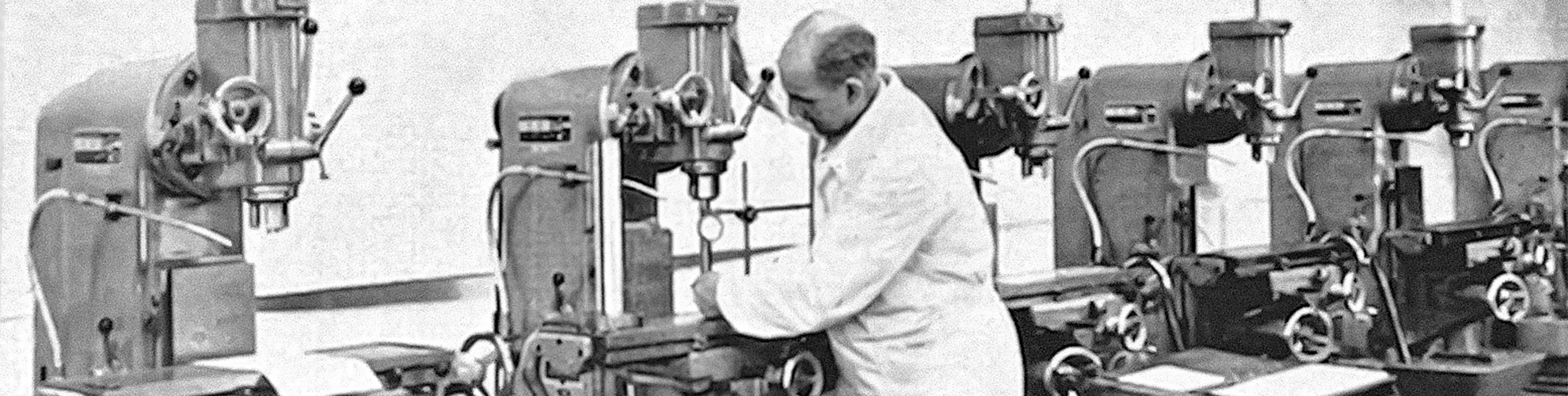
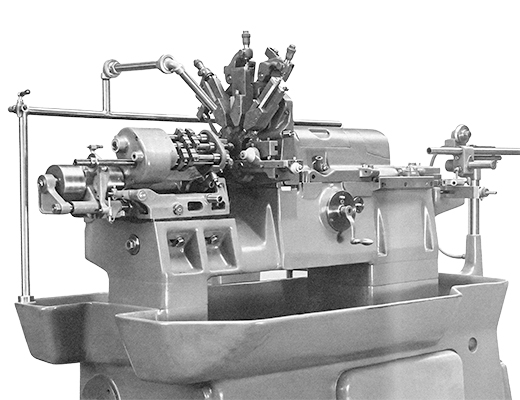
From ice skates to industrial machines
A machine that produces the rings used to tension the mainsprings for clocks transforms this workshop into a real factory. A big step for this young, small company since this new machine can be used to produce parts for the clock-making industry in which demand runs into the millions: Every single watch and clock spring needs one of these wire rings. Until now, these rings have been made by hand. This is not an easy manual job, so large quantities are simply not possible. Steinel’s machine changes that altogether. His production machine operates right around the clock.
Which is just as well because the clock industry in Schwenningen needs enormous quantities of components to satisfy its rapidly increasing production output. Clock-making, which started out in the mid-19th century as an artisan business, has grown into the town’s foremost industry, with a central significance for the economy of the region. Industrialisation brings technical innovations to the art of clock-making, also transforming Schwenningen into a centre for precision mechanics and precision engineering. In turn, this promotes the development of machines and tools in other industrial sectors. Bernhard Steinel himself worked in the clock-making industry for a few years before turning self-employed. The dominant businesses in this sector are the big clock factories owned by Friedrich Mauthe, Thomas Haller, Schlenker and Kienzle.
Read moreThe world’s first ever multi-spindle drilling machine
However, the business climate improves slowly, enabling Steinel once again to focus on building machines. In 1927, the young entrepreneur hires his first technical assistant. Harnessing his expertise, the pace of innovation continues to accelerate. Another sensational success is chalked up in 1927 when he develops and manufactures the world’s first ever multi-spindle drilling machine. As the years pass, an entire range of new machines is inspired by the creation of this product. Right from the get-go, progress is rapid and spectacular: This first multi-spindle drilling machine is followed by multiple-head drilling machines and thread-cutting or ‘tapping’ machines. This small team then goes on to produces hammer riveting machines, roller burnishing machines and curve milling units. Once again, Steinel is able to sell so many of these on the market that available space is no longer able to accommodate ever-increasing production volumes.
However, this next phase of expansion encounters a fresh economic crisis. This time it is The Great Depression of 1929/30 which later is seen to have been a global economic crisis. People no longer have any money to buy goods and demand drops like a stone. From one day to the next, just like everywhere else in Germany, thousands of men and women in Schwenningen become unemployed and are on the street. In order to survive, many companies in the clock-making industry are obliged to introduce short-time working. This is not the case for Bernhard Steinel. “I was always able to continue working”, as he recollects decades later. His personal conviction that an upturn always comes on the heels of every downturn proves to be an accurate one. This is borne out by the fact that Steinel remains well supplied with orders. He is even conducting business with Russia. His company supplies roller burnishing and drilling machines to that country. Demand there for these machines is good. So good in fact that his existing machines eventually lack the capacity to satisfy all his orders. The solution: A second shift is introduced - the machines now run for longer because more employees are hired to operate them. With the local unemployment rate so high, it is no problem at all to find good specialists. By the end of that crisis period, Steinel has a well-trained workforce of fifteen mechanics and three apprentices. This team is able to meet the rapid increase in demand from customers. By 1930, the production facility has once again become too small. Steinel acquires the next-door property, known locally as ‘the Frick factory’, where he starts producing riveting machines. Here, he produces and sells 800 to 900 machines each year.
