![[Translate to Englisch:] [Translate to Englisch:]](/fileadmin/user_upload/Firmengeschehen.jpg)
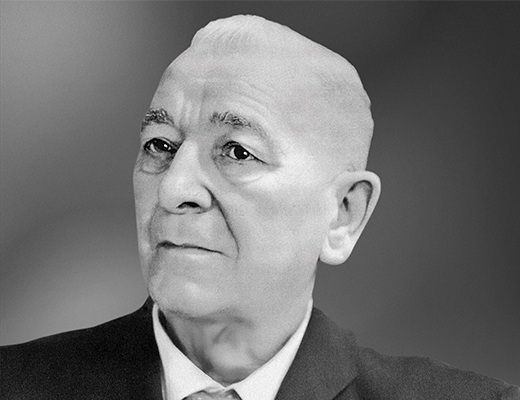
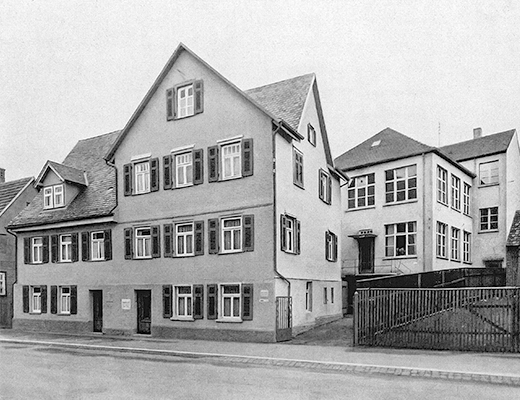
A living room start-up
The Steinel story begins back in 1924 in a living room in the German town of Schwenningen. After work, Bernhard Steinel, a foreman at the Thomas Ernst Haller clock factory, repairs bicycles and small machines at home. His nephew Alfred Jauch works as his assistant. Very modest beginnings indeed. During holiday periods, a wooden shed in a neighbour's garden serves as a home for this workshop. To begin with, orders take the form of repair work. These two mechanics restore lathes and motors to working order. In winter, they even sharpen ice skate blades. With good reason too, because ice hockey is starting to become really popular in Schwenningen. A swimming and ice-skating club is founded after the tragic drowning of four young people in the Salinensee in nearby Dürrheim. The new club aims to ensure that swimming and ice skating become safer, establishing a great tradition in the process. In the modern day, the SERC’s Wild Wings professional team in the German Ice Hockey League (DEL) is the highest-ranking sports team in the region.
Read moreFrom ice skates to industrial machines
A machine that produces the rings used to tension the mainsprings for clocks transforms this workshop into a real factory. A big step for this young, small company since this new machine can be used to produce parts for the clock-making industry in which demand runs into the millions: Every single watch and clock spring needs one of these wire rings. Until now, these rings have been made by hand. This is not an easy manual job, so large quantities are simply not possible. Steinel’s machine changes that altogether. His production machine operates right around the clock.
Which is just as well because the clock industry in Schwenningen needs enormous quantities of components to satisfy its rapidly increasing production output. Clock-making, which started out in the mid-19th century as an artisan business, has grown into the town’s foremost industry, with a central significance for the economy of the region. Industrialisation brings technical innovations to the art of clock-making, also transforming Schwenningen into a centre for precision mechanics and precision engineering. In turn, this promotes the development of machines and tools in other industrial sectors. Bernhard Steinel himself worked in the clock-making industry for a few years before turning self-employed. The dominant businesses in this sector are the big clock factories owned by Friedrich Mauthe, Thomas Haller, Schlenker and Kienzle.
Around the turn of the century, these plants in Schwenningen already have well above 1500 employees. A similar number of self-employed people work from home. Industrially speaking, both sides benefit from this additional home-based capacity: The self-employed workers can spare themselves the long and arduous commute to town from their farms and outlying homes while the company owners have access to a labour force whose capacity they can simply stop using when demand is weak, then draw upon again as soon as business picks up. There are also other advantages, especially in relation to costs: These self-employed ‘domestic industrialists’ work with their own machines and earn less than their full-time factory worker counterparts. By way of example, someone working from home for twelve to fourteen hours a day is able earn around 15 to 18 German Marks a week.
In a sense, as a young entrepreneur, Steinel is also one of these ‘domestic industrialists’. After all, his business does well when the clock industry is doing well. His machine enables him to meet the big demand from the clock manufacturers, assuring him of a regular income. Indeed, this tireless machine of his makes him a modest living as a self-employed individual.
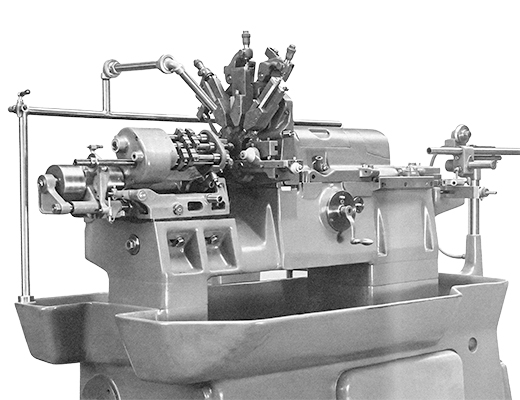
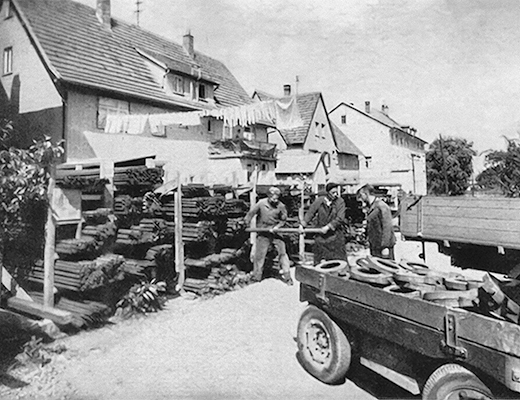
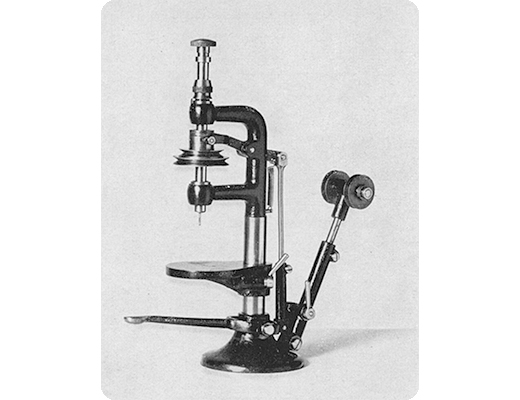
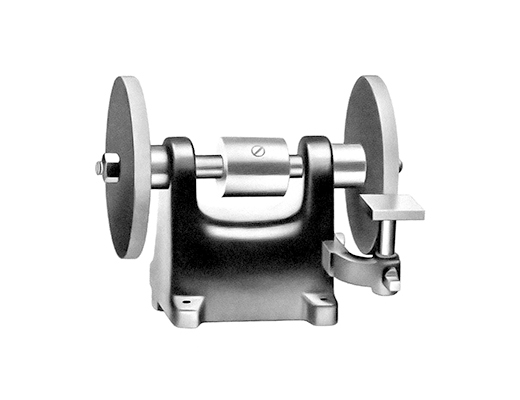
The first expansion
Nonetheless, Bernhard Steinel has no wish to rest on his laurels: As a second string to his bow, he starts to build machines. Small, simple sanding blocks are a product that can be manufactured in large quantities and delivered to customers very rapidly from his workshop on Sturmbühlstrasse. The entrepreneur charges 16 German Marks for each unit. That clearly represents good value for money to his customers because demand is high, and his small premises soon become too small to accommodate the steady increase in production volumes. Just one year after founding his company, Steinel has to expand, building a workshop in his garden at the back of his house. The floor area of the first factory built by this entrepreneur measures eight square metres. However, scarcely is construction of this new building complete than the economic climate changes abruptly. The young entrepreneur has to navigate his first crisis and manages to keep his head above water by returning to what his business was originally set up to do: Repair work
The world’s first ever multi-spindle drilling machine
However, the business climate improves slowly, enabling Steinel once again to focus on building machines. In 1927, the young entrepreneur hires his first technical assistant. Harnessing his expertise, the pace of innovation continues to accelerate. Another sensational success is chalked up in 1927 when he develops and manufactures the world’s first ever multi-spindle drilling machine. As the years pass, an entire range of new machines is inspired by the creation of this product. Right from the get-go, progress is rapid and spectacular: This first multi-spindle drilling machine is followed by multiple-head drilling machines and thread-cutting or ‘tapping’ machines. This small team then goes on to produces hammer riveting machines, roller burnishing machines and curve milling units. Once again, Steinel is able to sell so many of these on the market that available space is no longer able to accommodate ever-increasing production volumes.
However, this next phase of expansion encounters a fresh economic crisis. This time it is The Great Depression of 1929/30 which later is seen to have been a global economic crisis. People no longer have any money to buy goods and demand drops like a stone. From one day to the next, just like everywhere else in Germany, thousands of men and women in Schwenningen become unemployed and are on the street. In order to survive, many companies in the clock-making industry are obliged to introduce short-time working. This is not the case for Bernhard Steinel. “I was always able to continue working”, as he recollects decades later. His personal conviction that an upturn always comes on the heels of every downturn proves to be an accurate one. This is borne out by the fact that Steinel remains well supplied with orders. He is even conducting business with Russia. His company supplies roller burnishing and drilling machines to that country. Demand there for these machines is good. So good in fact that his existing machines eventually lack the capacity to satisfy all his orders. The solution: A second shift is introduced - the machines now run for longer because more employees are hired to operate them. With the local unemployment rate so high, it is no problem at all to find good specialists. By the end of that crisis period, Steinel has a well-trained workforce of fifteen mechanics and three apprentices. This team is able to meet the rapid increase in demand from customers. By 1930, the production facility has once again become too small. Steinel acquires the next-door property, known locally as ‘the Frick factory’, where he starts producing riveting machines. Here, he produces and sells 800 to 900 machines each year.
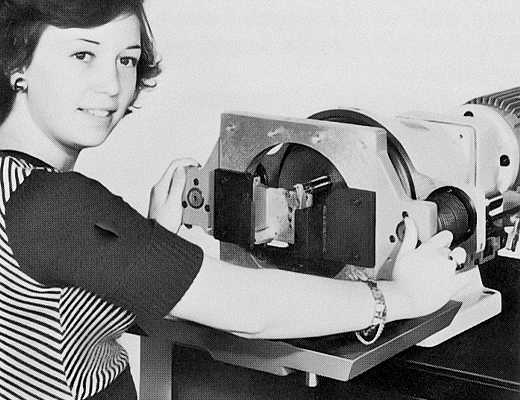

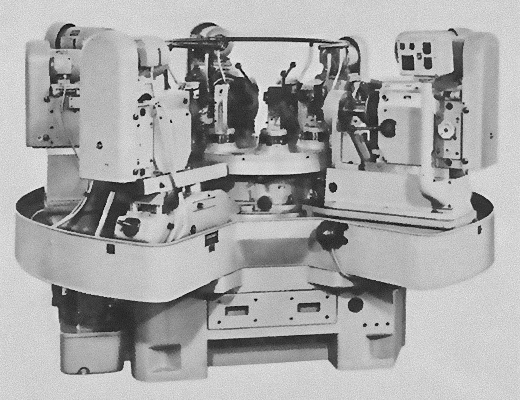
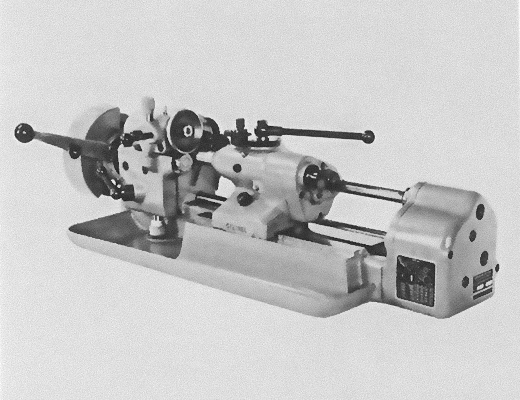
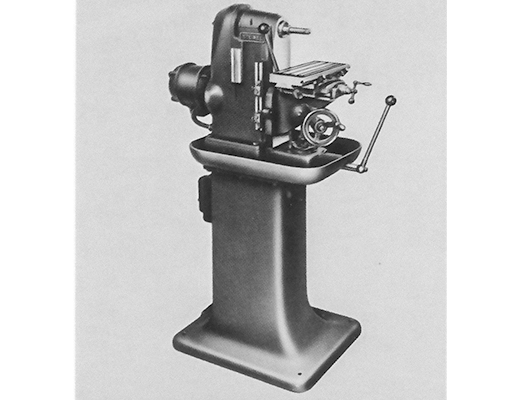
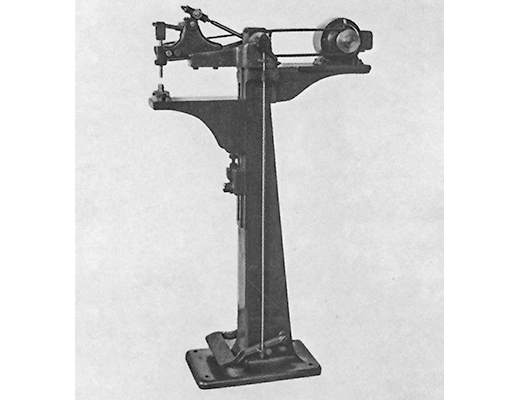
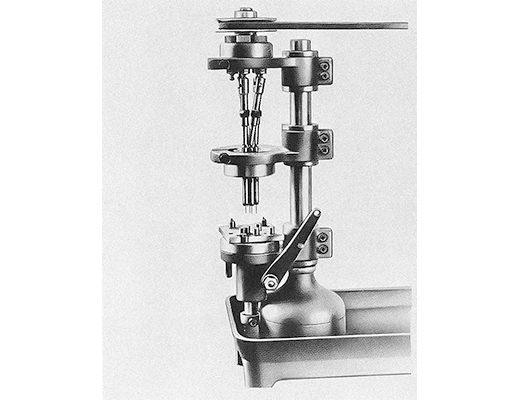

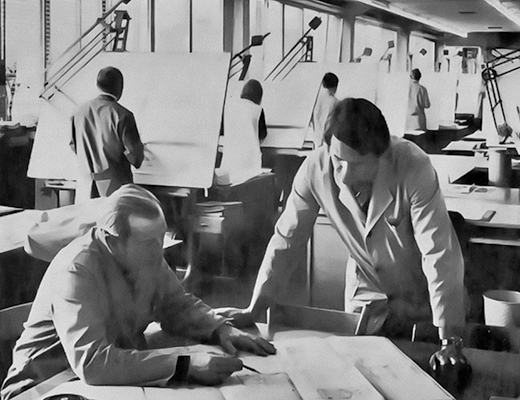
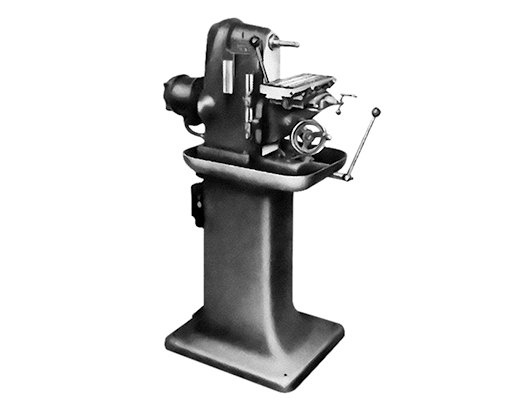
A strong sales partner
Steinel continues to expand its production range and transitions from one-off production to volume production. With business expanded to this extent, a partner is needed to take care of sales. Hahn & Kolb, a company based in Stuttgart, proves to be the ideal partner for selling Steinel products. This arrangement works very well indeed. The sales people in Stuttgart are supplied with superlative technology that they can then sell to their customers. An independent design department is set up. To an increasing extent, internal procedures are getting adapted to meet the requirements of an industrial company. Until now, company boss Bernhard Steinel, assisted by his daughters, has been responsible for the commercial side of the business over and above his design and workshop duties. The company also recruits an operations manager, and two employees with proven track records are promoted to supervisory posts Technical development continues apace during these personnel changes. From 1934, Steinel develops three different types of milling machine and puts them into volume production. The quality of Steinel milling machines establishes them as a household name all over the world.
Full order books, high levels of investment
From this point onwards, fortunes improve even more rapidly. The economy powers ahead inexorably and the Steinel workforce just keeps on growing. In 1937, the company already has 200 on its payroll. Despite one extension after another, the business premises are starting to burst at the seams again. Steinel acquires the building of the former Isaria meter factory on Winkelstrasse. This constitutes the decisive step towards becoming a medium-sized machine factory. Initial concern that the company might perhaps have overreached itself with these big premises proves to be unfounded. With an economic upturn in full swing and full order books, the high levels of investment in the extensive factory premises acquired from Isaria, a prime site location, prove to be absolutely the right thing to have done.
