web muy conocidos, como T-Online.de. Al año siguiente aparecieron las primeras ofertas de bancos y tiendas online, y a partir de 1998 el número de sitios web también se disparó en Alemania debido sobre todo a la popularización de las conexiones DSL a internet.
Orgullosa de su lema "50 años de calidad: siempre un paso por delante", Steinel dejó claro desde el principio que la innovación y la visión a largo plazo eran valores fundamentales de la empresa. La primera página web tenía un diseño sobrio y acorde con las posibilidades técnicas, pero su contenido era rompedor. Con el título "Nuestro catálogo de productos para sistemas de troquelado y conformado", Steinel presentaba su gama de productos de forma claramente estructurada: bastidores de columnas de aluminio y acero, elementos de guía, elementos de corte, elementos de muelle, accesorios y elementos de máquinas.
La sección "Quiénes somos" era uno de los apartados más destacados de la web. En ella Steinel no solo transmite información, sino también, y sobre todo, solvencia y confianza: una oferta integral de la mano de un solo proveedor, una calidad superior constante, un almacén central con 25.000 productos y un servicio de entrega fiable.
Tener un sitio web propio era tan inusual en aquella época que el periódico local "Neckarquelle" publicó una serie de artículos sobre las pocas empresas que ya tenían presencia en internet. Steinel pertenecía a aquel exclusivo grupo de pioneros digitales de Schwenningen.
En una época en la que sólo existían entre 5.000 y 10.000 sitios web alemanes y la presencia en internet se limitaba básicamente a las universidades y las grandes empresas como BMW y Deutsche Telekom, Steinel envió un mensaje claro: el futuro era digital. Con un sistema de información de producto electrónico en CD-ROM, conexión CAD y el moderno software WorldCAT para la búsqueda de productos y la tramitación de pedidos, Steinel no sólo demostró tener audacia, sino también una profunda comprensión de las oportunidades que ofrecía el mundo digital.