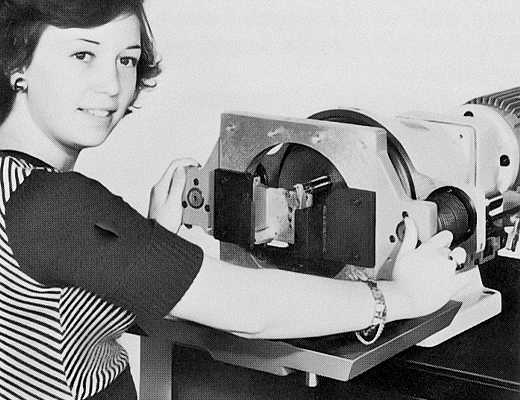

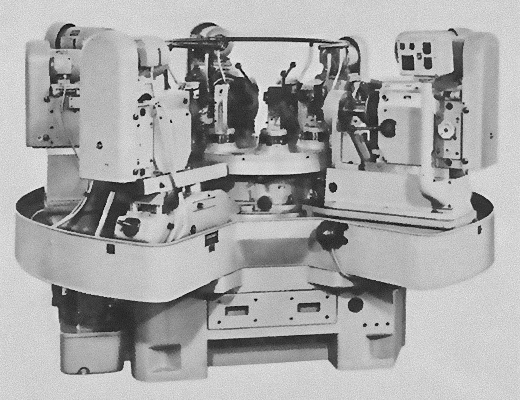
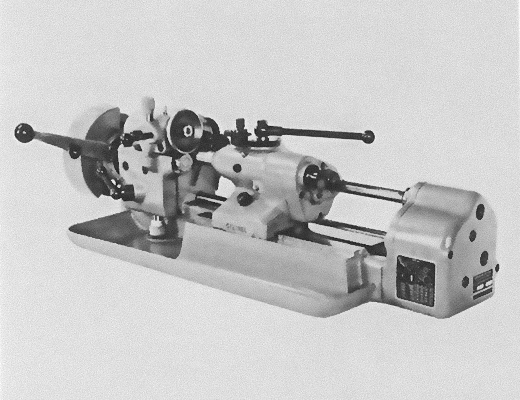
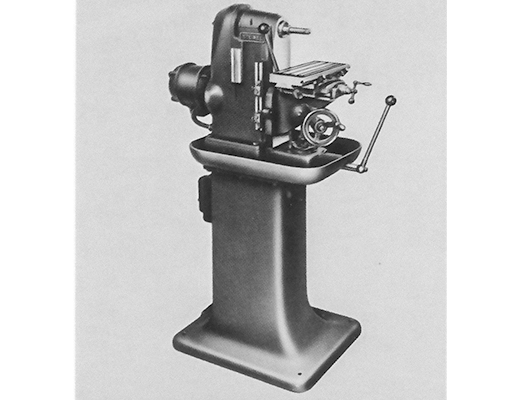
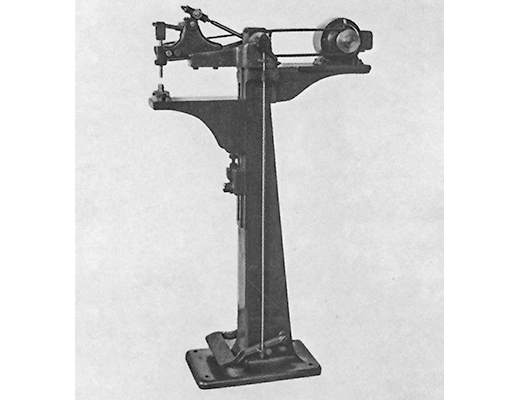
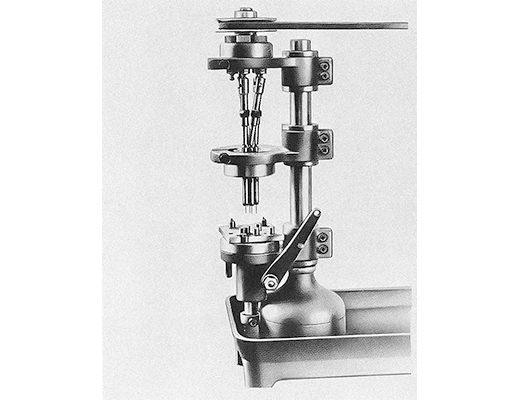

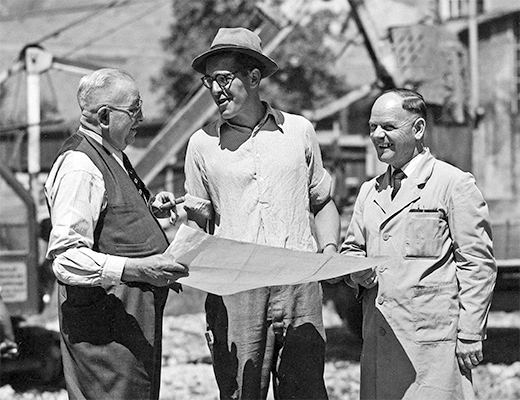
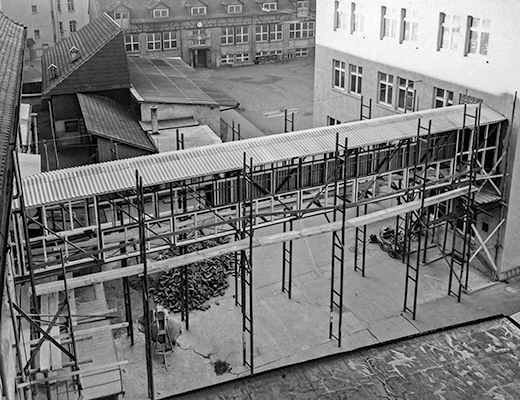
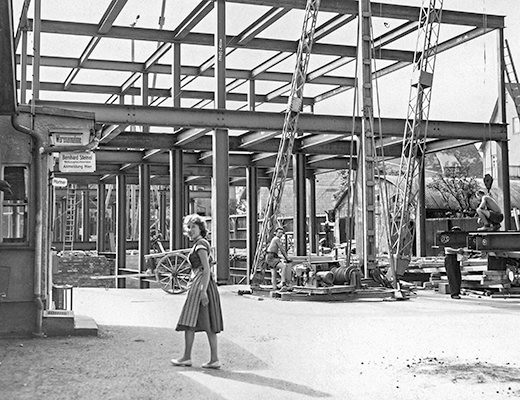
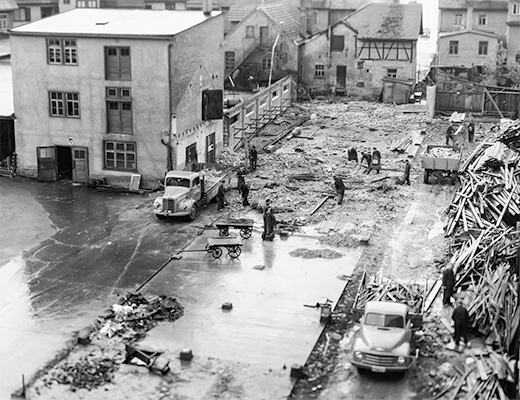
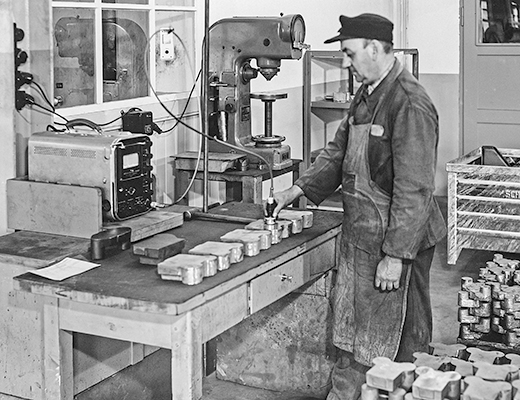
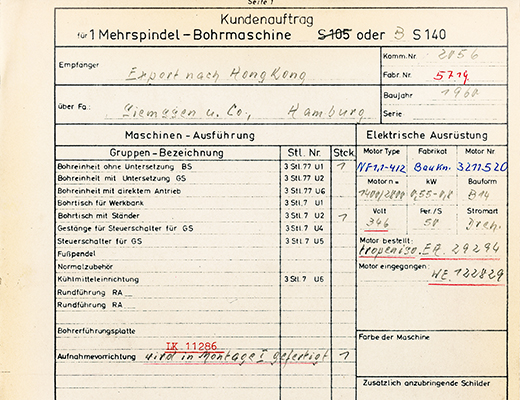
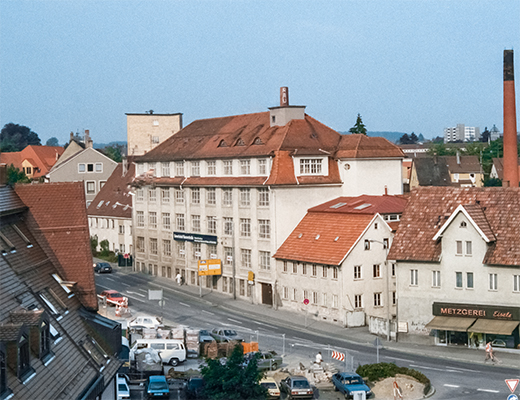
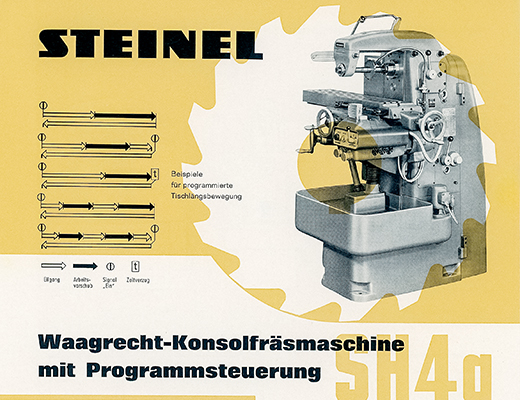
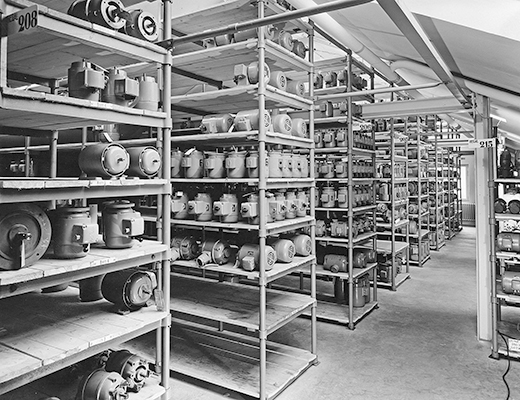
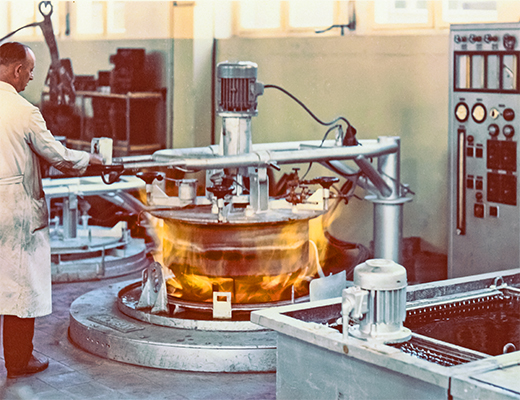
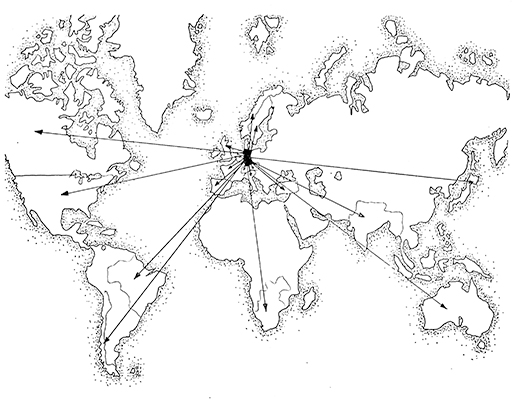
Always forging ahead with technical progress
Other than the setback inflicted by the confiscation of its production equipment, Steinel is able to continue its work seamlessly, reviving its pre-war product range: Initially in small quantities, turnkey milling machines, multi-spindle machines, small drilling machines, tenon rolling machines, drive polishing machines and riveting machines leave the factory gates. But that is by no means the whole story: The range of modular units developed during the war also goes back into production and undergoes further development. A short time later, the company is already able to supply eleven standards comprising a total of 130 products. By way of comparison: Decades later, Steinel fields seven product groups with 465 standards covering 25000 products. Steinel is able to provide everything from the smallest guide bush to large pillar frames.