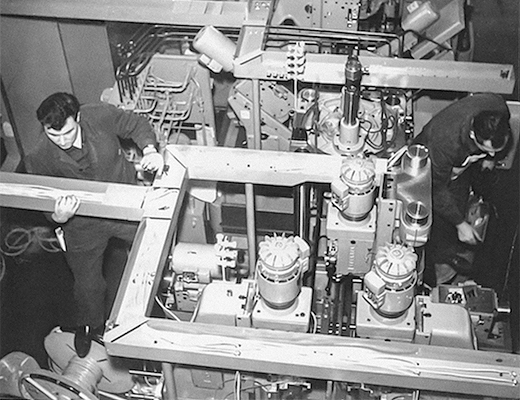
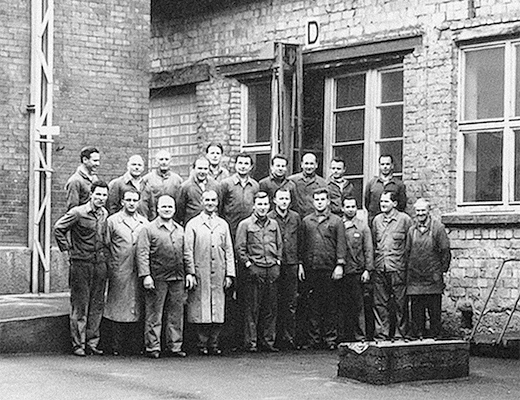
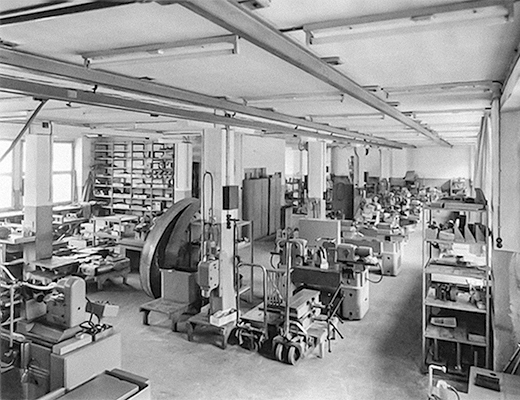
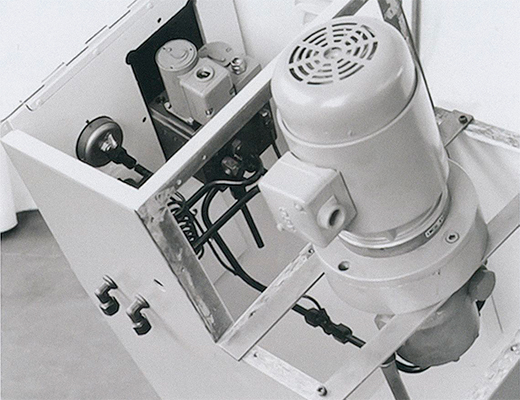
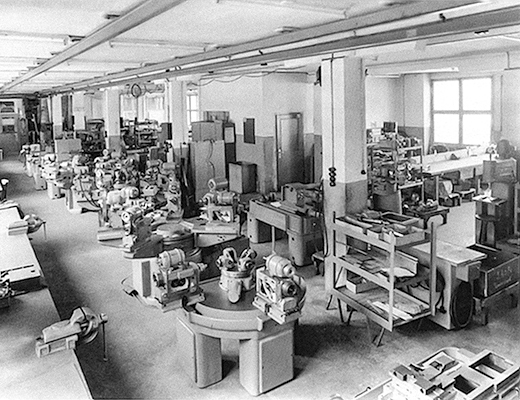
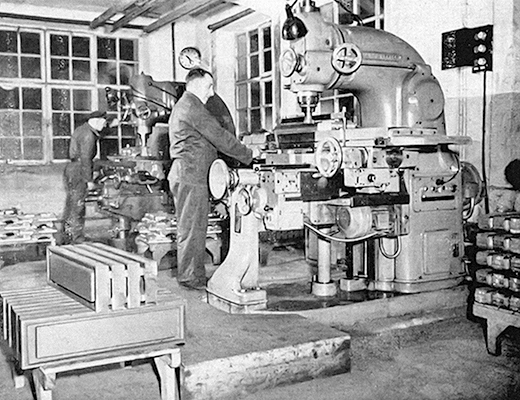
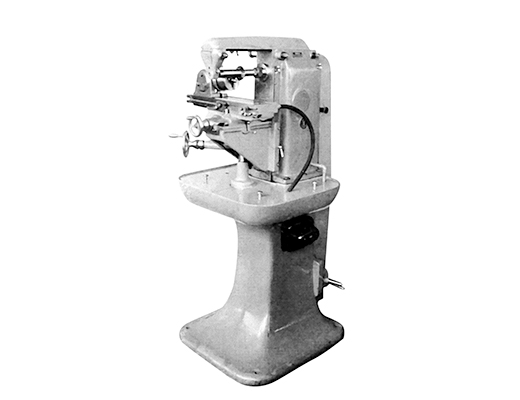
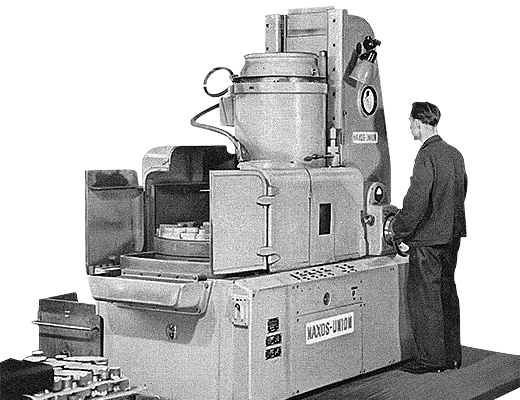
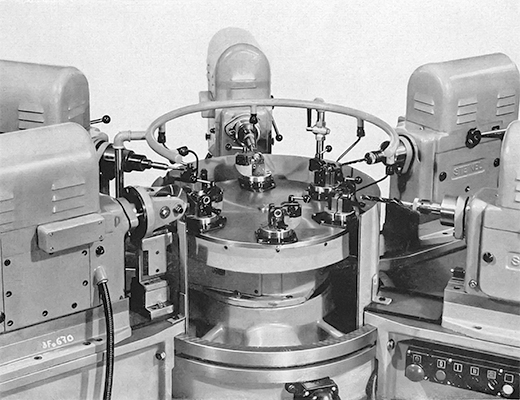
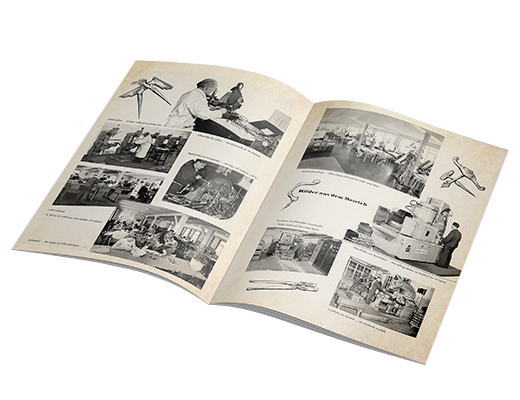
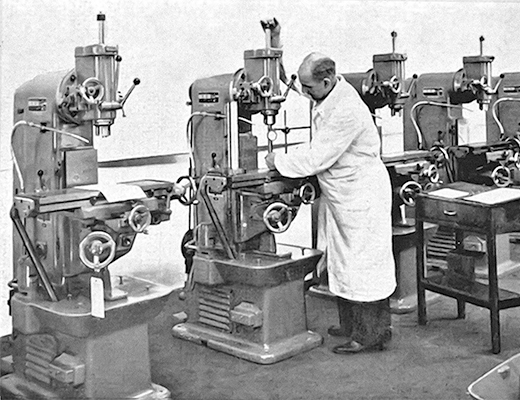
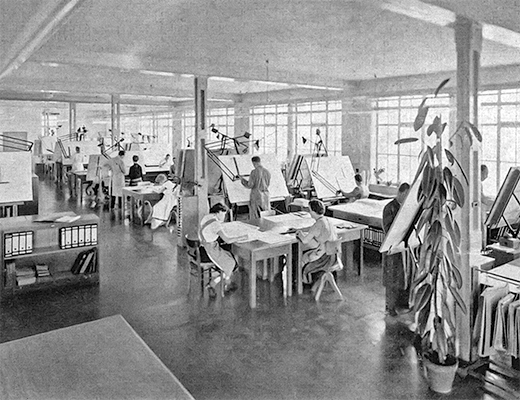
Already 300 employees at the outbreak of war
And the workforce stays at that level throughout the next few years. In 1937, the production range extends into an important sector with the first sliding headstock automatic lathe, a product requiring a lot of space in the production buildings. As early as 1939, Steinel is developing and building special-purpose machines with its 300 payroll staff The workforce comprises 243 hourly-paid men on the shop floor with 21 men and 13 women in salaried posts. Plus 31 young men and one young woman employed as apprentices. During this period, government officials require the company also to produce modular units for special machines, in addition to the existing product range. This later emerges as a very promising step to have taken for the future. In the ensuing decades, this branch of production becomes one of the main pillars of the business. The company only knows one direction: Onwards and upwards! The Second World War brings in large orders. The production range includes milling machines, multi-spindle machines, the P2 small boring machine, tenon rolling machines, drive polishing machines, rivet polishing machines and sliding headstock automatic lathes. Steinel is obliged to supply what is needed during these troubling times. Like all other companies in Germany, Steinel becomes an integral part of the wartime economy, producing precision parts and other components for the war machine.
Getting knocked down and getting back up again
Demand is far greater than production capability at this time. At the end of the war, the company employs a workforce of 450 but now faces the start of some difficult times. The French forces of occupation dismantle about 300 machines and much of the equipment in the factory. Between 65 and 80 per cent of production capacity gets dismantled and spirited away. The victors confiscate high-quality tools and test equipment. The financial loss amounts to 1.4 million Reichsmarks. Finally, after all this dismantling ends, the company is only left with enough machines for Steinel to keep 30 to 40 employees occupied with repair work. As Steinel puts it at the time, the only way to prevent even greater damage to his company is with “a great deal of oily and greasy work”.
The company may be on its knees, but Bernhard Steinel nonetheless sees a way forward. True to his motto, that what goes down will also go back up again, he sets about rebuilding his company. He is still able to draw upon the expertise and technical skills of his remaining employees. During these difficult post-war years, the entrepreneur calls upon his contacts, he purchases second-hand machines from companies that had not been dismantled quite as comprehensively, and he has the foresight to recognise that demand for his products is inevitably going to increase. After all, without toolmakers, any renaissance of industry in Germany is simply inconceivable. Steinel draws the right conclusions from this realisation and focuses on the production of standard parts, i.e. standardised parts for toolmaking. Volume production of column guide frames commences as early as 1948, followed in short order by other products. This is also recorded in company annals as the year when Steinel’s standard parts come into being.
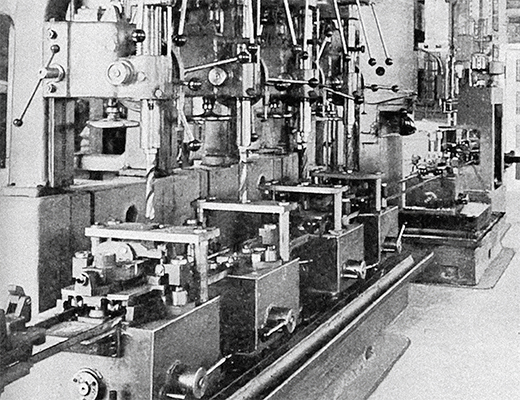
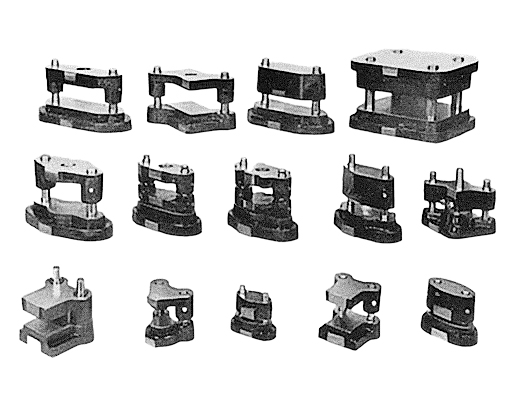
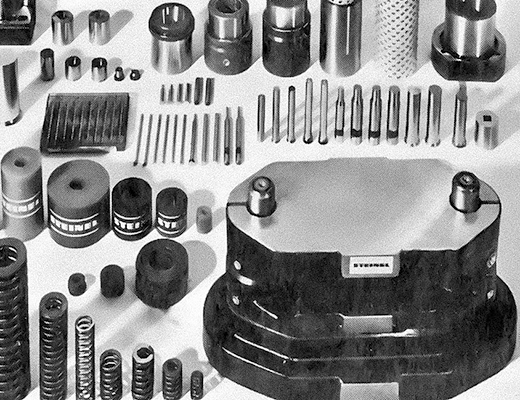
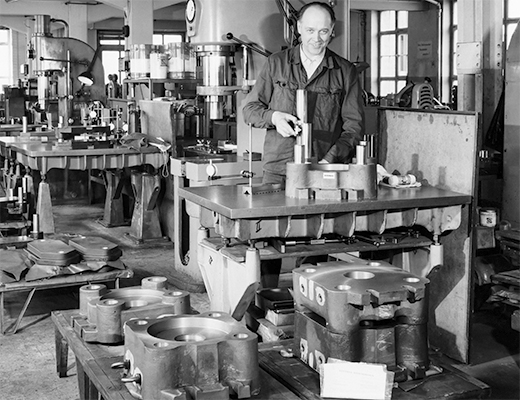
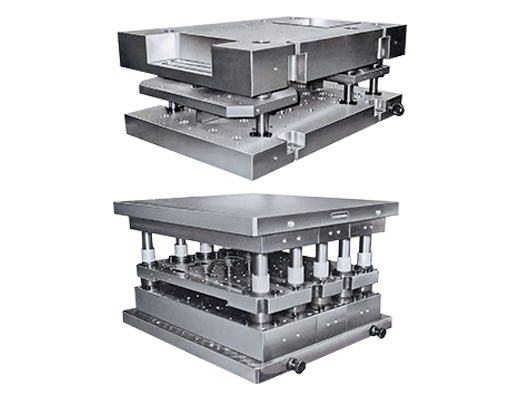
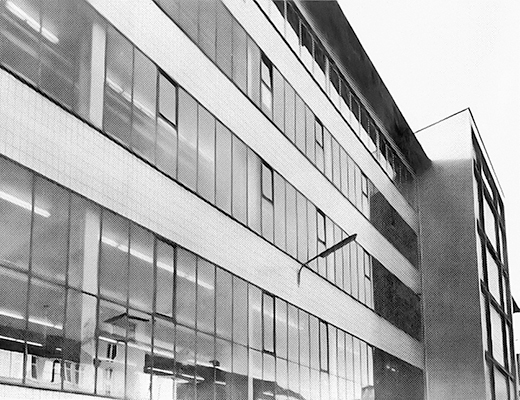
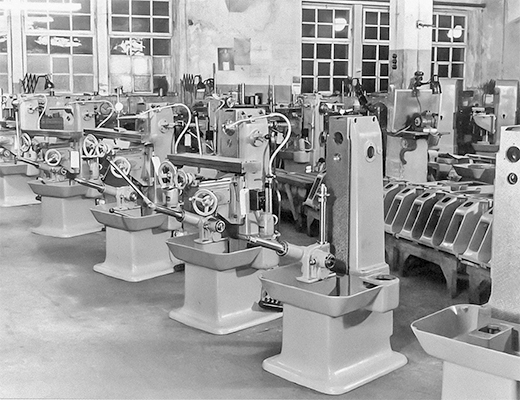
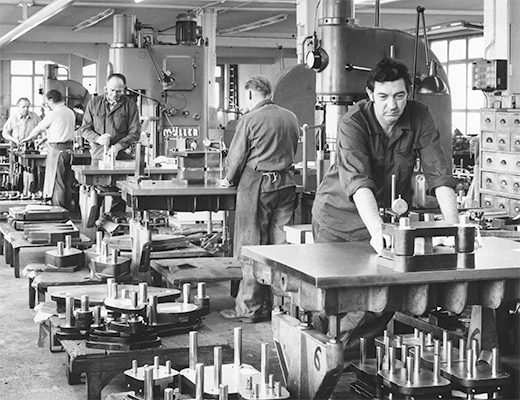

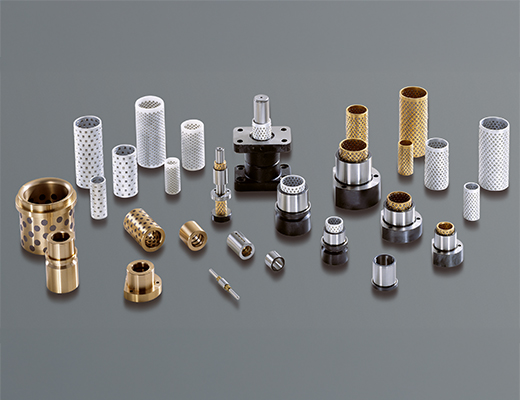
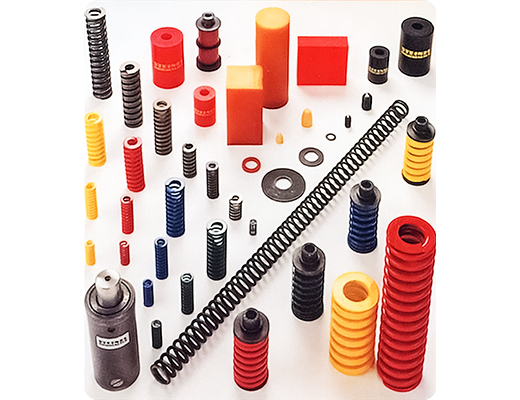
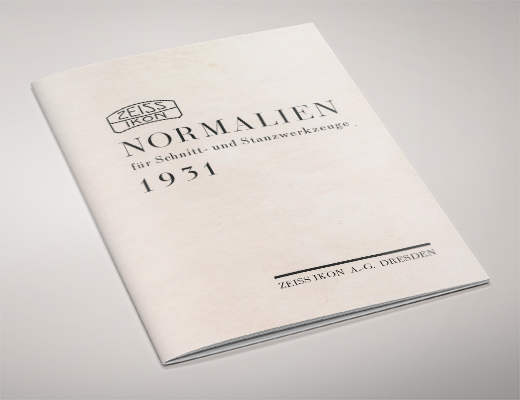
The first standard parts from Steinel
After the war, Bernhard Steinel focuses on standard parts for toolmaking. Zeiss-Ikon AG in Dresden had already laid the groundwork for this back in the 1930s. It was the first company ever to launch standardised punching tools and standardised tool elements on the market. This company is lost to its owners when the new rulers in Dresden nationalise the Zeiss factory. Faced with this situation, the part of Zeiss-Ikon that had moved to Stuttgart in the West takes the decision to continue fostering a close working partnership with its former sales partner Sustan. This is owned by the Frankfurt businessman Hanns Fickert, who now not only sells machine components and tools from several manufacturers, but also begins to produce standard parts on his own account. In collaboration with Steinel, he produces standardised punching tools. Right from Day One, everything points towards growth. After a short time, standard parts for moulding tools are added to the production schedule, which is soon expanded to include tools and standard parts for machining. From 1950 onwards, this division of labour really runs well: Steinel produces and the folk in Frankfurt generate the sales. However, in 1974, Sustan reaches the end of the road as a viable business. The company has to file for bankruptcy. At this point, Steinel takes charge of the sales of its own products, continuing to develop and extend the product range and increasingly to fine-tune it.