Hoy, casi treinta años después, la presencia de Steinel en internet es un elemento clave de la estrategia empresarial. Y es que el espíritu pionero de 1997 sigue muy vivo: el hecho de haber sabido identificar el potencial de Internet es otra prueba de que Steinel sigue siendo fiel a su filosofía de ir siempre un paso por delante, de estar siempre en primera línea. Es un ejemplo real de cultura corporativa con visión de futuro.
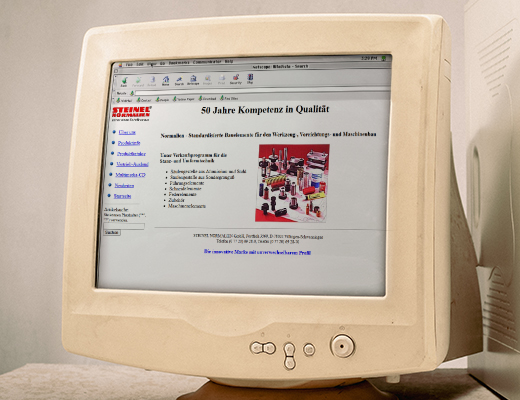
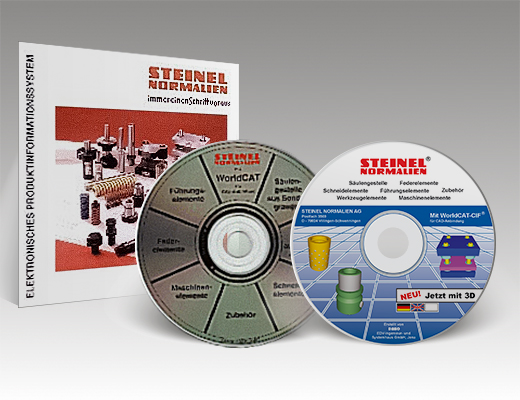
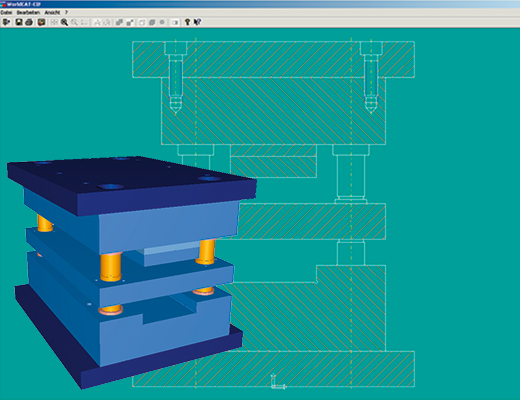
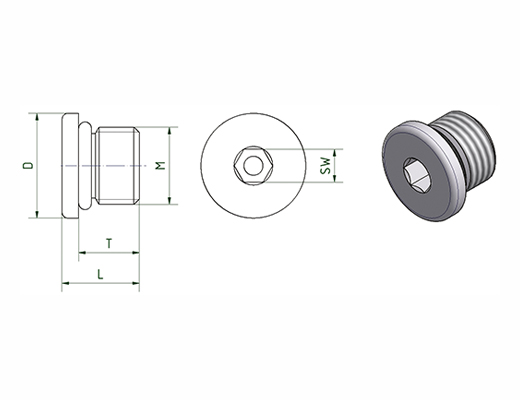
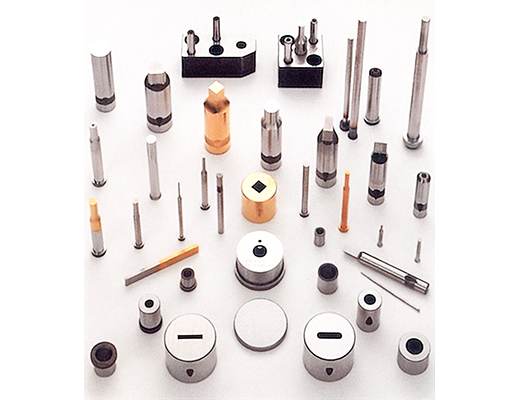
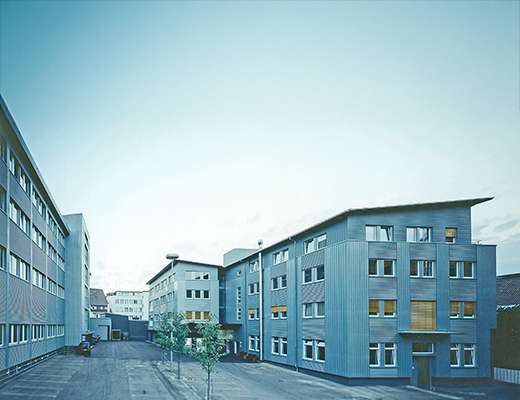
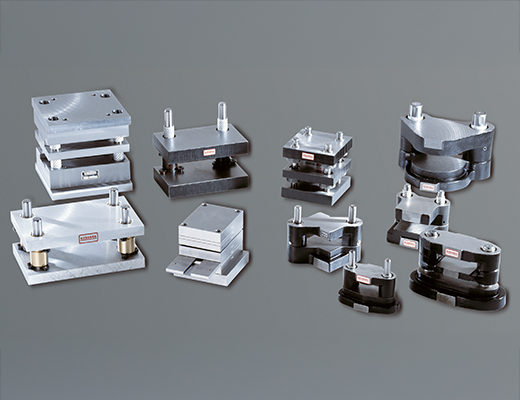
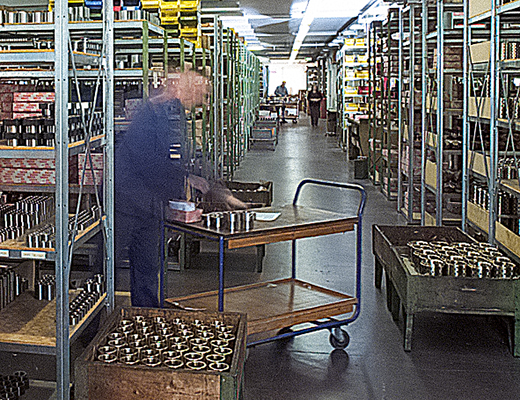
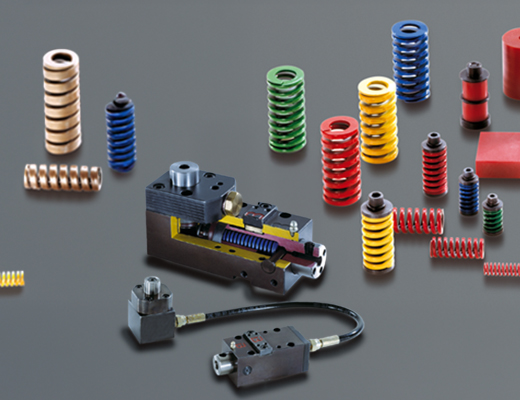
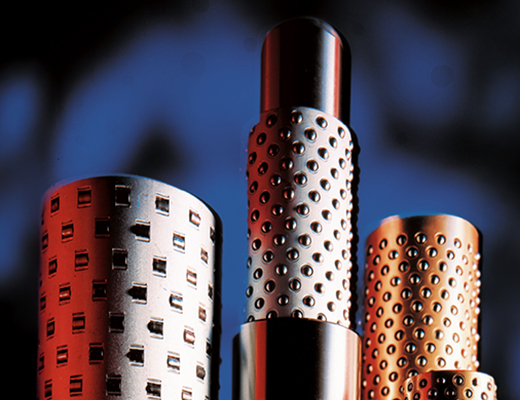
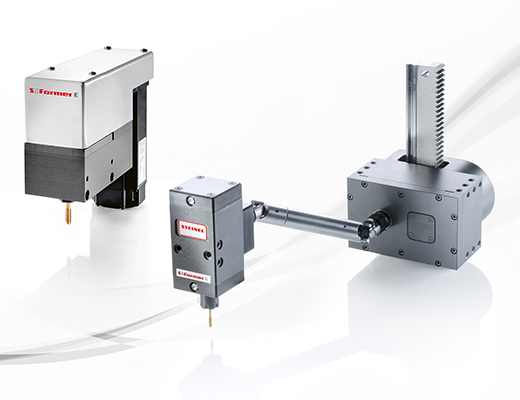
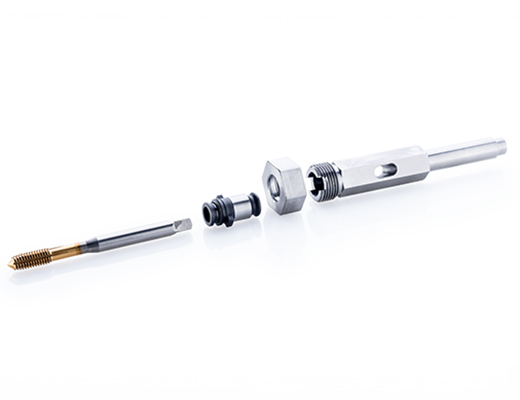
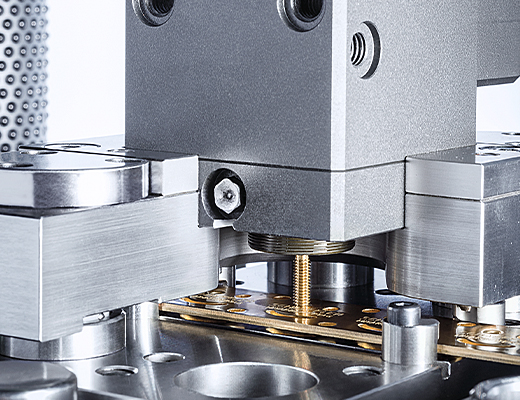
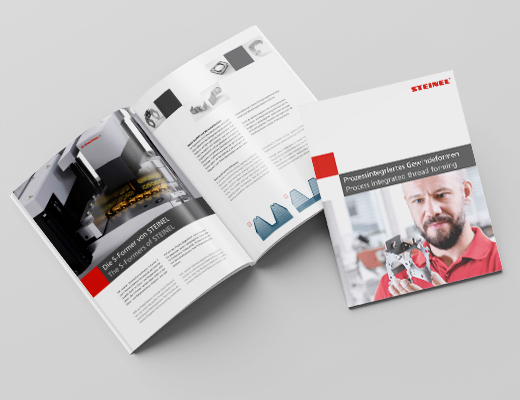