Read moreThe first IBM computer
An article in the local newspaper in December 1970 reveals that company supervisors are issued with a printed weekly work schedule every Monday. That can happen because the computer now schedules three to four thousand production operations each week. This schedule determines the sequence in which the 260 different machine groups are to process the workpieces. Steinel is once again in a leadership position through the use of its IBM computer. This machine tool factory is the first company in the entire Schwarzwald-Baar-Heuberg region in which a computer calculates almost all manufacturing operations. “We cannot envision further progress for ourselves that does not involve the use of a data processing system of this kind”, states company boss Bernhard Steinel Jr. when the Steinel computer is unveiled at the IBM branch in Villingen. And here is what he means by that: Through optimum management of machine utilisation, this computer system makes production more economical. This also shortens delivery lead times and ensures that deadline commitments are honoured consistently. Steinel is prepared to pay a great deal for this enhanced level of efficiency: Every month, the company pays IBM no less than 30 000 Marks to lease this computer. That's a hefty price tag, given that the average hourly-paid operator only earns around 1000 Marks a month. However, this proves to be a price worth paying, being more than offset by savings from greater productivity. The computer has another major advantage: It never gets tired. Which also means it can be at its busiest when the workforce has already left for the weekend. From Friday evening, it runs flat-out, enabling it to schedule tasks for every machine during the coming week.
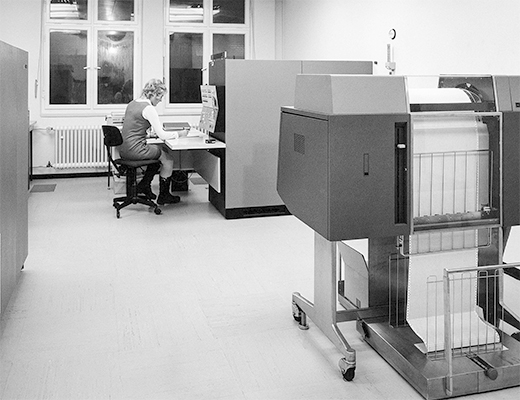
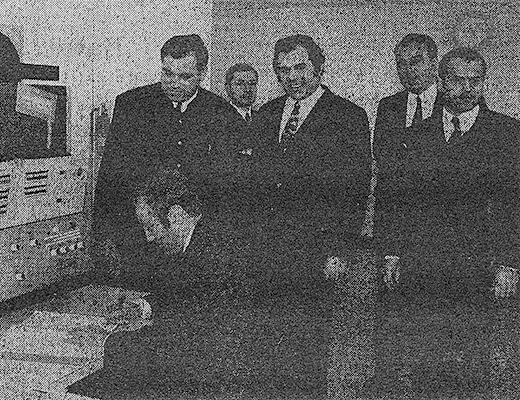
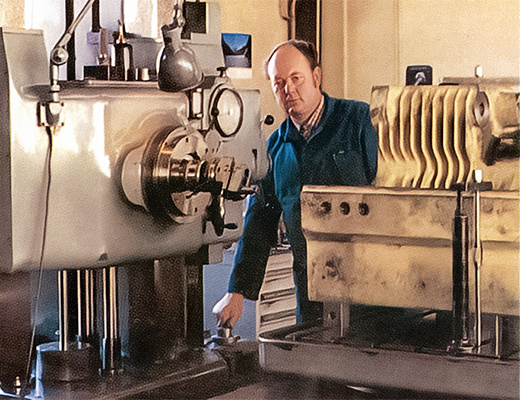
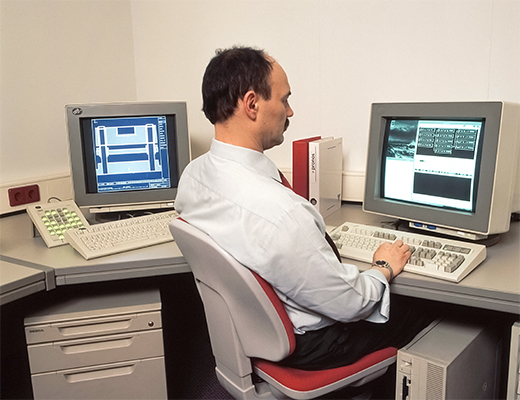
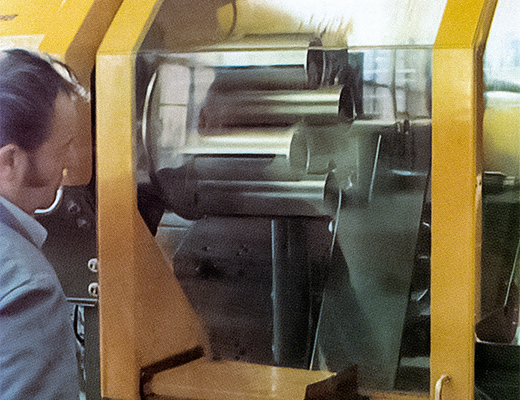
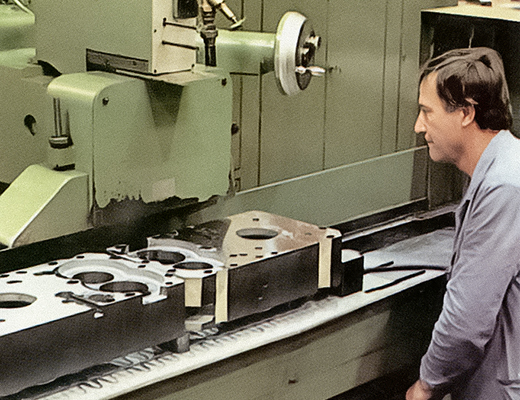

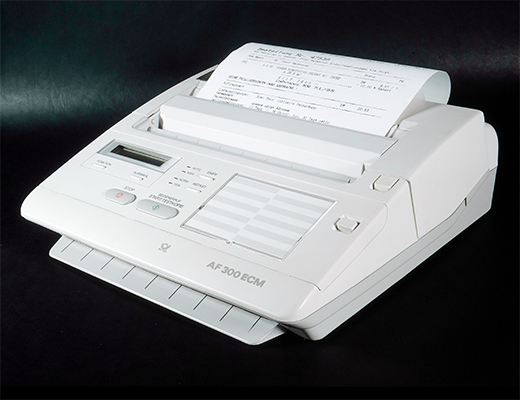
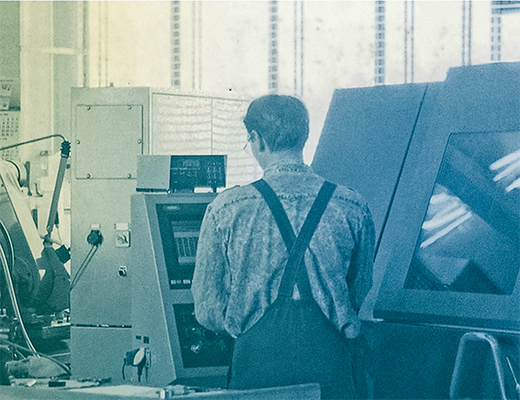
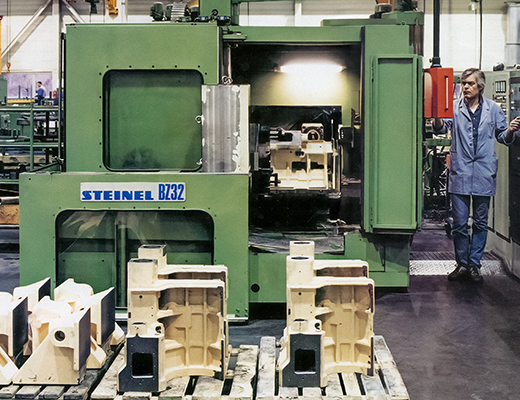
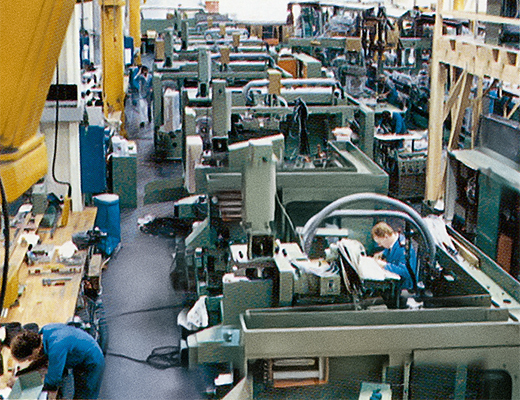
Even greater precision with CNC machines
CNC machines really are in the ascendancy now. Computer-numerically-controlled (CNC) machine tools enable material to be processed very precisely indeed. They make it possible to produce components to high standards of precision and repeatability. Their big advantage over manually operated machines is that they work autonomously, performing many tasks without human intervention as soon as one of their programs starts running. These machines owe their tremendous precision to their computerised control system which enables them to perform complex and detailed work, achieving zero-defect output even when repeated on a large scale.
However, the advent of the personal computer, the PC, still lies some years in the future. It is not until April 1990 that the company’s first PC gets installed in the Sales office. Individual departments are allocated set times when they can use this new computer. In-house communication uses a fax with thermal paper, printouts from which reach their recipients using the company's pneumatic tube system. An e-mail system is not introduced until 2001, a delay due in large part to security concerns.