Always forging ahead with technical progress
Other than the setback inflicted by the confiscation of its production equipment, Steinel is able to continue its work seamlessly, reviving its pre-war product range: Initially in small quantities, turnkey milling machines, multi-spindle machines, small drilling machines, tenon rolling machines, drive polishing machines and riveting machines leave the factory gates. But that is by no means the whole story: The range of modular units developed during the war also goes back into production and undergoes further development. A short time later, the company is already able to supply eleven standards comprising a total of 130 products. By way of comparison: Decades later, Steinel fields seven product groups with 465 standards covering 25000 products. Steinel is able to provide everything from the smallest guide bush to large pillar frames.
By 1952, the worst is over and rapid progress is made on further development work. The range of products for its customers continues to grow because the company founder is never short of new ideas. He views every new task as a challenge and he channels his drive into technical progress. Constant improvements can be achieved in production through the introduction of new machines. An approach which enables this entrepreneur to become a successful technology leader. Steinel’s culture of continuous technical improvement becomes his hallmark quality. Success flows from the fact that the people who run this company have the skill of anticipating market developments. This equips them to meet customer demand more rapidly and more accurately.
The production facilities also undergo a huge expansion in the first half of the Fifties. The company is able to acquire additional buildings directly beside the existing factory. Within just a few years, a respectable size of industrial complex emerges. This is accompanied by a corresponding increase in the number of people on the company payroll. By 1955, the company already has 600 employees, achieving remarkable levels of production output with their work: In 1956, the 4000th Type SH4 milling machine is delivered to a customer. 1961 sees the completion of structural expansion for a while, with the construction of a four-storey building for assembly and design operations.
Less than 40 years after it was founded, Steinel has grown into a company of global stature. Starting with just a small workshop, Bernhard Steinel has created a leading company in the machine construction sector. However, this indefatigable entrepreneur is not able to enjoy his success for long: in 1962, the company founder dies at the age of 75 after a short illness.
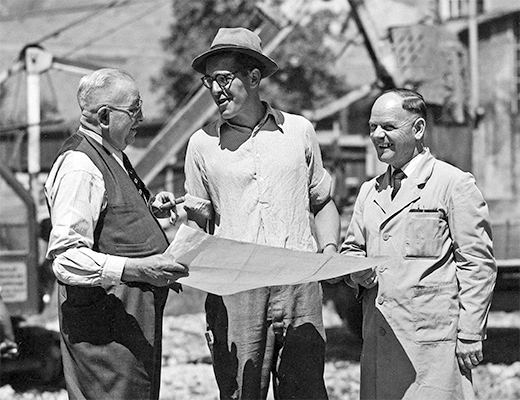
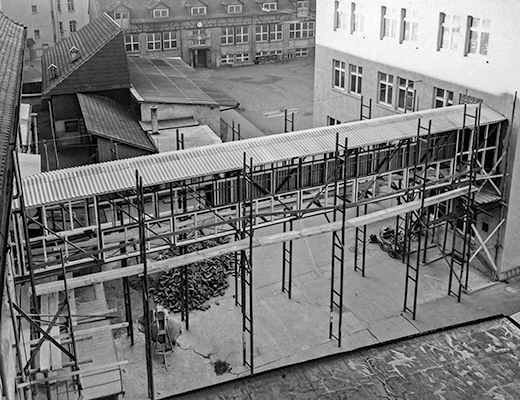
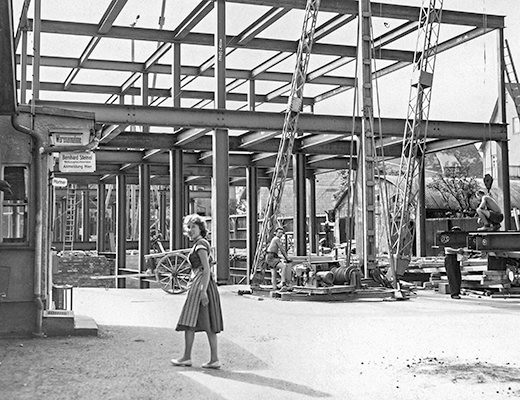
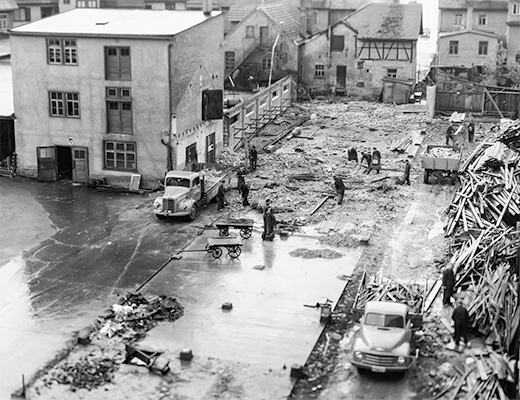
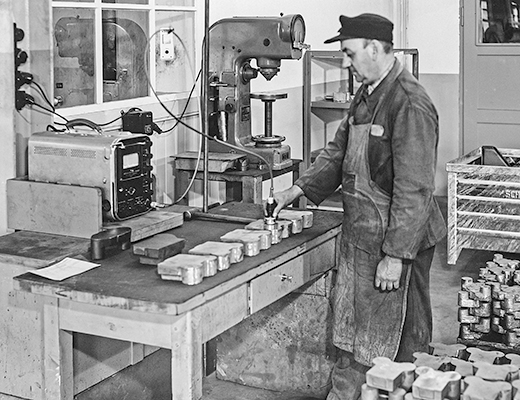
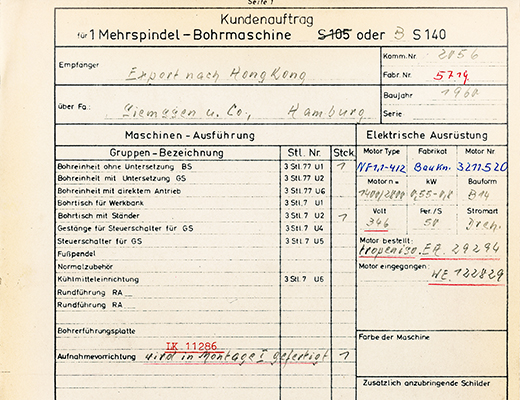
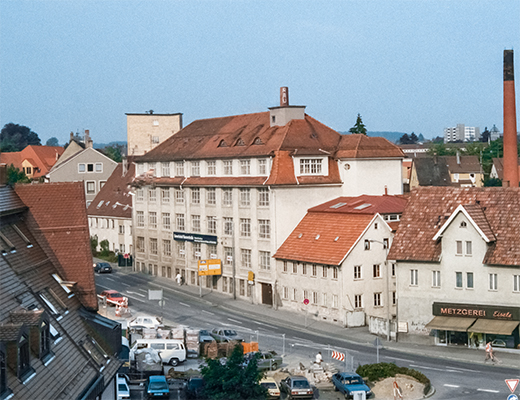
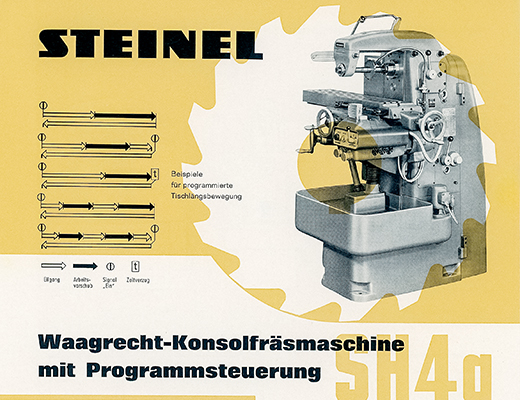
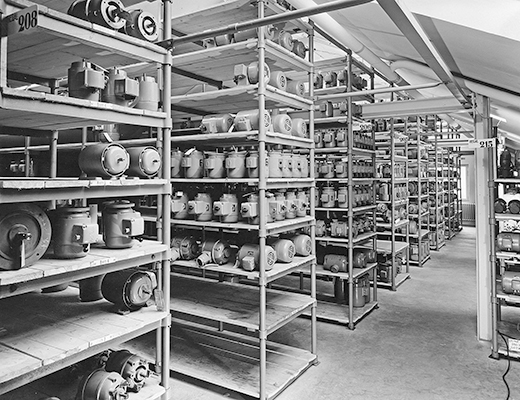
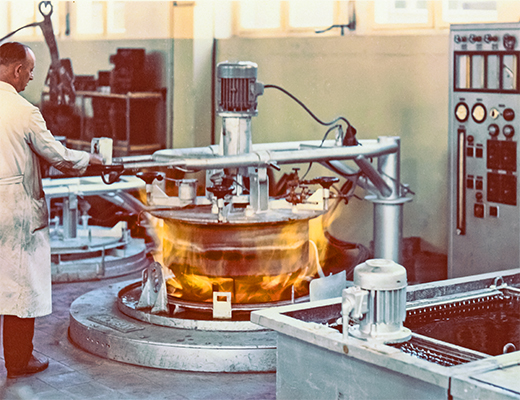
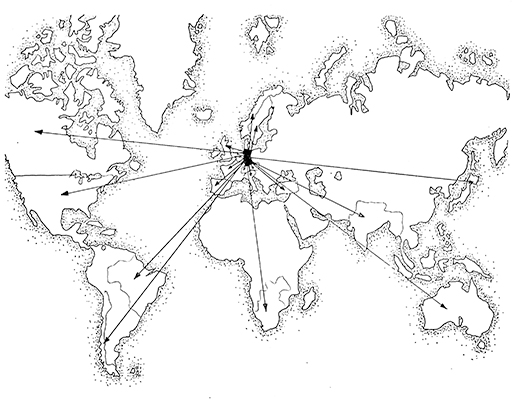
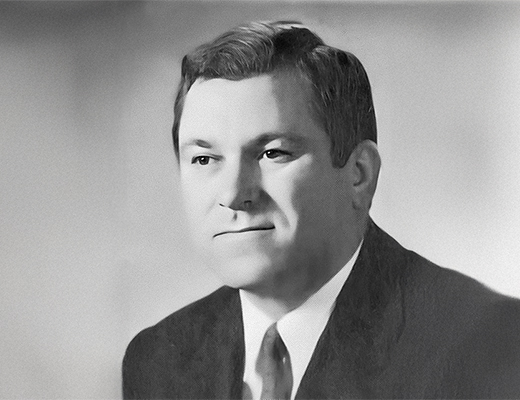
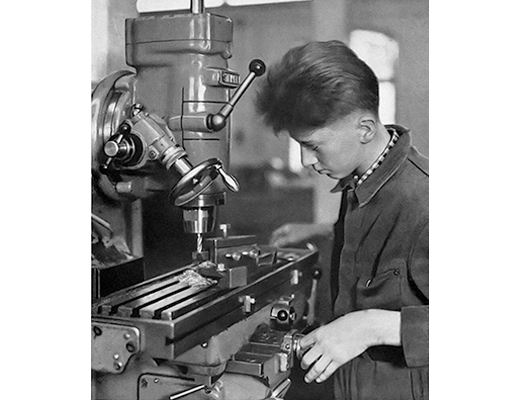
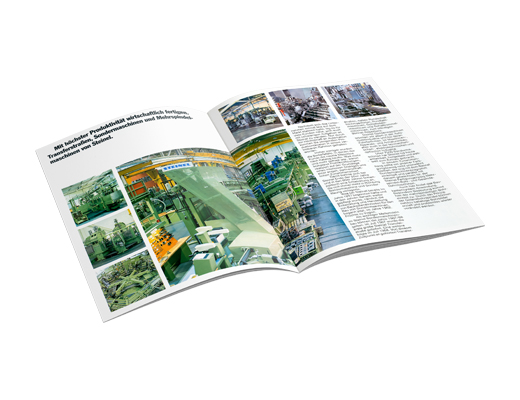
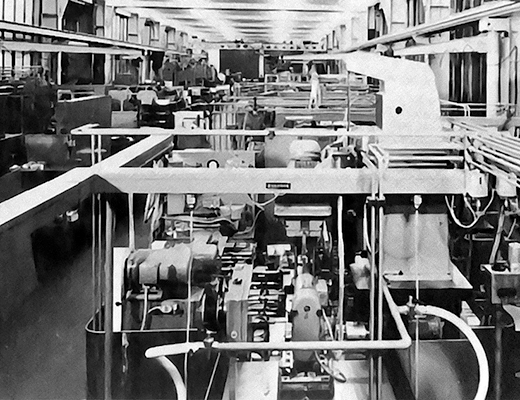
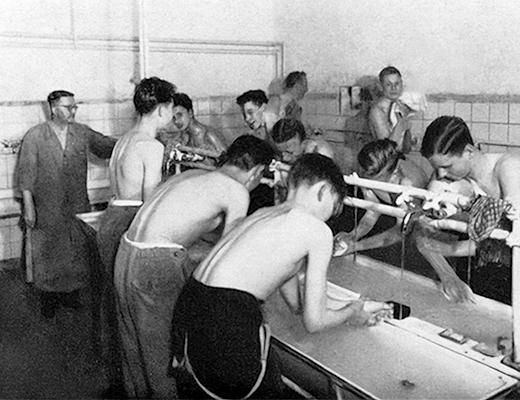
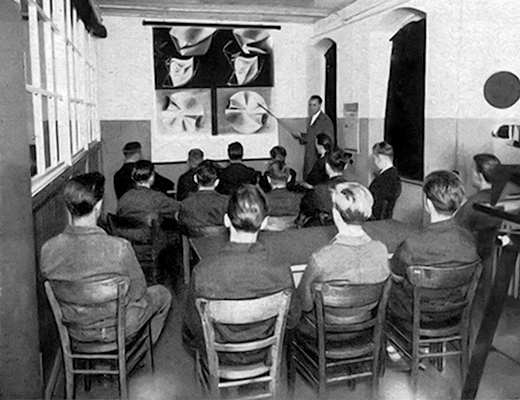
Second generation takes charge of running the company
His son Bernhard A. Steinel takes the helm of the company and continues to navigate a successful course. The new company boss brings great energy to driving forward the modernisation of organisational and technical aspects of the business, a process that began several years previously. This involves consistently purchasing the most modern production equipment, the ideal way to complete the restructuring from a master craftsman's business to an efficient industrial company in short order.
Great emphasis is placed on the training of qualified specialists. Ever since 1938, the company has run its own training workshop. Here, full-time instructors teach young people skills for their future careers. After just four decades, no fewer than 1,350 people have completed this training programme. In 1984, the German President praises the company for its outstanding achievements in vocational training. Having these well-trained skilled staff with their in-depth expertise is an important factor behind the success of Steinel as a company.
Read moreDigitalisation and further training of the workforce
Soon, almost nothing will happen in the company that does not involve the use of a computer. To satisfy ever more demanding requirements, Steinel also leases computer capacity from a local bank, the Schwenninger Volksbank. On Friday, the computers at that bank are hard at work for Steinel. At this time, programming by punch card represents leading edge technology. Last but not least, the company is setting up its own in-house DP capability, but it first has to train its payroll staff. As a consequence, Steinel’s salaried staff ‘get sent back to school’, attending training courses right across Germany. Once back at their desks, they work away on their terminals and the computer churns out huge reams of paper. The entire output of the computer is printed on continuous paper. Each year, it gets through no fewer than 18 pallets of this paper.