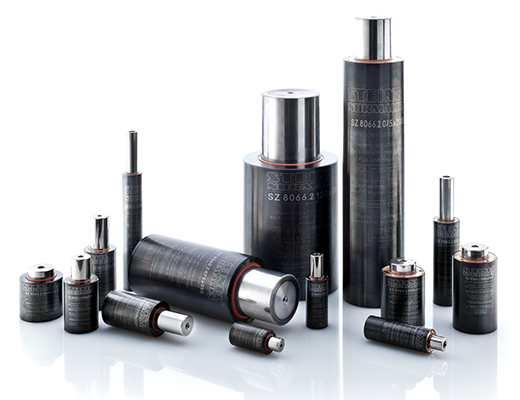
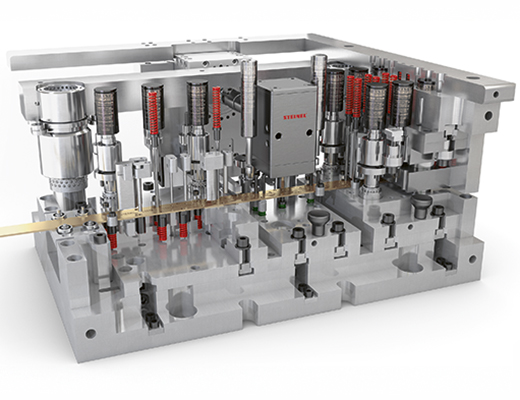
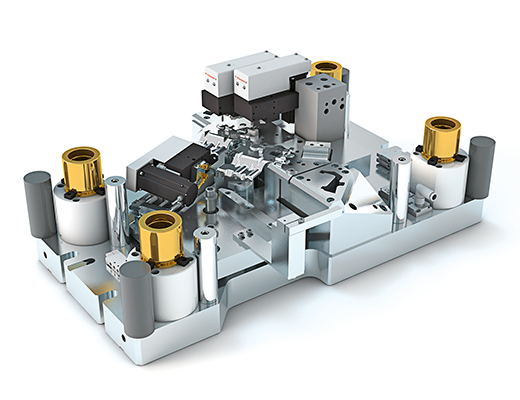
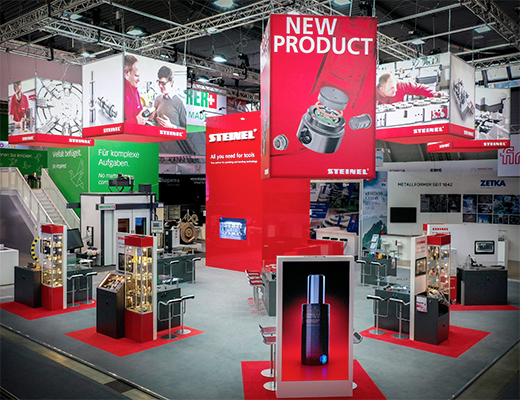
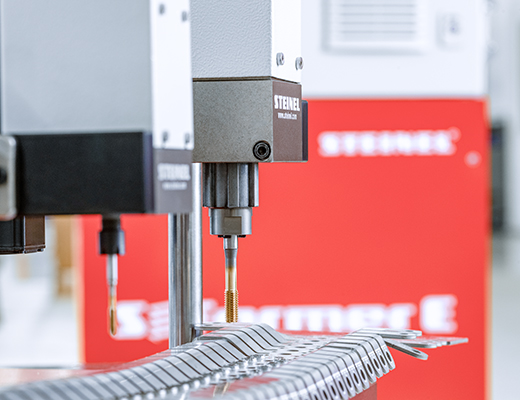
Nuevos desarrollos y patentes
Las unidades de formación de rosca denominadas S-Former son un buen ejemplo del potencial innovador de Steinel.
Estos sistemas desarrollados por los ingeniosos técnicos de Steinel impulsan notablemente la productividad de los clientes, dado que las roscas se fabrican directamente en el proceso de troquelado y doblado. A diferencia de las roscas cortadas, en las roscas formadas la estructura metálica se comprime, lo que se traduce en una mayor resistencia. Además, la formación de la rosca se lleva a cabo sin arranque de viruta, lo que evita el ensuciamiento del troquel. Esto significa que todas las fases de trabajo necesarias se llevan a cabo en un solo proceso, lo que se traduce en un pronunciado incremento de la productividad y en la obtención de roscas de la máxima calidad.