The start of plant construction
On the strength of the depth and breadth of experience of its design engineers and workforce, Steinel now considers itself ideally equipped to enter the plant engineering sector. This constitutes a big step into the future. The company is now literally able to offer its customers complete turnkey production systems. Steinel covers the entire spectrum from raw materials to production and testing, right through to on-site installation of the new plant. To provide solutions to problems of this level of complexity, Steinel engineers draw on in-house products as well as on machines from other manufacturers. The company now possesses extensive expertise, especially in the planning of plant for the production of pipes, sleeves, drilling chisels as well as the drill bits used for oil and gas extraction. This is in demand right around the globe. Steinel now supplies and installs its technology in Austria, Japan, the USA and even in the Soviet Union. This includes CNC turning machines, deep-hole drilling machines, specialist machining centres, assembly machines as well as a multi-faceted range of testing and measuring systems.
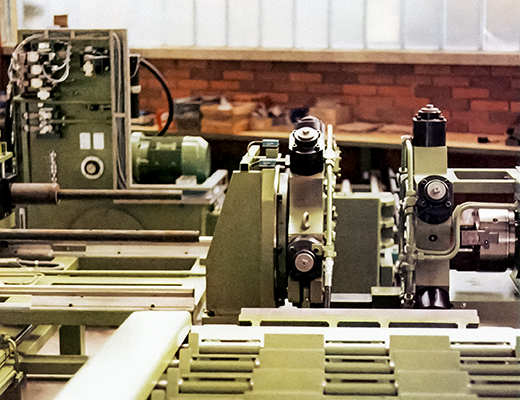

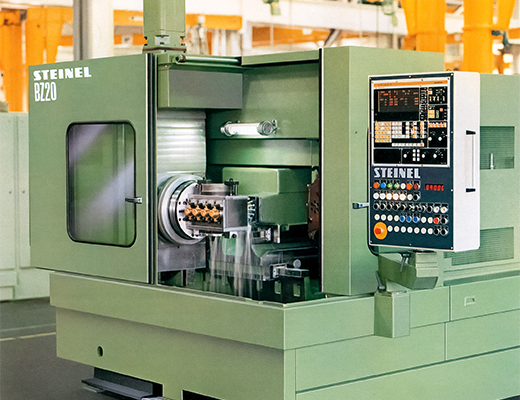
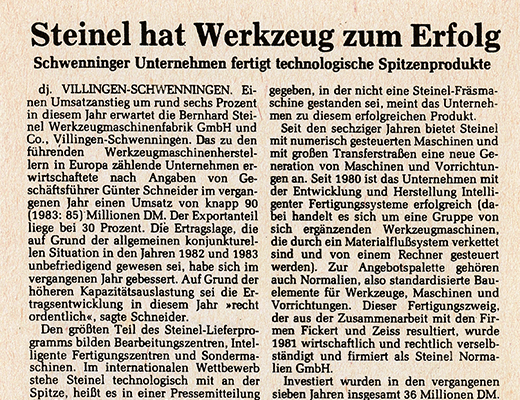
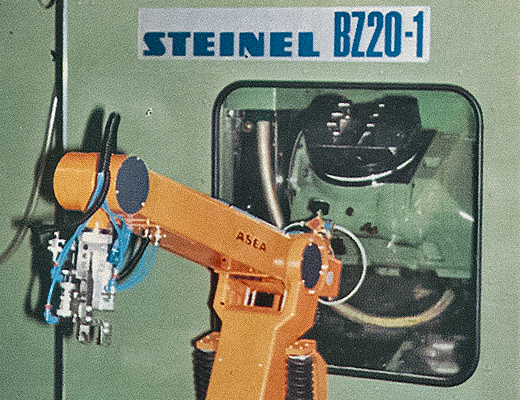
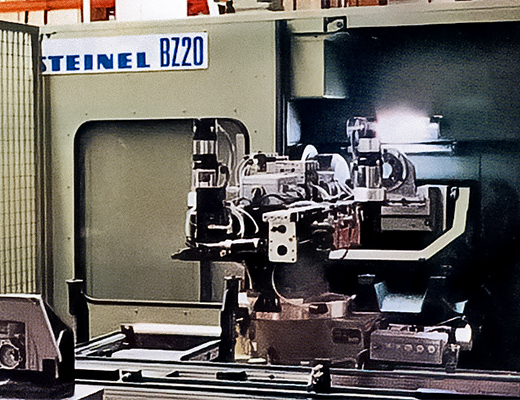
Computer controls machine
As a manufacturer of smart manufacturing systems, Steinel is also sought ought by Zeiss to partner it on a pioneering project. This involves the pilot plant for a flexible manufacturing system capable of machining 150 different workpieces. This is made possible by the computer-controlled system featuring four BZ 20 machining centres with pallet changing device, pallet storage with 30 slots, a loading and unloading area, an NC-controlled transport carriage and a measuring machine. This new product attracts a great deal of interest at a public demonstration of the commissioning process. In the course of that same year and again in 1984, Steinel supplies a flexible production system to Bosch. These systems now feature four BZ 20 and four BZ 25 machining centres with 80 twin-spindle heads. These are interconnected by a modular pallet transport system. Handling devices load and unload these systems. However, that is only the beginning. Many more flexible production systems of a similar design are supplied to leading companies. For all of these projects, Steinel is able to draw upon its extensive experience in the construction of special machines that employ NC technology. These two complementary areas are combined to satisfy demanding requirements. This makes it possible to manufacture even more productive machining centres. This is achieved using multi-spindle drilling heads with automatic workpiece feed, while the integrated NC units and automatic tool changers enhance the flexibility of these customised machines.