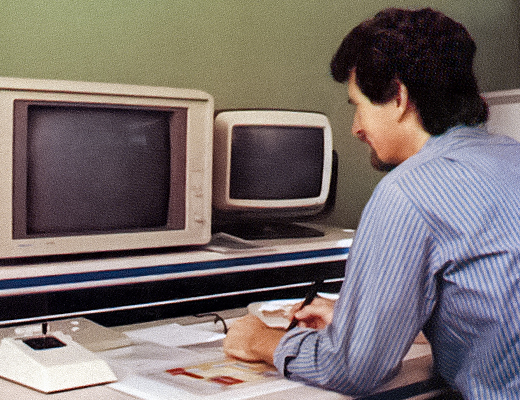
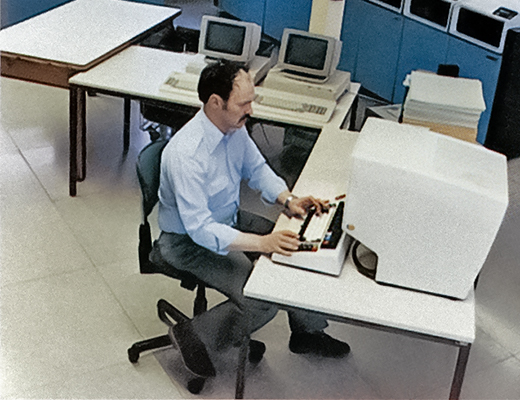
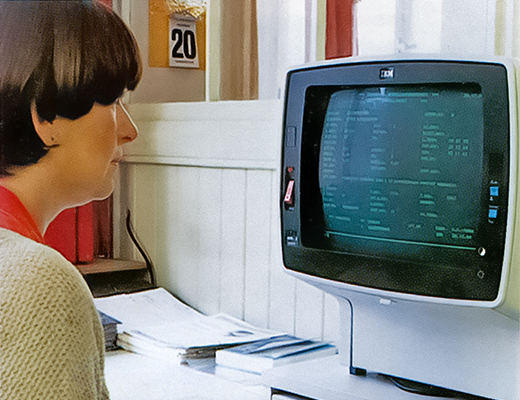
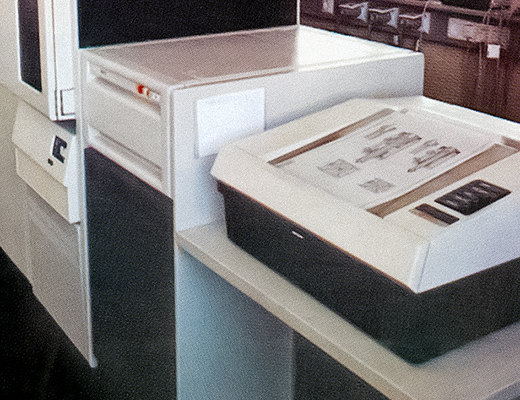
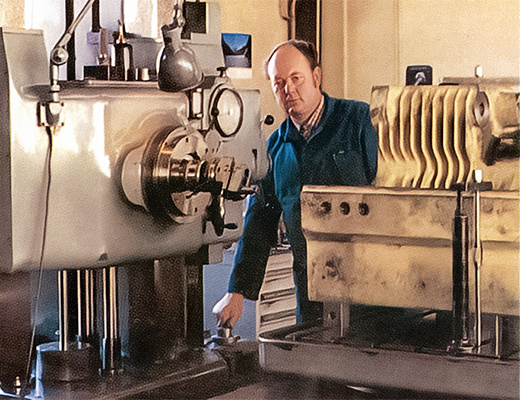
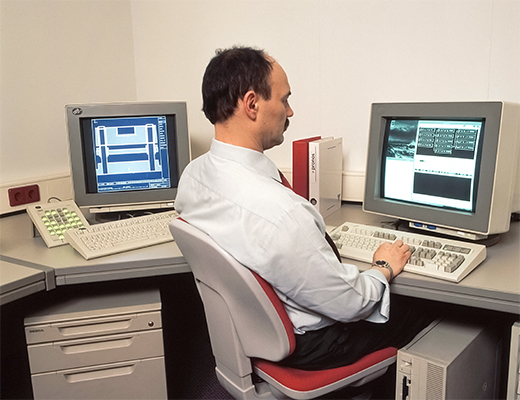
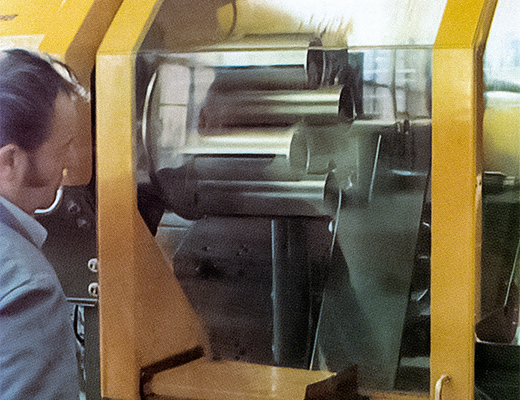
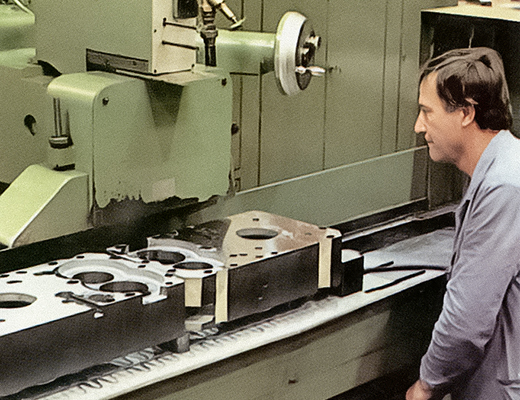

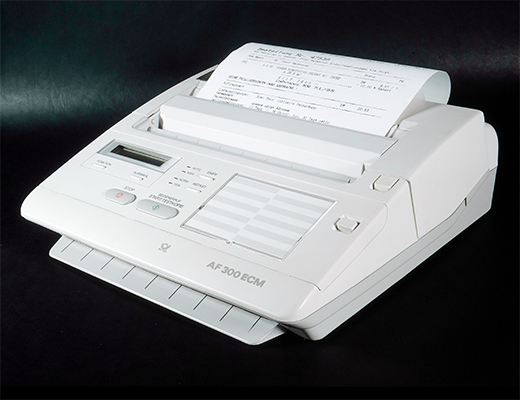
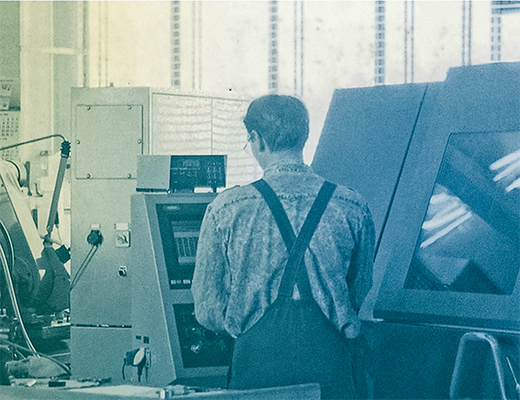
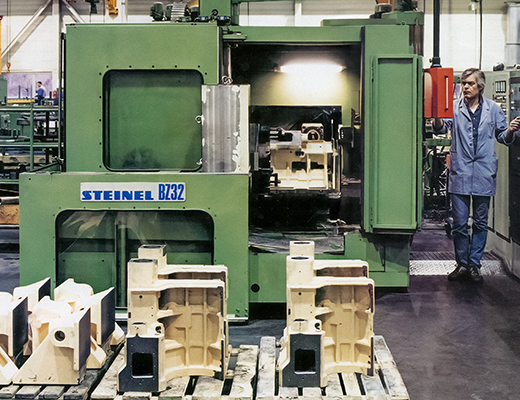
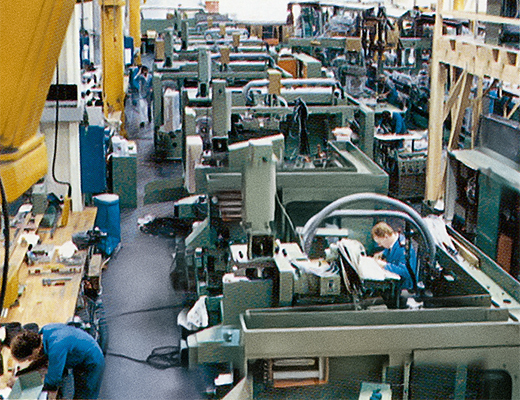
Even greater precision with CNC machines
CNC machines really are in the ascendancy now. Computer-numerically-controlled (CNC) machine tools enable material to be processed very precisely indeed. They make it possible to produce components to high standards of precision and repeatability. Their big advantage over manually operated machines is that they work autonomously, performing many tasks without human intervention as soon as one of their programs starts running. These machines owe their tremendous precision to their computerised control system which enables them to perform complex and detailed work, achieving zero-defect output even when repeated on a large scale.
However, the advent of the personal computer, the PC, still lies some years in the future. It is not until April 1990 that the company’s first PC gets installed in the Sales office. Individual departments are allocated set times when they can use this new computer. In-house communication uses a fax with thermal paper, printouts from which reach their recipients using the company's pneumatic tube system. An e-mail system is not introduced until 2001, a delay due in large part to security concerns.
In demand across many sectors
Steinel's special machines are in demand in many industrial sectors. Primarily, Steinel machines are used by the automotive industry and its suppliers, by the mechanical engineering sector, in the manufacture of apparatus and fittings, but also in the precision mechanics, electrical engineering and optics industries. Of course, the popularity of these products is also reflected in the constantly increasing numbers of finished products that leave the factory. In the early Eighties, the company is proud to announce that it has already developed, produced and sold over 7500 of its customised machines. Another sector, involving the production of multi-spindle drilling and tapping machines, has close links to this range of customised machines. That sector is flourishing in parallel to the successful range of customised machines. Steinel’s proven modular system also comes up trumps in this sector. This is particularly evident in the efficiency of the articulated drilling spindle principle: This makes it possible to create almost any drilling template and to modify it again just as easily.
1975 is a pivotal year in the history of the company. As it celebrates its 50th anniversary, the company employs a workforce of 1000 people. The production range extends across two fields of activity. The first of these is machine tool construction sector. Here, customised or ‘special’ machines, NC machines, multi-spindle machines, riveting machines and milling and drilling machines are manufactured. The second is the standard parts sector which manufactures tools and fixtures. Column frames, guide elements, cutting elements, spring elements and accessories are manufactured and sold here. The output levels achieved up to this point are impressive, a testament to the company’s success. In its anniversary year, Steinel has produced around 8000 units and 59000 machine tools since the end of the war. These include 7000 special machines and 19500 milling machines. Over and above this, 150 modern NC machines have been manufactured in the last decade.
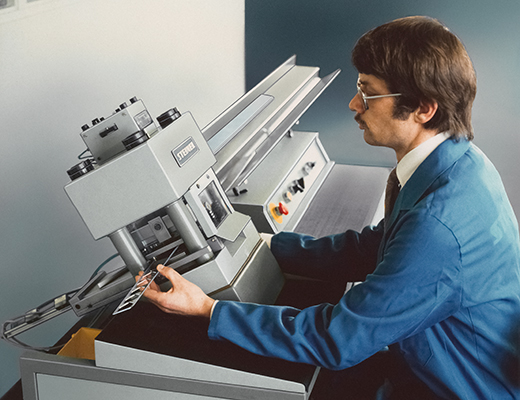
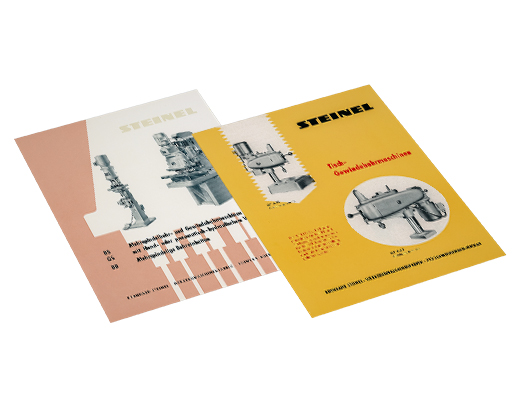
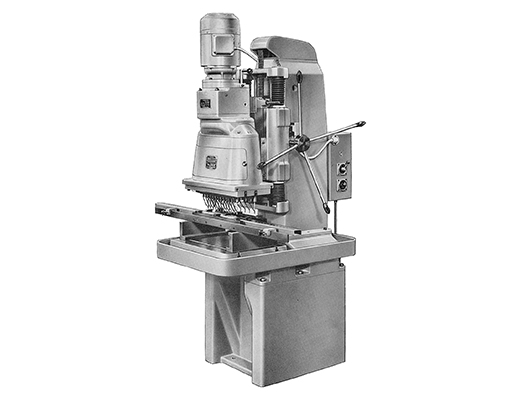
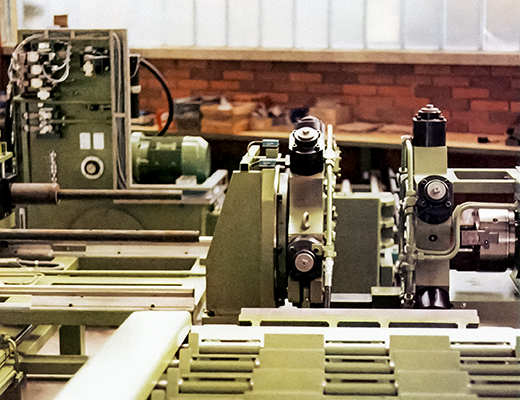

The start of plant construction
On the strength of the depth and breadth of experience of its design engineers and workforce, Steinel now considers itself ideally equipped to enter the plant engineering sector. This constitutes a big step into the future. The company is now literally able to offer its customers complete turnkey production systems. Steinel covers the entire spectrum from raw materials to production and testing, right through to on-site installation of the new plant. To provide solutions to problems of this level of complexity, Steinel engineers draw on in-house products as well as on machines from other manufacturers. The company now possesses extensive expertise, especially in the planning of plant for the production of pipes, sleeves, drilling chisels as well as the drill bits used for oil and gas extraction. This is in demand right around the globe. Steinel now supplies and installs its technology in Austria, Japan, the USA and even in the Soviet Union. This includes CNC turning machines, deep-hole drilling machines, specialist machining centres, assembly machines as well as a multi-faceted range of testing and measuring systems.
A big growth market
The business sector plant construction is emerging as a major growth market and the company is devoting a great deal of brainpower to it. The aim here is to identify solutions to problems that deliver optimum benefits to its customers. Right from an early stage, the specialists at Steinel recognise the importance of numerically controlled machine tools. The company unveiled its first NC machine at the Hanover Trade Fair back in 1964. The FH 6 drilling and milling machine is just the very beginning; it is followed in 1970 by the first Steinel machining centre. The BZT 40 is a larger feeder with an NC rotary table, a 40-slot tool magazine, a device for changing tools and pallets and a workpiece coding device. In technological terms, this system is way ahead of its time; even many years later, this machining centre is still able to hold its own against the more recent models available on the market. Into the future, the development of machining centres will remain a high priority at Steinel and will continue to be promoted vigorously. In 1973, the BZ 30 and the RBA 2 turret drilling machine are launched on the market. The BZ 30 quickly becomes a real best-seller: In just four years, no fewer than 100 of them are produced and sold. This makes it the best-selling machining centre in its category.