Read moreThe first website for a German provider of standard parts
In 1997, for many German companies, the Internet is still a mysterious new territory. Websites are still something of a rarity, and the notion that companies could showcase their products and services online is anything other than a widespread phenomenon Nonetheless, while others were still reluctant to take the plunge, Steinel becomes the first supplier of standard parts to venture into the digital age.
Although the .de domain was introduced back in 1986, it remains almost unused until the early Nineties. It is not until 1995 that commercial websites begin to establish themselves. Then, 1996 very well-known websites such as T-Online.de are launched. The following year sees the first offerings from banks and online shops. Then, starting in 1998, the number of websites also proliferates in Germany, due primarily to the increasing availability of DSL Internet connections.
With its self-confident motto of "50 years of expertise in quality - always one step ahead", Steinel projects a clear statement right from those very early stages that innovation and vision are core values of the company. The first website may have had a simple design, determined by what was technically feasible at that time, but its content is ground breaking. Steinel presents its product range in a clearly structured manner under the heading of “Our sales range for stamping and forming technology" Aluminium and steel column frames, guide elements, cutting elements, spring elements, accessories and machine elements.
One of the highlights on the website is headed “About us”. Here, Steinel not only imparts information, first and foremost it seeks to inspire confidence: An entire product range from a one-stop shop, featuring consistently excellent quality, a central warehouse with 25 000 products and a dependable delivery service - these are all messages that position Steinel as a capable partner.
At the time, having your own website is so unusual that the local newspaper Neckarquelle publishes a series of articles about the tiny handful of companies that already have an Internet presence. In Schwenningen, Steinel is a member of this exclusive group of digital pioneers.
At a time when there are only around 5000 to 10 000 German websites, a time when the Internet is populated for the most part by universities and large corporations such as BMW and Deutsche Telekom, Steinel is sending out a clear signal: The future is digital. With an electronic product information system on CD-ROM, CAD linking and the modern WorldCAT software for product research and order processing, Steinel is not simply being courageous, it is also demonstrating a profound understanding of the opportunities afforded by the digital world.
Today, almost three decades later, Steinel’s Internet presence constitutes a central building block of the company. Moreover, the pioneering spirit of 1997 lives on: As one of the first companies to recognise the potential of the Internet, Steinel remains loyal to its core beliefs - always one step ahead, always right up-to-date. An example of genuinely visionary corporate culture.
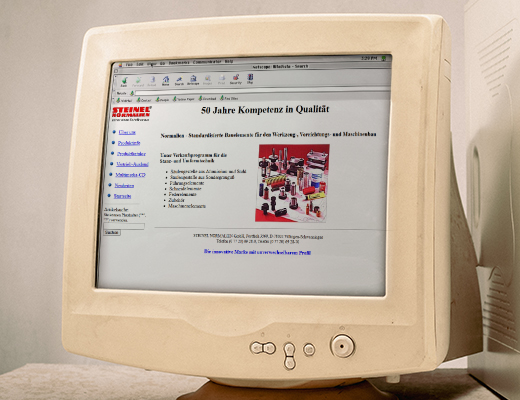
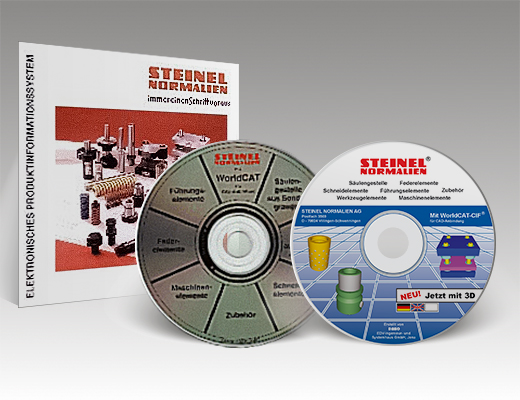
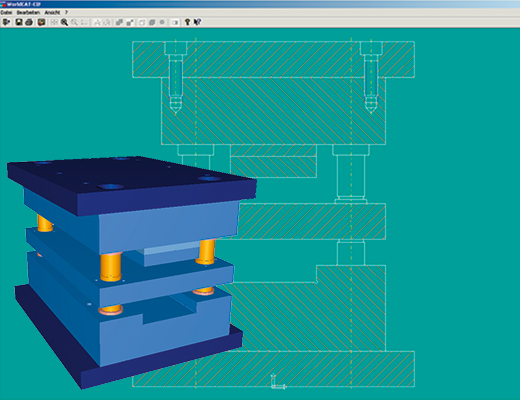
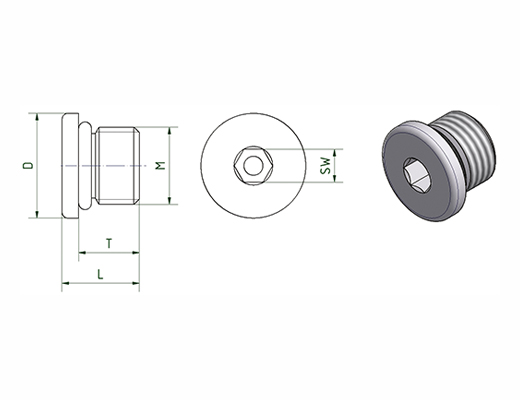
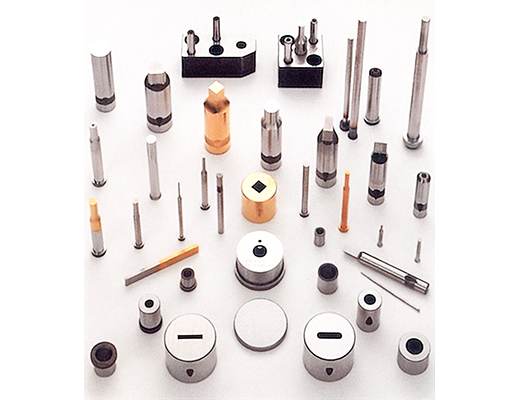
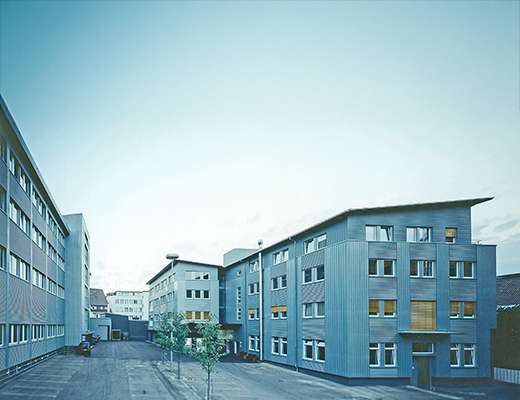
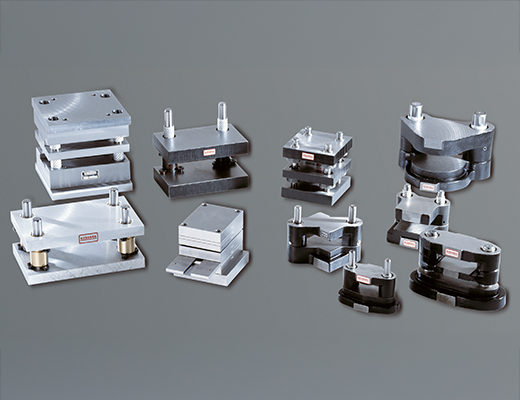
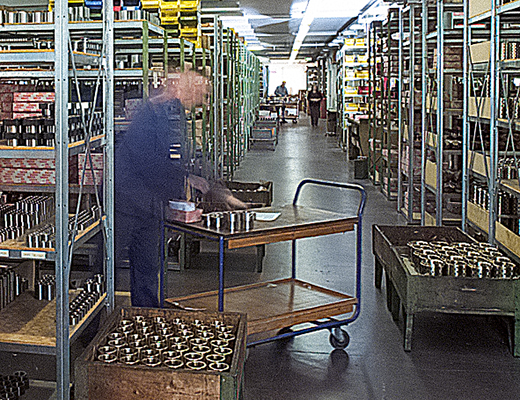
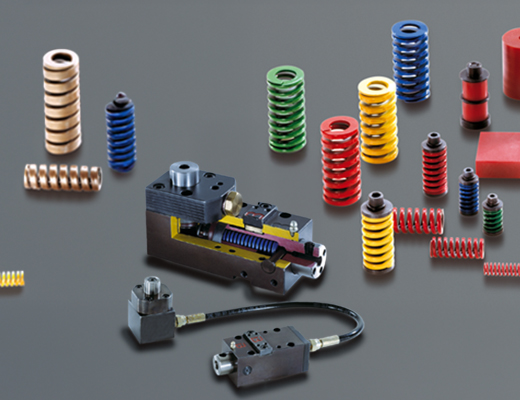
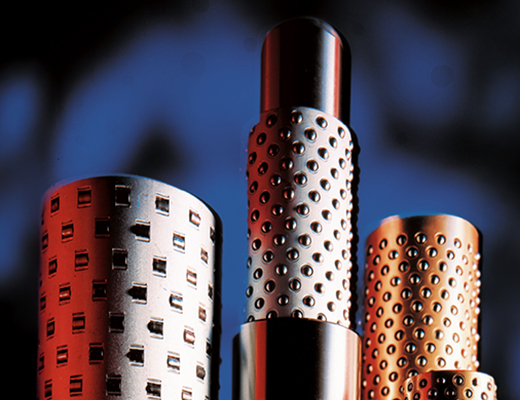
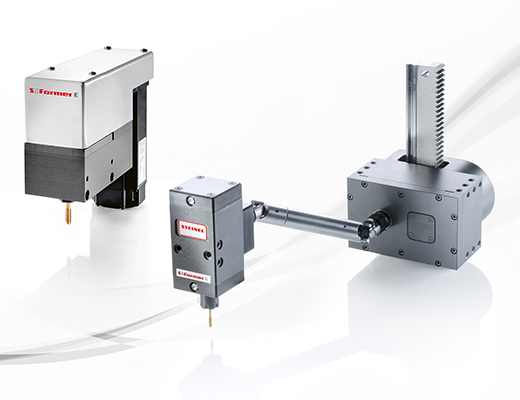
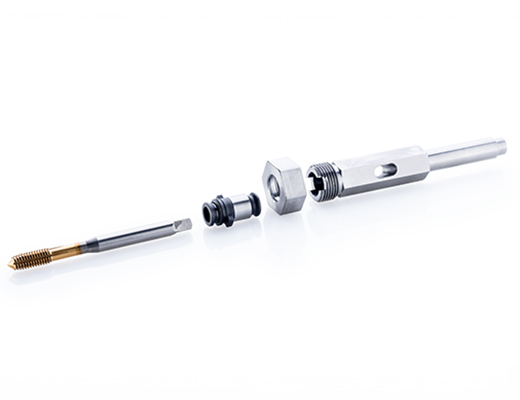
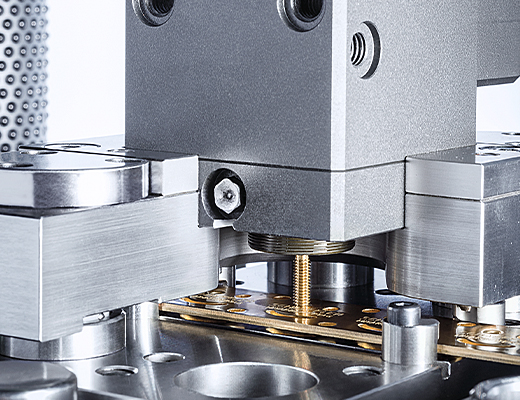
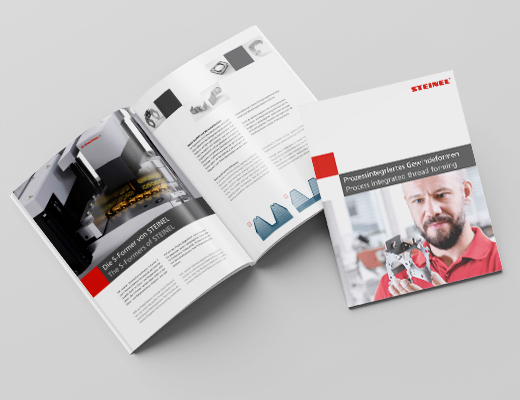
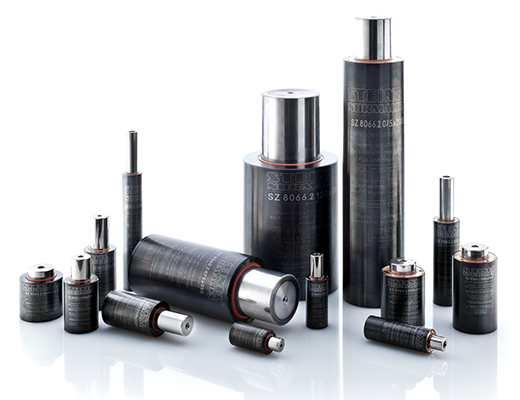
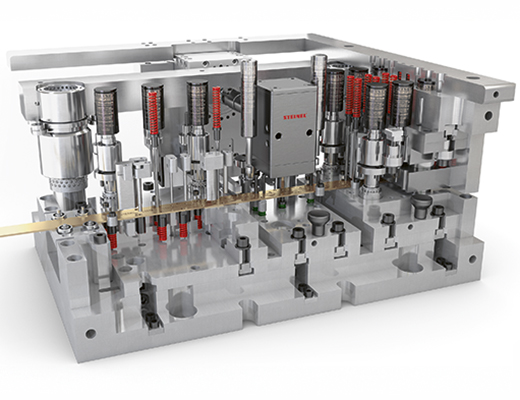
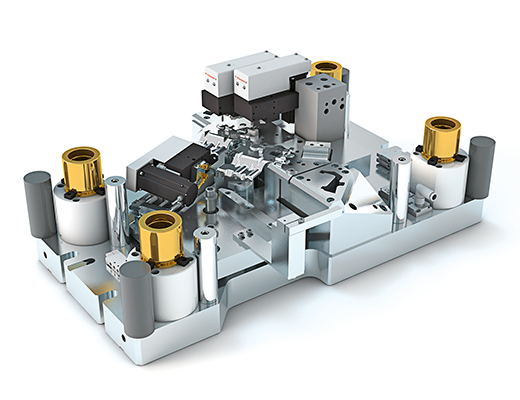
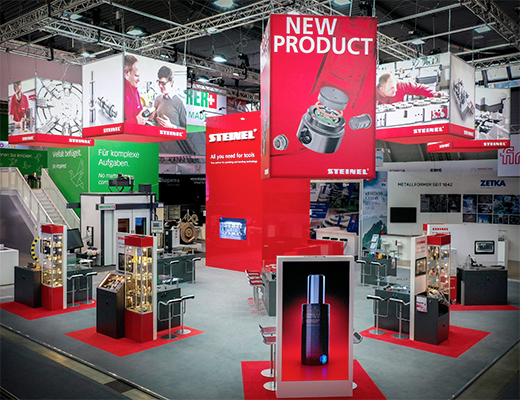
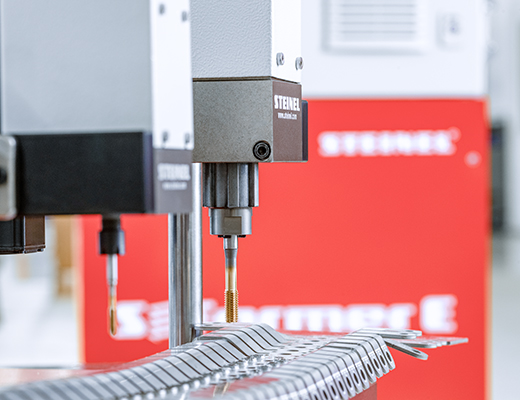
Innovations and patents
A fine example of Steinel’s potential for innovation is its S-Former range of tapping units.
The systems developed by Steinel’s creative minds translate into significant gains in productivity for its customers. This is because threads are produced directly in the punching and bending process. In contrast to cut threads, the metal structure of moulded threads is compacted. This delivers greater strength. Furthermore, the thread moulding process does not produce any chips which prevents moulds from getting contaminated. As a consequence, all necessary operations are completed in a single process. This results in a big increase in productivity combined with optimum thread quality.
Read more