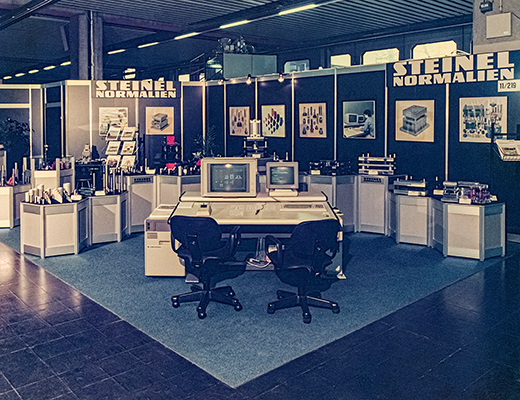
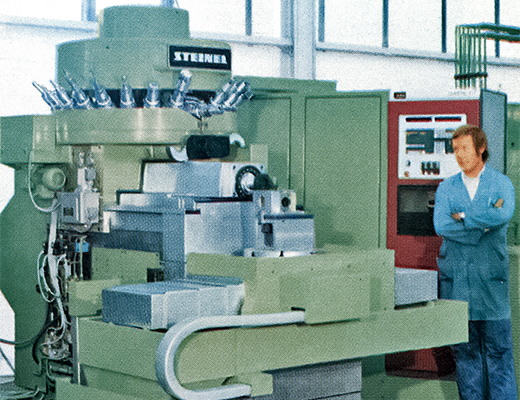
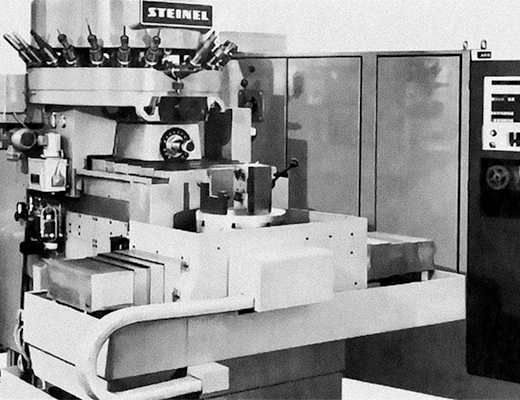
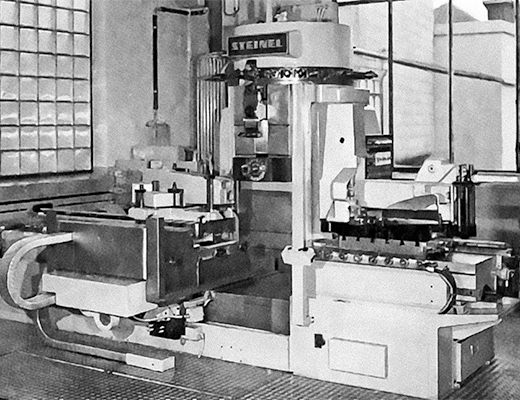
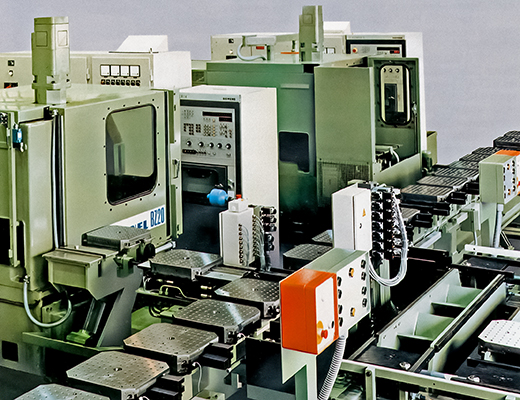
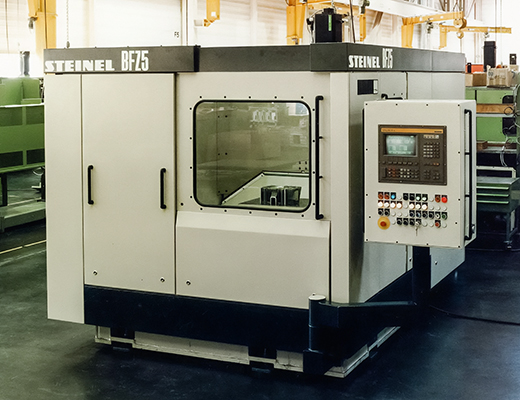
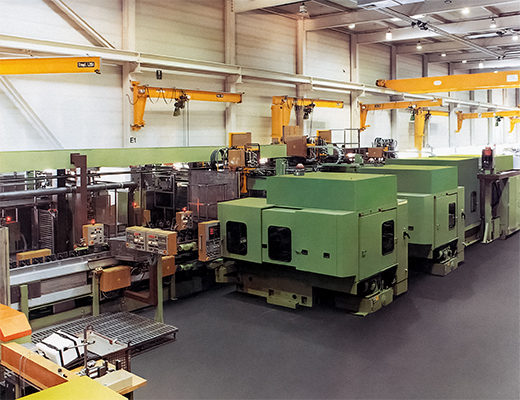
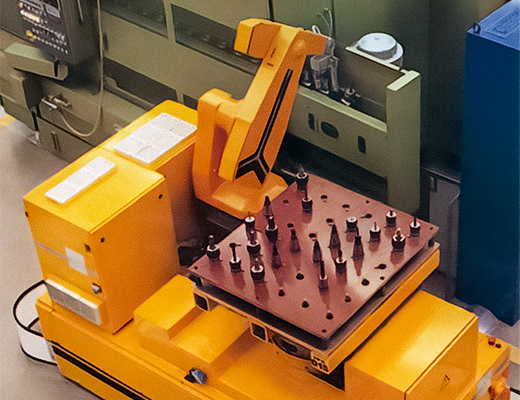
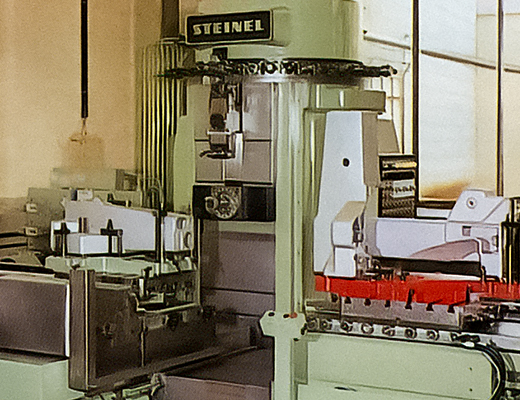
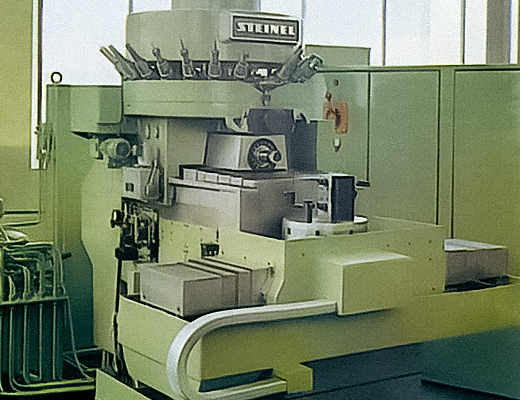
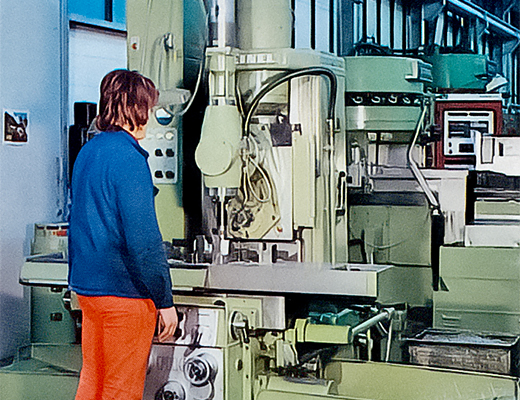
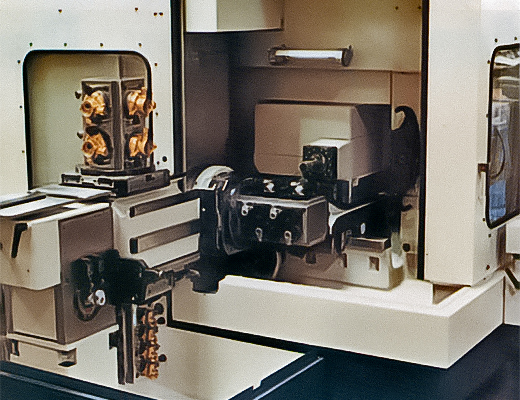
Smaller, but greater performance
The company then goes on to achieve a major success in 1977: Steinel presents the BZ 20 - a complete machining centre that can be used to manufacture small workpieces. These are however time-consuming to machine. This is an important success because before this, it was not possible to produce workpieces of this kind efficiently enough on machining centres. That was because the systems used in the past were too large, too cumbersome and therefore too uneconomical. The Steinel development team turns all of this on its head. This new machine delivers savings in throughput and production times on a scale previously inconceivable in the machine construction industry, in automotive manufacturing and also for the manufacturers of optical devices, precision mechanics and electronics. The great advantage of NC technology is that it makes production equipment a great deal smaller while also increasing its performance capabilities by a large margin. The BZ 20 is also in operation in companies for which the big machining centres that pre-dated it were too expensive.
Read moreComputer controls machine
As a manufacturer of smart manufacturing systems, Steinel is also sought ought by Zeiss to partner it on a pioneering project. This involves the pilot plant for a flexible manufacturing system capable of machining 150 different workpieces. This is made possible by the computer-controlled system featuring four BZ 20 machining centres with pallet changing device, pallet storage with 30 slots, a loading and unloading area, an NC-controlled transport carriage and a measuring machine. This new product attracts a great deal of interest at a public demonstration of the commissioning process. In the course of that same year and again in 1984, Steinel supplies a flexible production system to Bosch. These systems now feature four BZ 20 and four BZ 25 machining centres with 80 twin-spindle heads. These are interconnected by a modular pallet transport system. Handling devices load and unload these systems. However, that is only the beginning. Many more flexible production systems of a similar design are supplied to leading companies. For all of these projects, Steinel is able to draw upon its extensive experience in the construction of special machines that employ NC technology. These two complementary areas are combined to satisfy demanding requirements. This makes it possible to manufacture even more productive machining centres. This is achieved using multi-spindle drilling heads with automatic workpiece feed, while the integrated NC units and automatic tool changers enhance the flexibility of these customised machines.
This same time heralds the first deliveries of flexible production lines comprising tried-and-tested standard units together with recently developed units from the NC modular system. A good example of this advanced solution is the BZE 200 CNC machining unit. All three of its axes are located in a single tool. This is an ideal format for integration into rotary transfer machines and transfer lines. The computer is now an integral part of it all. These systems are equipped with tool monitoring devices, fault diagnostics and computer terminals; some are already connected to higher-level production computers.
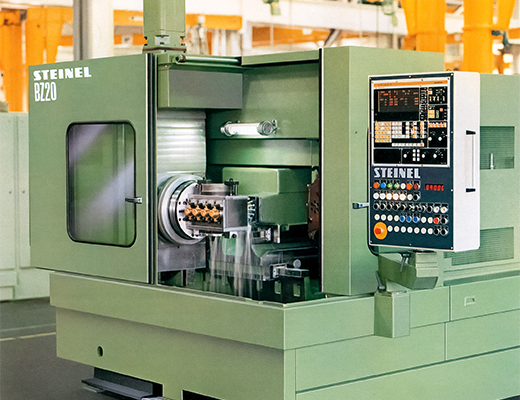
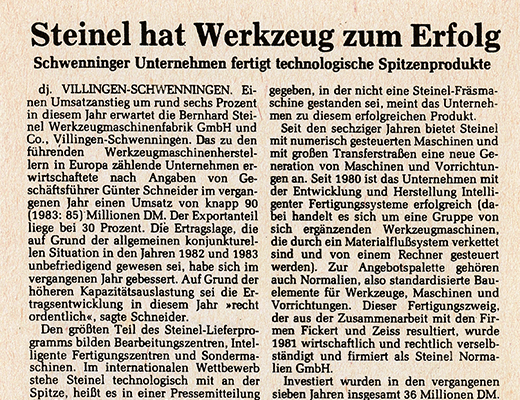
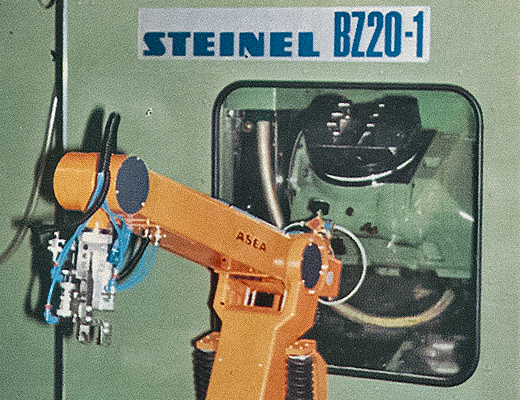
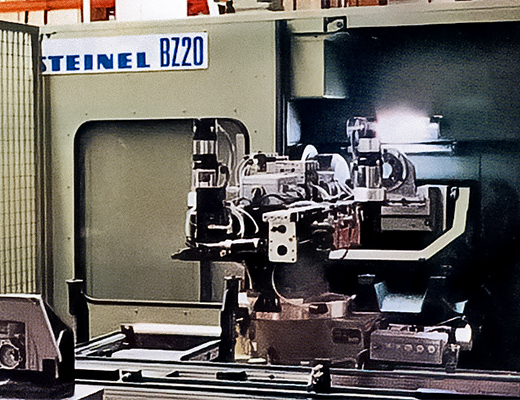
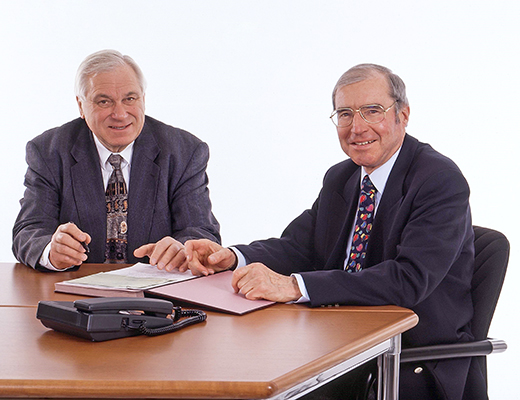
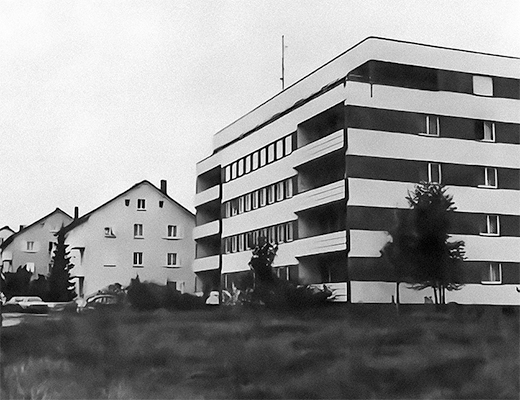
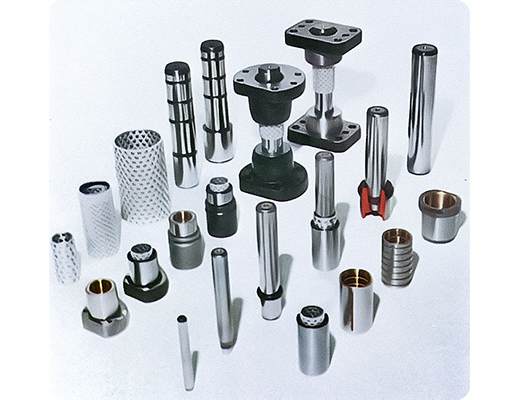
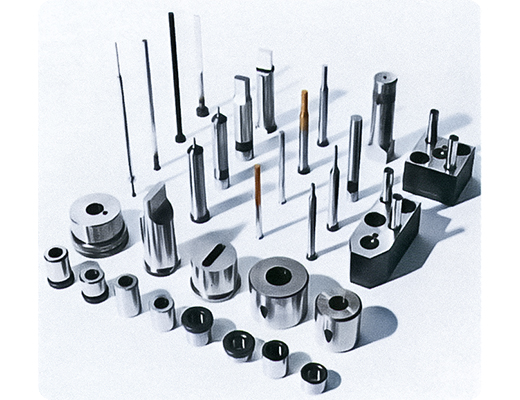
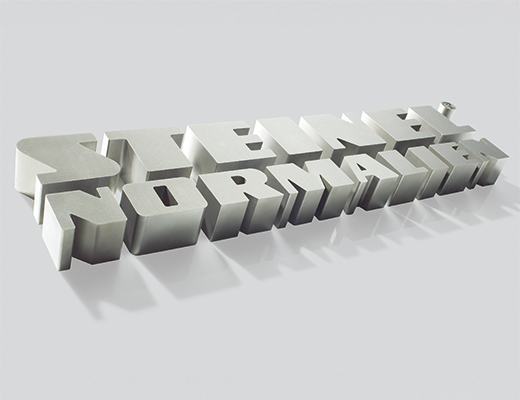
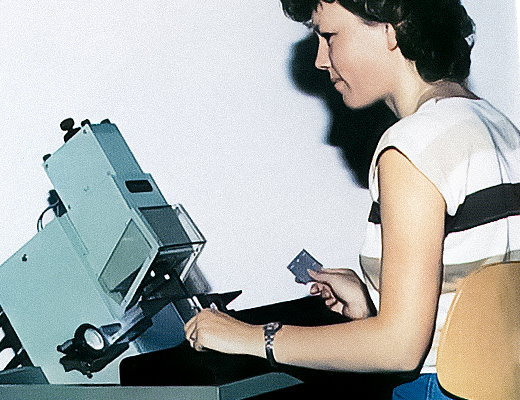
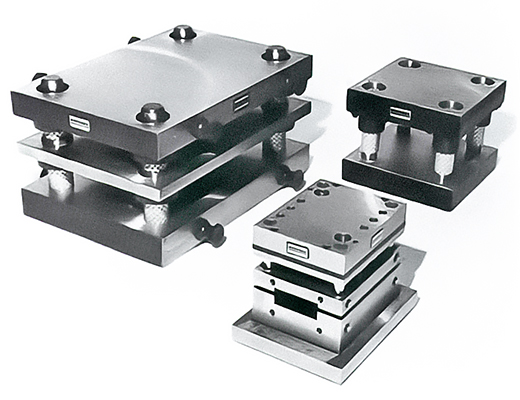
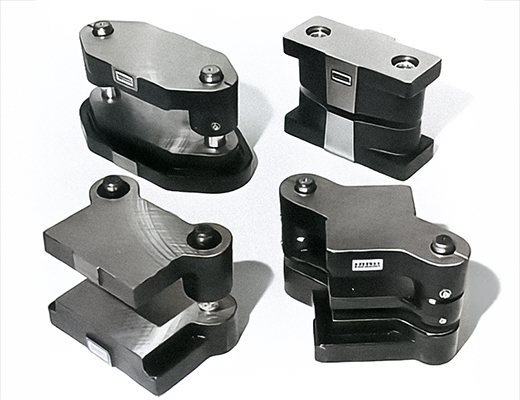
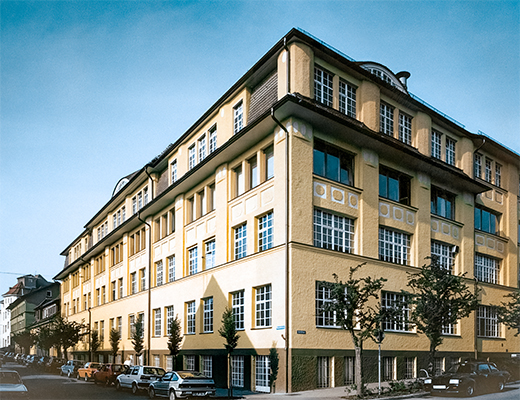
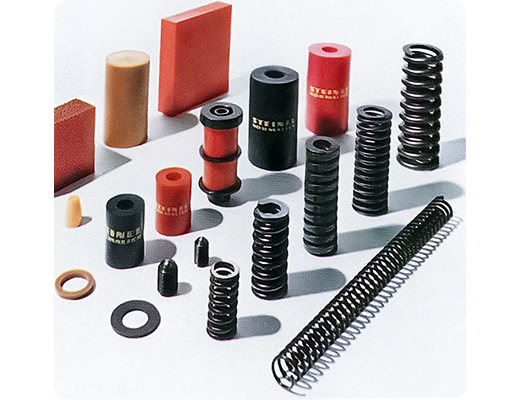
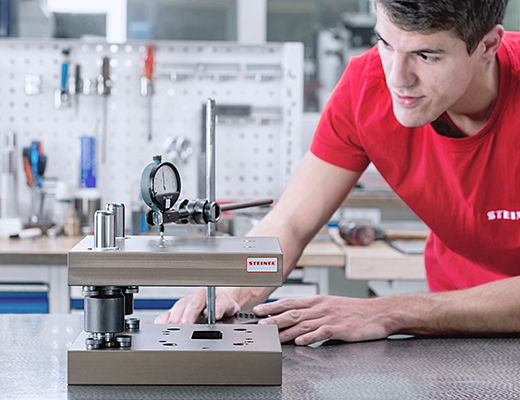
The founding of Steinel Normalien GmbH
The big turning point occurs in 1981: Steinel Normalien GmbH is founded on 11 September and what was previously just one aspect of production operations is now listed in the commercial register as an economically and legally independent company. The company directors are Bernhard A. Steinel and Günter Schneider, while Joachim Mayer and Helmut Timm are appointed as authorised signatories. The share capital of almost four million Marks comes from the sale of the former company apartments built by Steinel Wohnungsbau GmbH in the Fifties and early Sixties on Brühlstrasse and Rottweiler Strasse. Construction of these was prompted by the housing shortage in the years after the war, an important piece of social welfare for company employees at the time. However, by 1980, the situation had changed completely: There is no longer any shortage of rental accommodation and by this time, almost none of the remaining tenants in the Steinel buildings are company employees. The owners therefore decide to sell the property to Südgrund GmbH from Stuttgart. This creates a strong starting position for Steinel Normalien GmbH, which also sells its existing stocks of standardised finished products to the machine tool factory.
Read moreNew production building for the machine tool factory
In response to these challenges, Steinel decides to build a new, modern production building on the industrial estate at the eastern side of town, beside the airfield. In 1981, construction of the new plant, ‘Werk A’ on Albertistrasse, reaches completion. Further expansion soon follows. Ultimately, after all of this expansion, the new buildings with assembly shop, high-bay warehouse and an office building for production-related departments will extend over an area of 42,000 square metres. The company now has crane systems with lifting capacities of up to 32 tonnes, equipping it with ideal production conditions for the manufacture of its heavy machines. A shuttle bus service connects the two production sites on Winkelstrasse and Albertistrasse, transporting employees to their workplaces. In the modern day, that evokes nostalgic memories for employees, another being the presence of a security guard at the factory gate on Winkelstrasse who took care to prevent any unauthorised persons from entering the factory premises. And anyone actually on-site is obliged to follow instructions to the letter: The security guard at the gate makes a point of ensuring that no-one exceeds the maximum speed limit of ten kilometres per hour in the factory yard. This sometimes prompts very heated exchanges which, as long-serving Steinel residents remember with a grin, were always decided in favour of the guard at the gate.
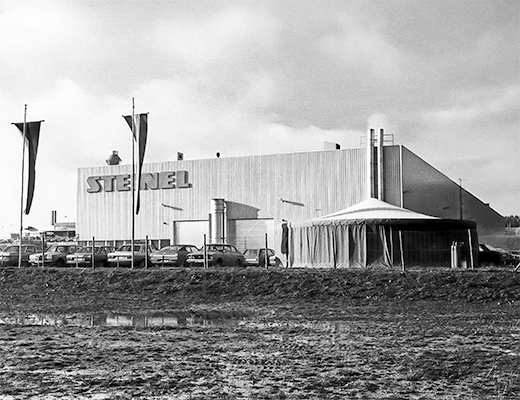
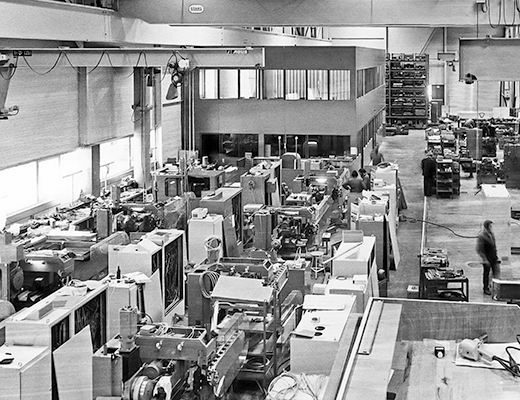
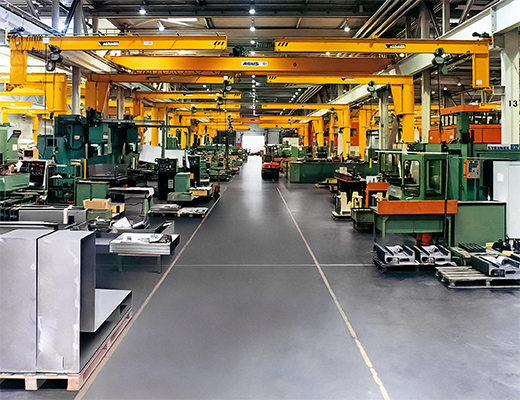
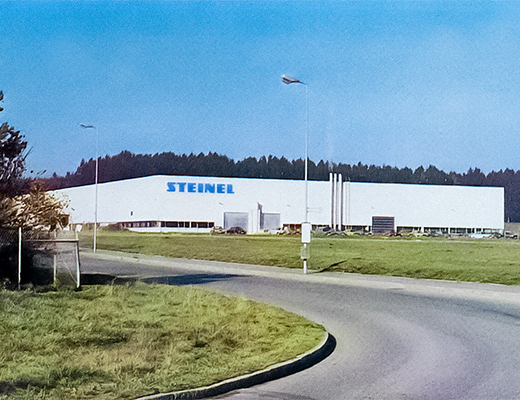
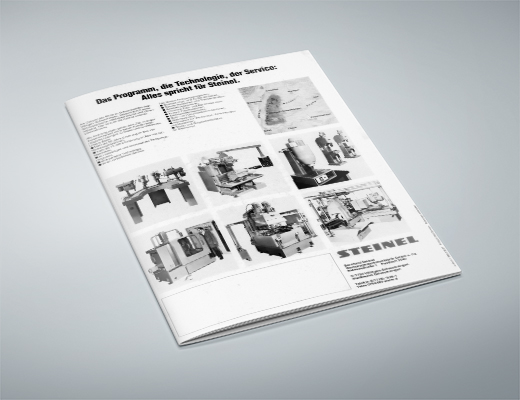
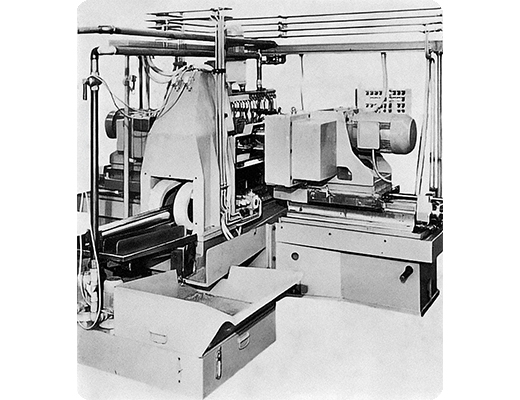

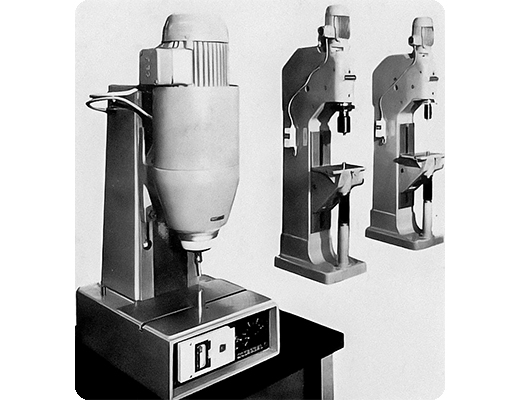
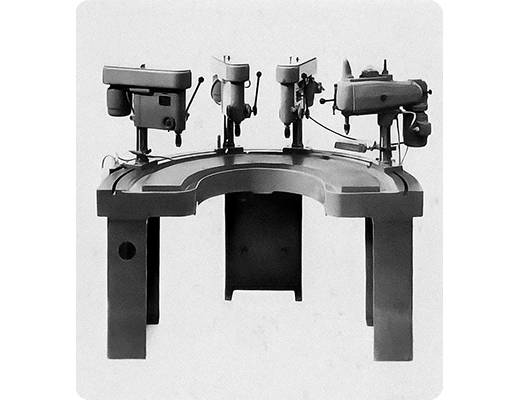
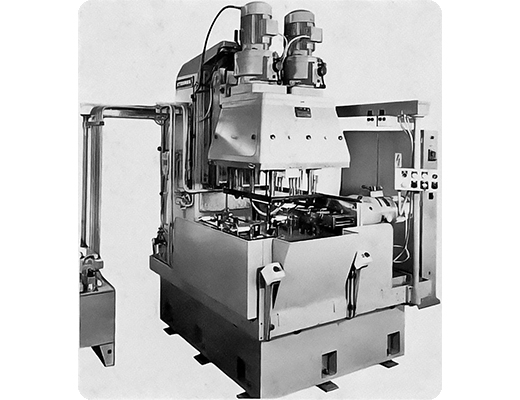
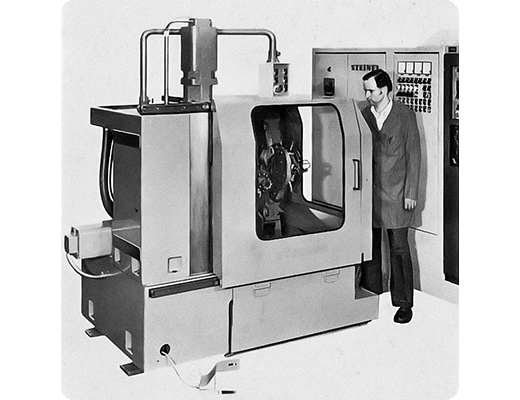
Challenges of the Eighties
Mind you, in the Eighties, there are soon greater concerns than traffic regulations on the factory premises: The situation on the machine tool market takes a turn for the worse. Despite its improved infrastructure, the company comes under economic pressure in the Eighties. The machine construction sector faces major challenges, including strong competition from German manufacturers such as Gildemeister in Bielefeld and Maho in Pfronten, Bavaria. Both of these companies have very successful track records in this sector. In addition, the pre-financing of these expensive machines, often each costing between two to three million Deutschmark, imposes a significant strain on the company’s financial situation. In line with common practice in this industry, Steinel does not receive payment until after it has delivered its products to customers. Consequently, long periods of time need to be bridged financially. Between 1981 and 1983, many employees at the machine tool factory lose their jobs.
Search for a capable partner
However, downsizing the workforce is not able to improve the situation in any fundamental way. These financial burdens compel Steinel to seek out a strong partner who can safeguard the future of the company. By taking this step, the company seeks to maintain its competitiveness. It also wishes to enable its great tradition to continue. In 1986, the company formally separates its production operations for standard parts and machine tools. In December 1986, Steinel Normalien GmbH acquires the factory premises on Winkelstrasse and Rathausstrasse in Schwenningen, a site with strong traditional roots. Here, on the site where the machine tool factory had been writing a success story for so many decades and where it grew to maturity, the independent company now sets its sights on the future. Normalien GmbH also severs its corporate legal ties to the parent company: At the beginning of 1987, Steinel Normalien GmbH takes on the employees from the standard parts production division. It now has a payroll staff of 125 and is now a fully integrated company, from production to sales.
Meanwhile, the shareholders are looking for a buyer for the machine tool factory. A white knight duly appears in Schwenningen, in the form of the Austrian industrial group Voest-Alpine AG. In 1987, the management team from Linz takes over Steinel Werkzeugmaschinenfabrik. They wish to establish their own machine tool manufacturing capability within their industrial conglomerate. Until this time, their business focused primarily on steel production. Employee morale is subdued. They are unsure what to expect from the Austrians. Feelings are running high at the works meeting, held in the City cinema right next door to the company premises. Everyone at that meeting still remembers what one employee said about this commitment from the Alpine republic: “Better to be red-white-red than dead”.
Nonetheless, this company with its wealth of tradition, was only granted a reprieve spanning ten roller-coaster years. In 1999, the Villingen-Schwenningen district court opens insolvency proceedings against the company's assets. This marks the end of a long history for this machine construction company. However, the factory site at the airfield with its impressive production building is still bustling with activity. The Müga company, owned by two former Steinel employees Peter Gary and Helmut Müller, acquires the company property from the machine tool factory. These two business owners are therefore returning to their old place of work: Gary was the service manager at Steinel-Werkzeugmaschinenfabrik while Müller was in charge of sales. Müga acquires the service rights for machine tools and also the very well-stocked spare parts warehouse. This ensures that expert service staff are on hand to support Steinel machining centres in Germany, of which about 300 are in active service.
The production areas and offices that Müga does not itself need are leased to other companies and institutions. Even after end of the Steinel era, an innovative atmosphere can still be felt in the East Industrial Estate, creating something new with ideas and inventiveness, in keeping with the tradition established by company founder Bernhard Steinel.
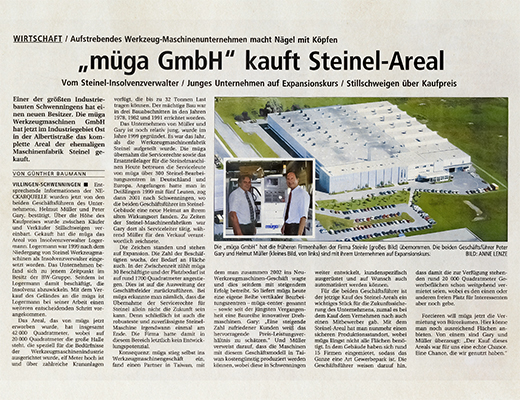
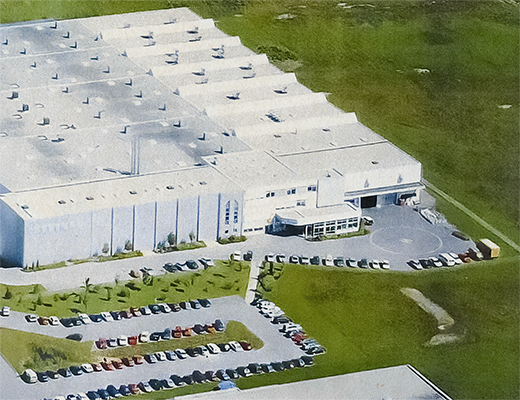
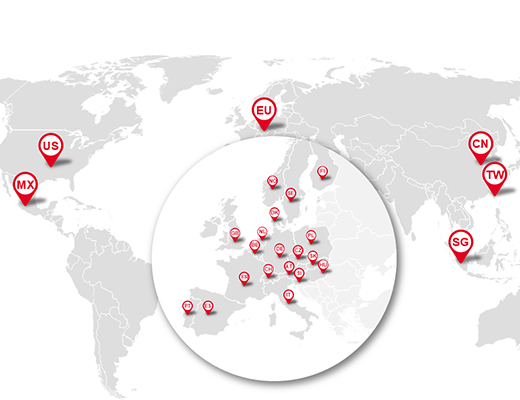

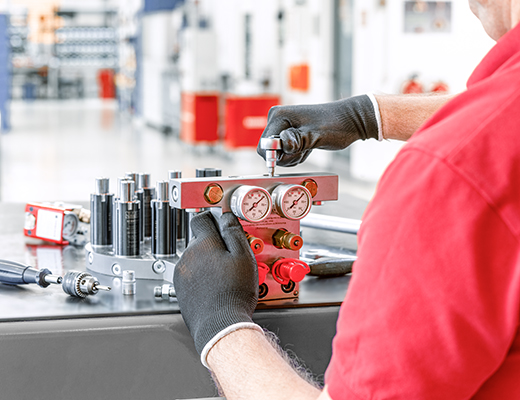
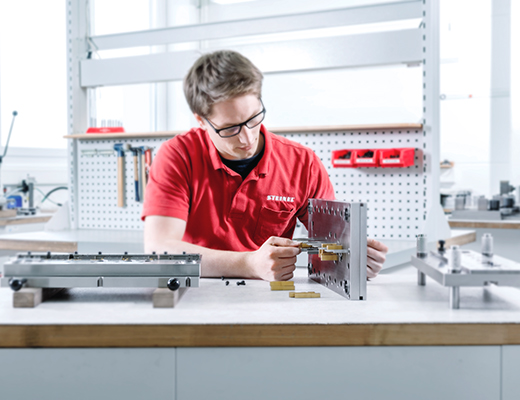
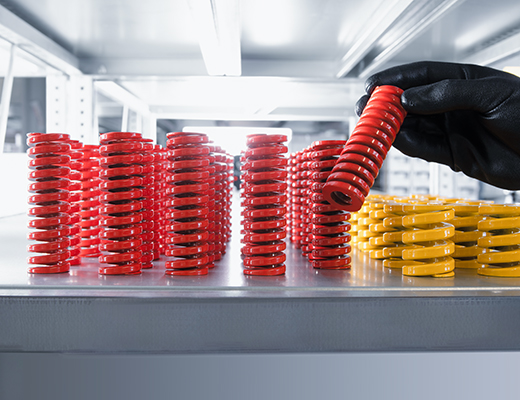
Extended product range and internationalisation
The production range continues to expand, accompanied by continuous fine-tuning of quality and precision. STEINEL is actively involved in standardisation in the toolmaking sector and it assists with the creation of applicable standards. In 1990, standardised parts are incorporated into the STEINEL product range in accordance with DIN standards. One year later, the range is extended to include system springs and nitrogen cylinders. In 2006, STEINEL becomes the first standard parts manufacturer in Germany to develop and produce its own nitrogen cylinders for demanding applications in punching tools. This establishes a unique market position for Steinel. Steinel and its customers all benefit from this. This is thanks to the remarkable longevity and reliability of this in-house development. Steinel nitrogen cylinders achieve an impressive length of service life. This longevity is of huge benefit because these nitrogen cylinders are used in cutting and forming tools that perform repetitive operations. Today, Steinel has almost 20 000 different items in its product range for companies involved in the construction of moulds, fixtures, plant and machinery.
Read moreThe first website for a German provider of standard parts
In 1997, for many German companies, the Internet is still a mysterious new territory. Websites are still something of a rarity, and the notion that companies could showcase their products and services online is anything other than a widespread phenomenon Nonetheless, while others were still reluctant to take the plunge, Steinel becomes the first supplier of standard parts to venture into the digital age.
Although the .de domain was introduced back in 1986, it remains almost unused until the early Nineties. It is not until 1995 that commercial websites begin to establish themselves. Then, 1996 very well-known websites such as T-Online.de are launched. The following year sees the first offerings from banks and online shops. Then, starting in 1998, the number of websites also proliferates in Germany, due primarily to the increasing availability of DSL Internet connections.
With its self-confident motto of "50 years of expertise in quality - always one step ahead", Steinel projects a clear statement right from those very early stages that innovation and vision are core values of the company. The first website may have had a simple design, determined by what was technically feasible at that time, but its content is ground breaking. Steinel presents its product range in a clearly structured manner under the heading of “Our sales range for stamping and forming technology" Aluminium and steel column frames, guide elements, cutting elements, spring elements, accessories and machine elements.
One of the highlights on the website is headed “About us”. Here, Steinel not only imparts information, first and foremost it seeks to inspire confidence: An entire product range from a one-stop shop, featuring consistently excellent quality, a central warehouse with 25 000 products and a dependable delivery service - these are all messages that position Steinel as a capable partner.
At the time, having your own website is so unusual that the local newspaper Neckarquelle publishes a series of articles about the tiny handful of companies that already have an Internet presence. In Schwenningen, Steinel is a member of this exclusive group of digital pioneers.
At a time when there are only around 5000 to 10 000 German websites, a time when the Internet is populated for the most part by universities and large corporations such as BMW and Deutsche Telekom, Steinel is sending out a clear signal: The future is digital. With an electronic product information system on CD-ROM, CAD linking and the modern WorldCAT software for product research and order processing, Steinel is not simply being courageous, it is also demonstrating a profound understanding of the opportunities afforded by the digital world.
Today, almost three decades later, Steinel’s Internet presence constitutes a central building block of the company. Moreover, the pioneering spirit of 1997 lives on: As one of the first companies to recognise the potential of the Internet, Steinel remains loyal to its core beliefs - always one step ahead, always right up-to-date. An example of genuinely visionary corporate culture.
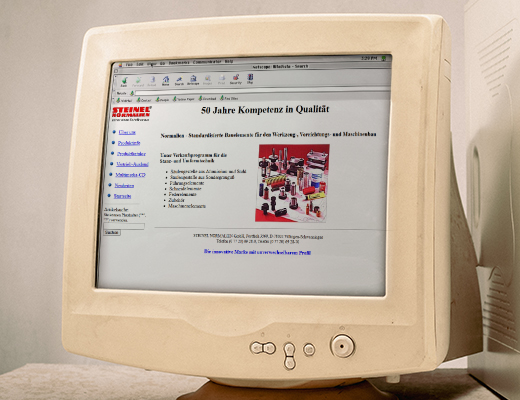
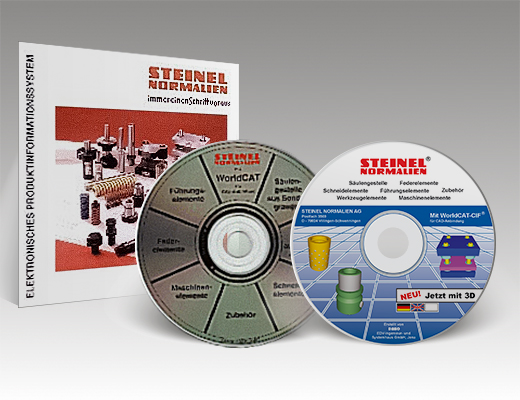
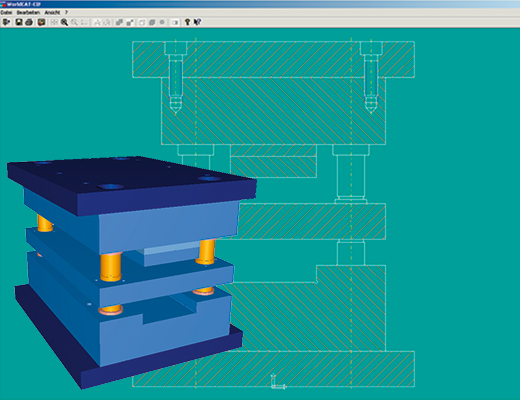
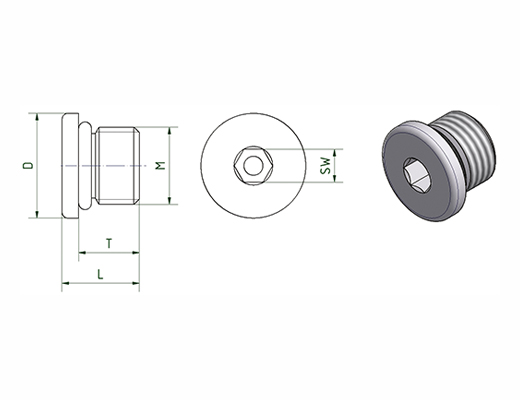
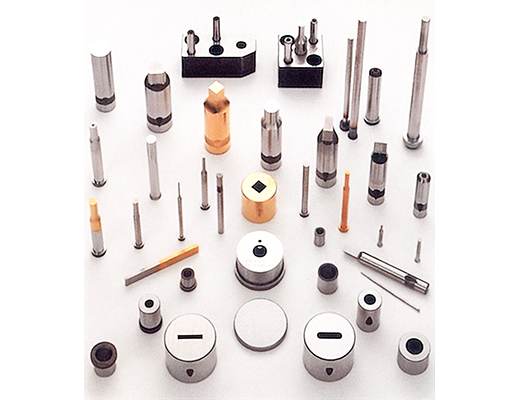
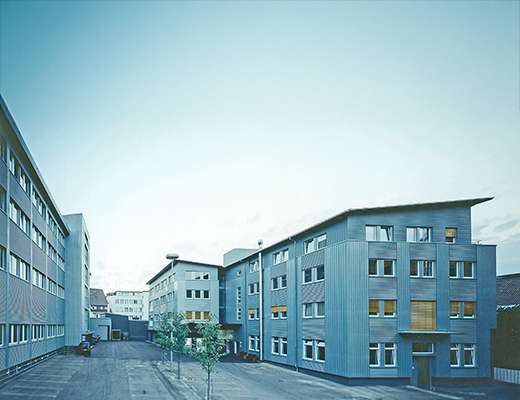
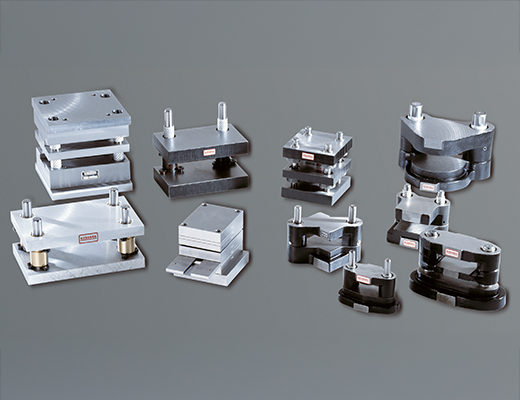
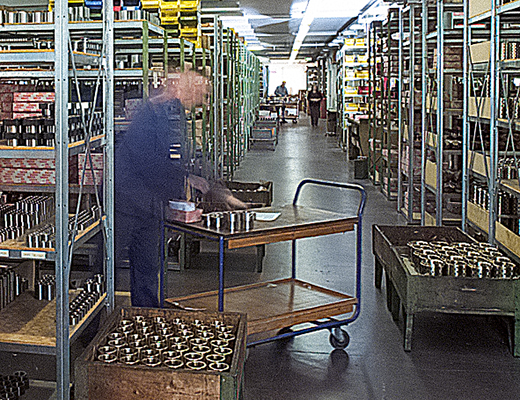
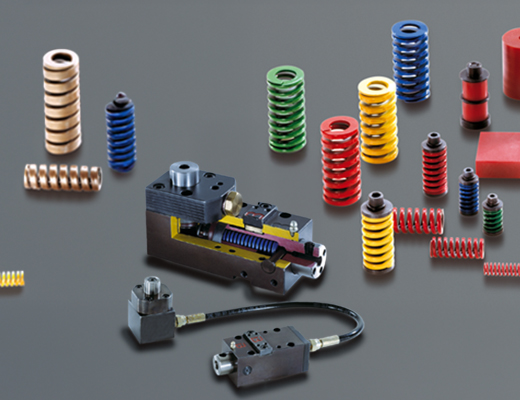
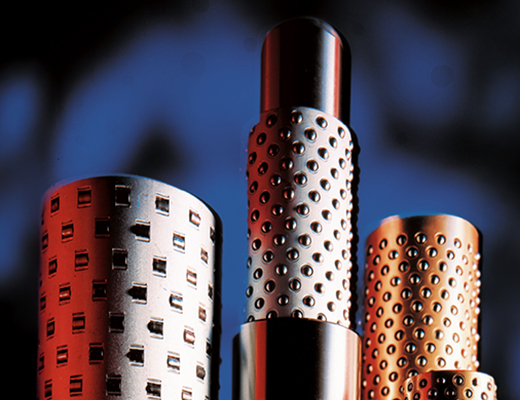
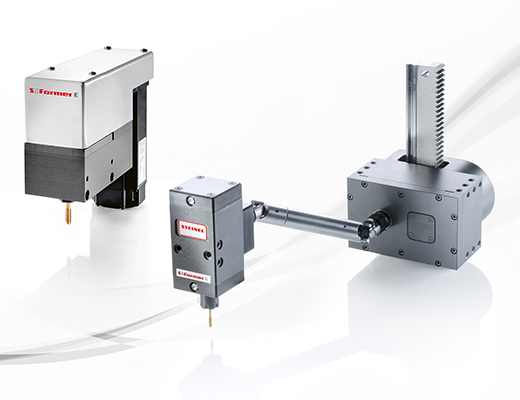
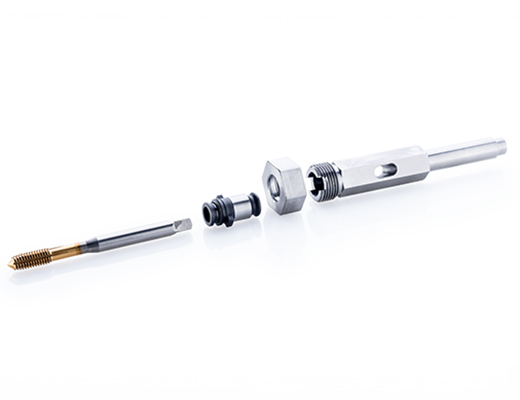
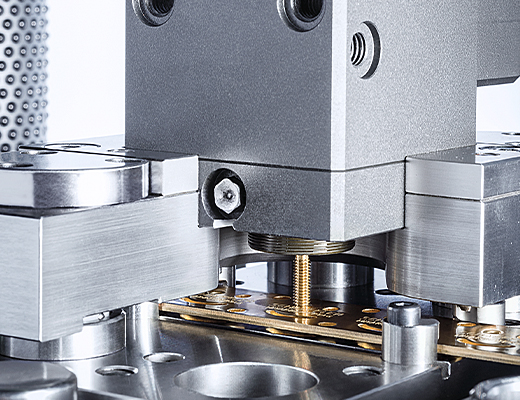
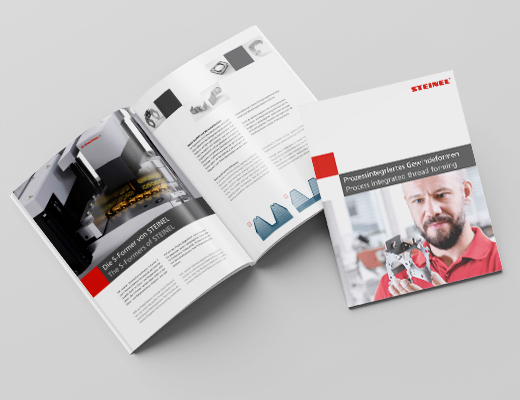
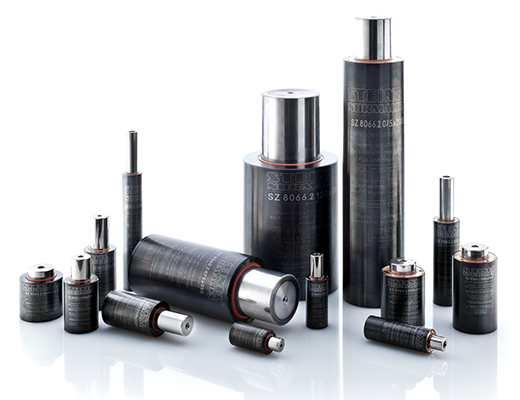
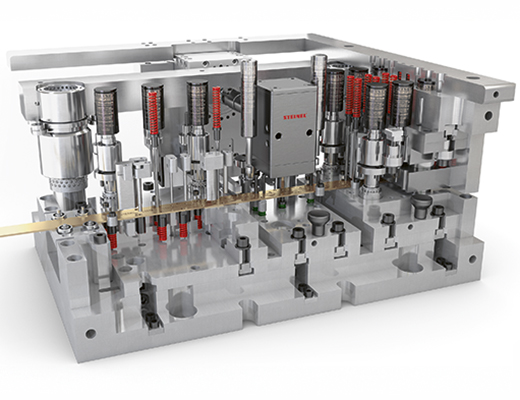
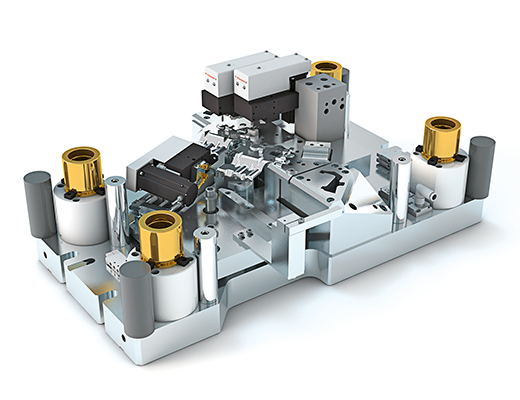
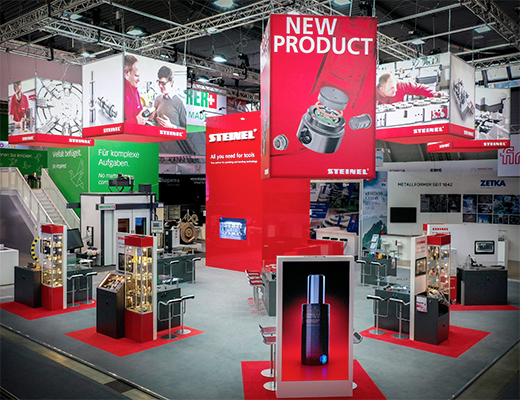
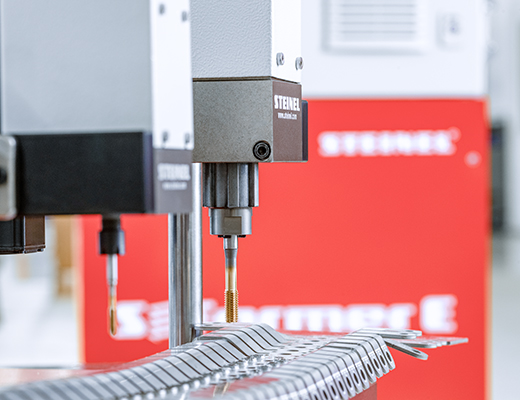
Innovations and patents
A fine example of Steinel’s potential for innovation is its S-Former range of tapping units.
The systems developed by Steinel’s creative minds translate into significant gains in productivity for its customers. This is because threads are produced directly in the punching and bending process. In contrast to cut threads, the metal structure of moulded threads is compacted. This delivers greater strength. Furthermore, the thread moulding process does not produce any chips which prevents moulds from getting contaminated. As a consequence, all necessary operations are completed in a single process. This results in a big increase in productivity combined with optimum thread quality.
Read moreThe Halblech site at Buching im Allgäu
In 2009, Sesselbahnstr. 7, not far from the fairytale castle, becomes home to the newly founded company of Steinel Aktivelemente GmbH. This site focuses on the manufacture of active elements and also on the design and manufacture of tool modules and complete tools for stamping and forming technology. This expands the product portfolio of STEINEL Normalien AG.
The company places great emphasis on exceptional precision and durability in the active elements. In addition to fully automated production, the manufacturing process also includes manual post-processing, i.e. operations such as micro-blasting, polishing and PVD coating. All of which extend the service life of its products. Another of its trump cards is the ability to guarantee rapid availability. Steinel can provide comprehensive spare parts management, including warehousing and on-site consignment stock. All of which guarantees its customers rapid access to spare parts. The CAD/CAM processes guarantee that all spare parts fit perfectly.
When designing and manufacturing tool modules and complete punching tools for its customers, Steinel supports them with an in-depth analysis of their production processes and of potential ways to optimise those processes. This boosts production efficiency, it improves product quality and it reduces downtime.
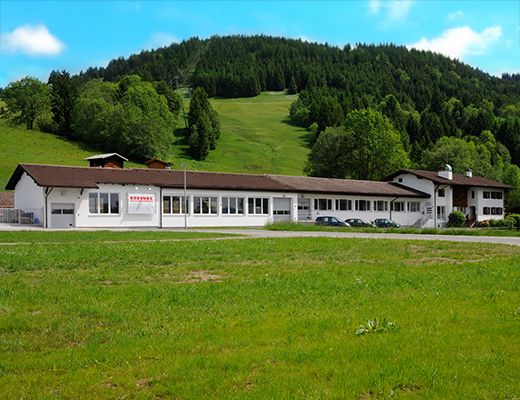
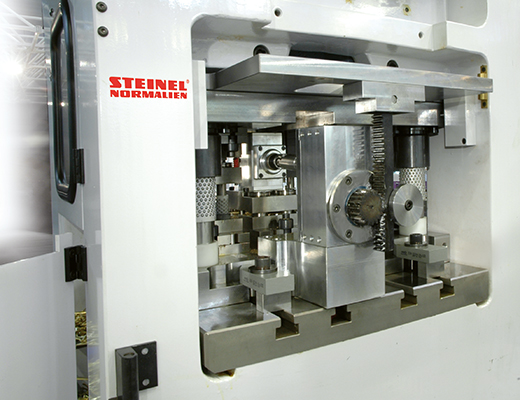
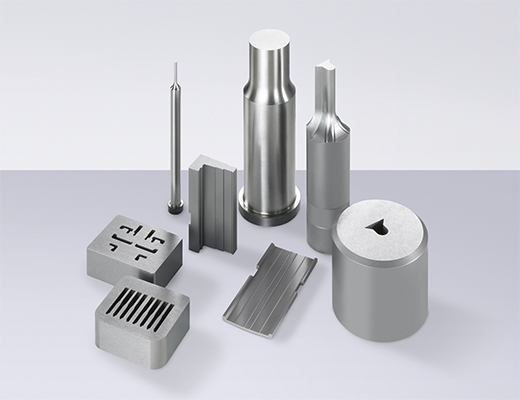
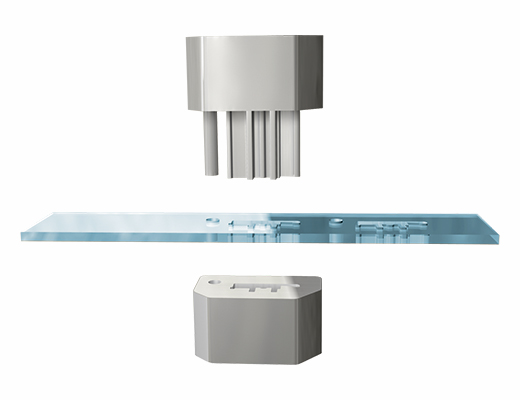
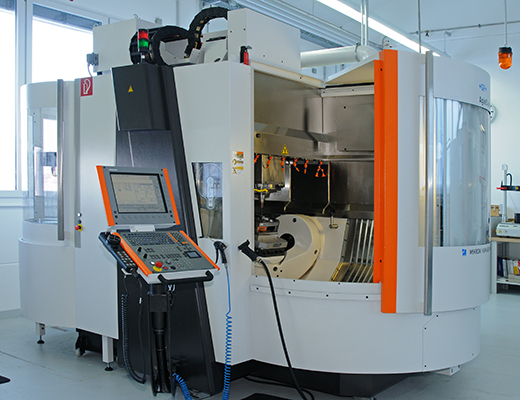
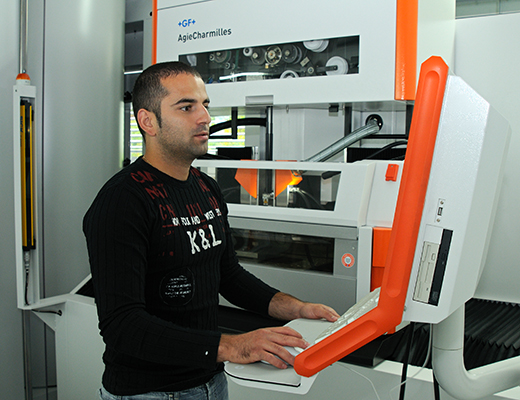
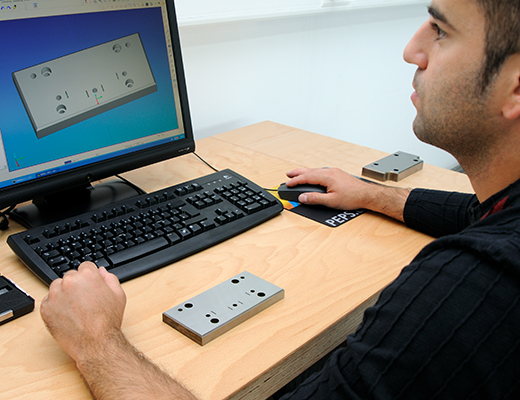
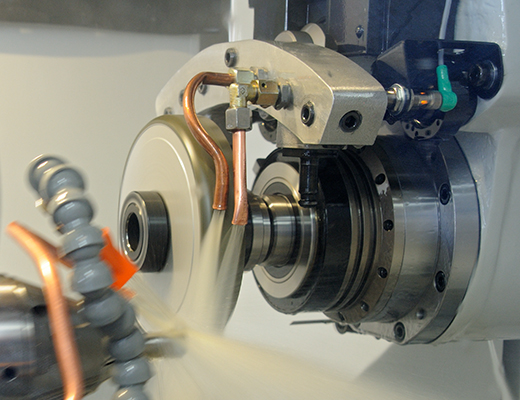
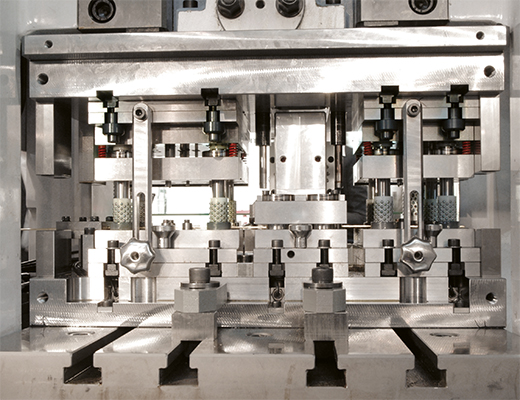
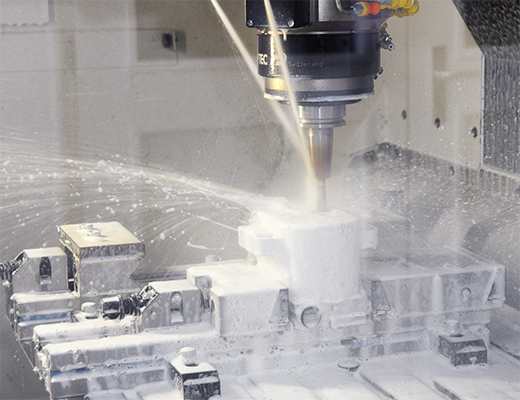
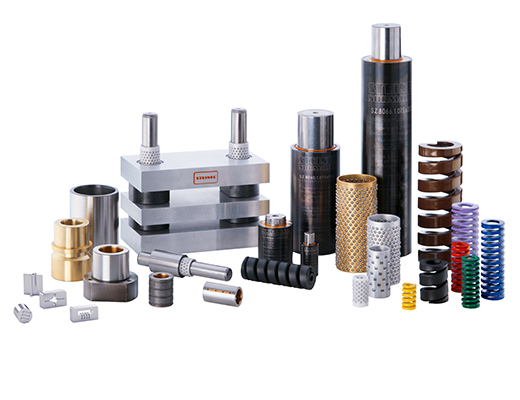
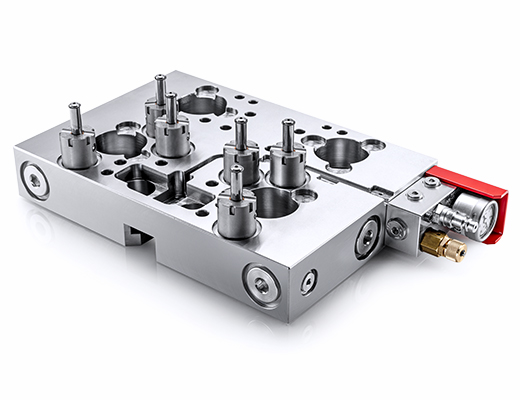
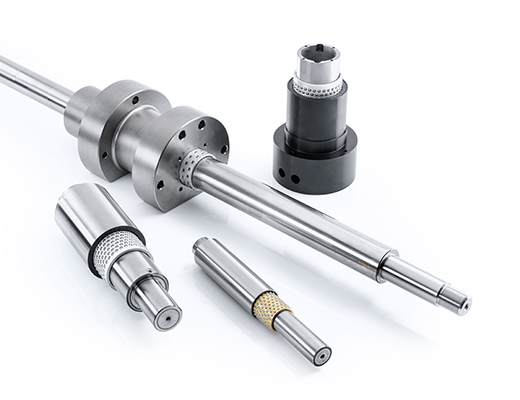
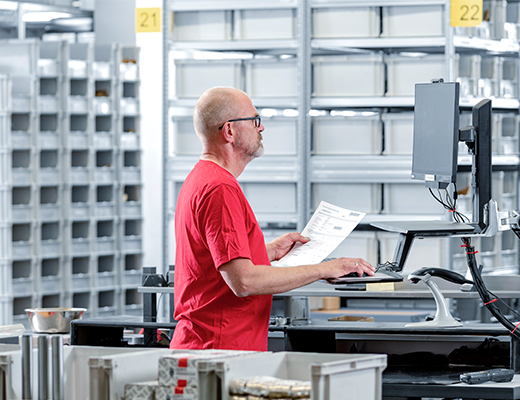
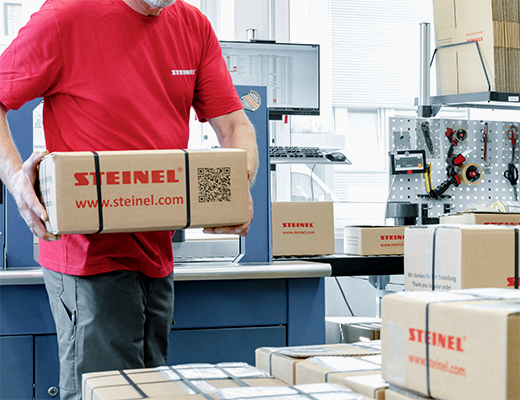
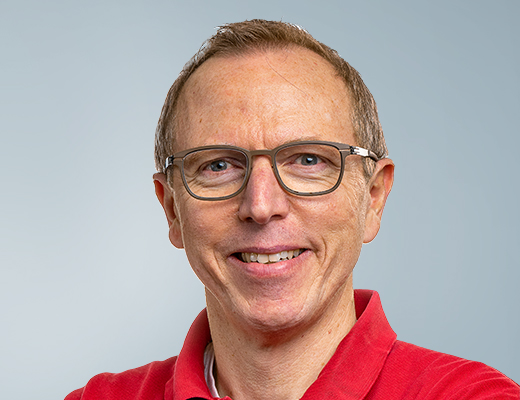
The fourth generation takes the helm
In 2002, almost 80 years after the company was founded by Bernhard Steinel, it becomes a public limited company. The shares in this PLC (an AG in Germany) remain in the possession of the previous shareholders and will not be traded on the stock exchange. Wolfgang Rau, previously Managing Director of the limited company (the GmbH), becomes a member of the Board of Management. Bernhard A. Steinel, the son of the company founder, is at the head of the three-person Supervisory Board. In 2012, a significant change takes place in the executive management team at Steinel: Christoph Neudörffer, the great-grandson of the founder, joins the Board of Management. This means that after a good decade and a half under external management, a member of the founding family will once again be taking over the management of the company. Following in the footsteps of the company founder Bernhard Steinel and of his son Bernhard A. Steinel, the fourth generation is now joining the company. The third Steinel generation did not get involved in the management of the company.
Read moreSolutions for machine & plant construction
Despite the fact that STEINEL products are best known in relation to stamping and forming technology, their components and systems are also ideally suited for use in other sectors. After all, high-precision sequences of movements and durability are also important in many other applications. Since the early 2000s, increasing use has been made of customised solutions based on STEINEL guides and its complex range of structural attachments. Examples of these other sectors include measurement technology, packaging machines for the pharmaceutical and food industries and assembly equipment for the production of batteries and fuel cells.
There is also no limit to the list of possible applications for these customised solutions, nor to their diversity. For example, STEINEL ball guides can be used in any installation position for longitudinal and rotary movements to facilitate extremely fast cycle speeds while STEINEL roller guides are ideal for linear movements and high lateral forces. Depending on requirements, STEINEL guides can be coated, dirt-protected and high strength. They can also be fitted with integrated seals and may also be stainless or acid-resistant. The company portfolio even includes guides electrically insulated with ceramic balls. There are virtually no limits for these guides, not even in terms of their shapes and dimensions.
For complex applications or special requirements, the experts at STEINEL can provide appropriate solutions. right from the design, development and construction stages. The experience gained over decades in stamping and forming technology and the expertise derived from a plethora of sectors is also translating into a success factor in other industries. And demand is huge, equating to gigantic potential. What started out with individual projects is now expanding into yet another core business. This shows that the management team is continuing to pursue its long-standing strategy which is to intensify activities beyond the scope of stamping and forming technology sector.
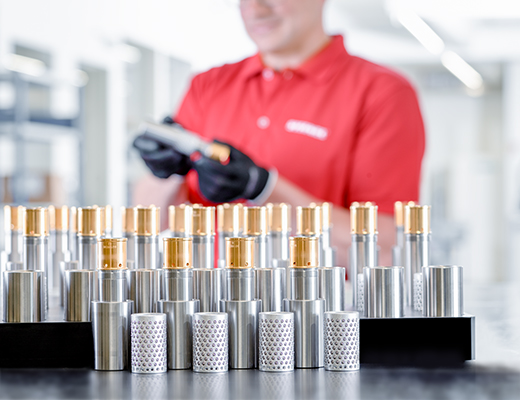
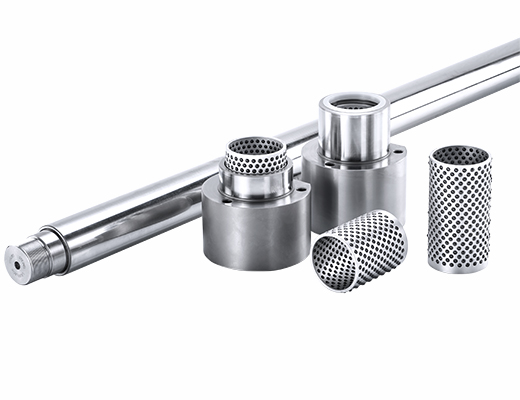
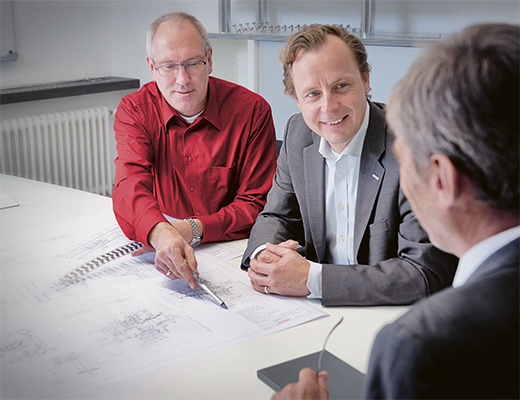
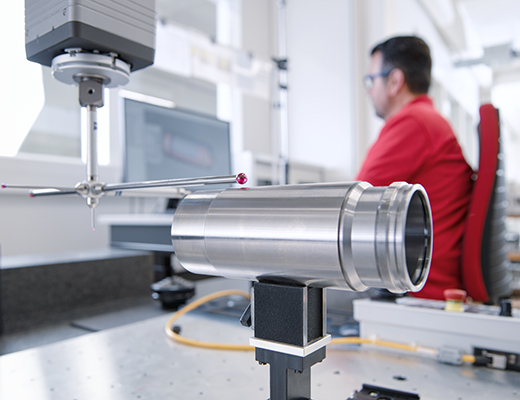
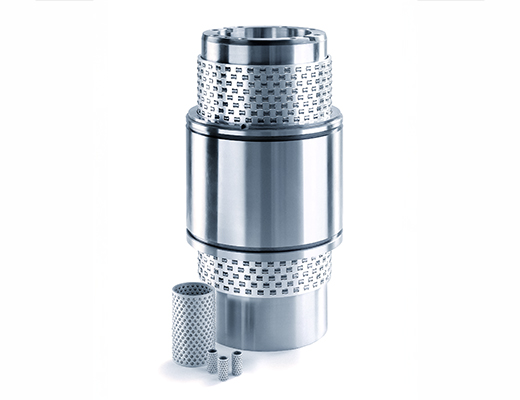
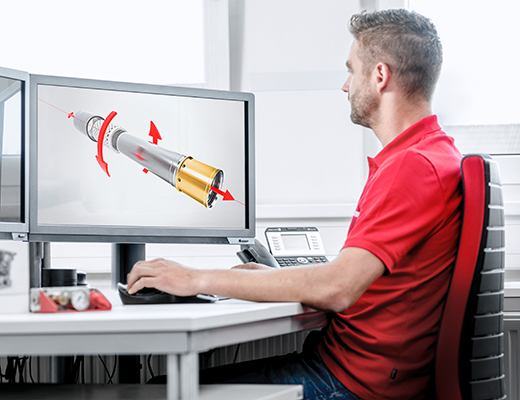
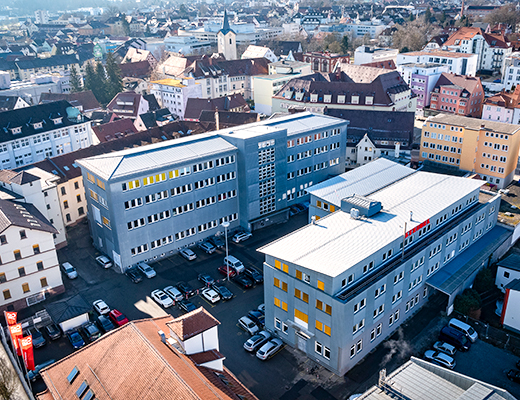
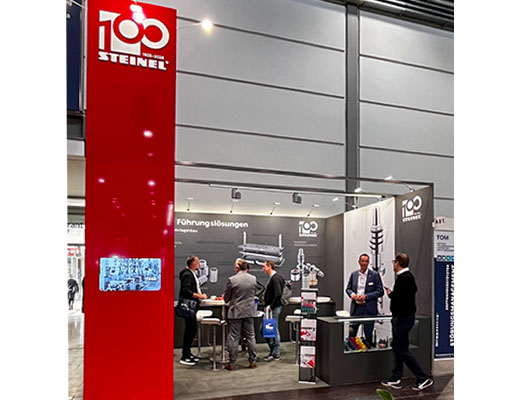
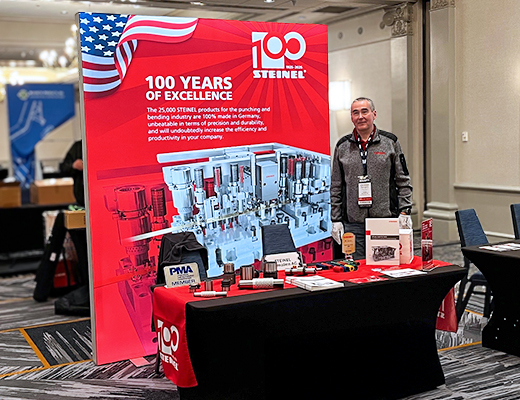
STEINEL celebrates its centennial
STEINEL’s anniversary year has officially begun – both at the company premises and with the first international event. In the coming months, STEINEL will continue to mark its 100th anniversary with special trade fair appearances and a range of celebratory activities. The highlight will be Blechexpo 2025, where STEINEL will demonstrate its commitment to both innovation and tradition. This anniversary year will offer many exciting insights and memorable moments – we look forward to sharing them with you.